Reducing Shrinkage with Advanced Inventory Management Systems
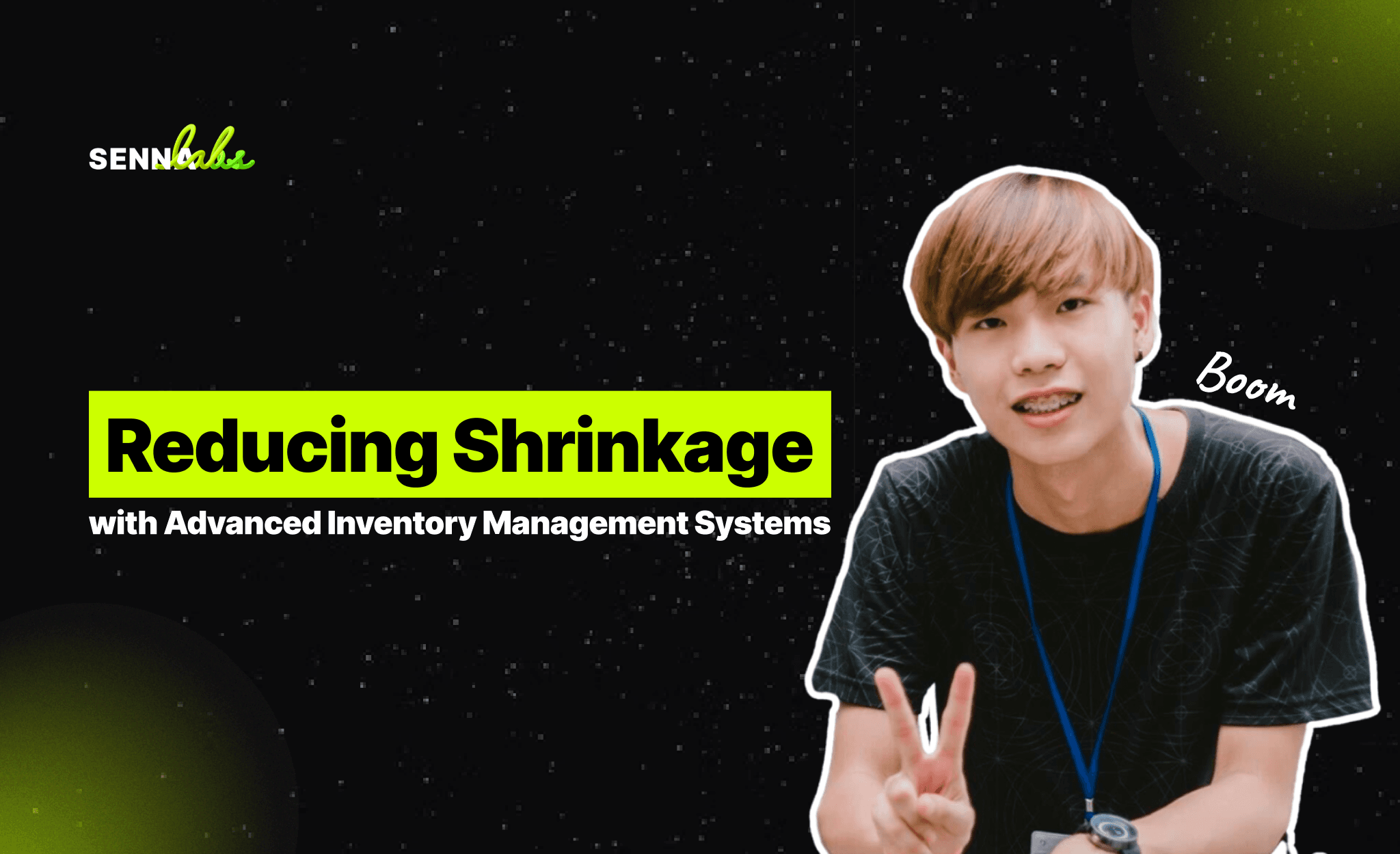
Shrinkage is a persistent challenge in retail, often caused by theft, spoilage, or inventory mismanagement. The financial impact of shrinkage extends beyond lost revenue—it can also erode customer trust and strain operational efficiency. Modern inventory management systems, equipped with advanced technologies such as RFID tags, real-time tracking, and automated monitoring, offer powerful tools to combat shrinkage and enhance control over inventory.
In this article, we’ll explore how advanced inventory management systems help minimize shrinkage and provide a real-world example of a convenience store that successfully reduced losses by implementing RFID tags for high-value items.
The Impact of Shrinkage on Retail
Shrinkage remains one of the most significant challenges for retailers. Common sources of shrinkage include:
-
Theft: Both employee theft and shoplifting contribute to inventory loss, particularly for high-value or easily concealable items.
-
Spoilage: Perishable goods, such as food and beverages, are prone to spoilage if not managed carefully.
-
Inventory Mismanagement: Errors in stock counting, data entry, or handling can lead to misplaced or unaccounted-for inventory.
-
Vendor Fraud: Discrepancies during the receiving process, such as short shipments or damaged goods, can also contribute to shrinkage.
Shrinkage directly impacts profitability, and reducing it requires proactive strategies and advanced technologies.
How Advanced Inventory Management Systems Minimize Shrinkage
Modern inventory tools use automation, data tracking, and advanced analytics to address the root causes of shrinkage. Key features include:
1. Real-Time Inventory Visibility
Advanced systems provide real-time updates on inventory levels, making it easier to track stock movements and detect discrepancies. This visibility helps identify missing items quickly and accurately.
-
Benefit: Reduces undetected losses caused by theft or errors in handling.
2. RFID Technology
Radio-frequency identification (RFID) tags are a powerful tool for monitoring high-value or theft-prone items. RFID systems track inventory throughout the supply chain and in-store, providing precise location data and improving accountability.
-
Benefit: Reduces theft by enhancing visibility and control over individual items.
3. Automated Stock Counts
Automation eliminates manual stock counting errors, ensuring accurate records of inventory at all times. Frequent automated counts make it easier to spot anomalies and investigate potential issues.
-
Benefit: Minimizes shrinkage caused by mismanagement or counting inaccuracies.
4. Spoilage Tracking and Alerts
For perishable goods, advanced systems can monitor expiration dates and send alerts for items nearing spoilage. This ensures that products are sold or used before they expire.
-
Benefit: Reduces losses from unsellable stock due to spoilage.
5. Loss Prevention Analytics
Inventory systems equipped with analytics tools can identify patterns in shrinkage, such as high theft rates for specific items or locations. Retailers can use these insights to implement targeted loss prevention strategies.
-
Benefit: Addresses shrinkage proactively by identifying and mitigating risks.
6. Integration with Security Systems
Advanced inventory tools can integrate with store security systems, such as cameras or alarm tags. This creates a comprehensive solution for monitoring and protecting inventory.
-
Benefit: Enhances theft prevention by combining physical security measures with inventory data.
Use Case: Convenience Store Reduces Shrinkage with RFID Tags
The Problem:
A regional convenience store chain struggled with high shrinkage rates, particularly for high-value items such as electronics, premium alcohol, and personal care products. Traditional inventory tracking methods were insufficient to monitor these items effectively, leading to frequent losses and reduced profitability.
The Solution:
The store implemented an advanced inventory management system with RFID technology for its high-value inventory. Key features included:
-
RFID Tagging: Each high-value item was tagged with an RFID chip, enabling real-time tracking and improved accountability.
-
Automated Alerts: The system sent notifications for unauthorized movement of tagged items, triggering security measures.
-
Integrated Reporting: Loss prevention teams used analytics dashboards to identify theft patterns and adjust security strategies accordingly.
The Result:
The RFID system delivered significant improvements:
-
Reduced Shrinkage: Losses for high-value items decreased by 35%, as enhanced visibility deterred theft and improved accountability.
-
Improved Operational Efficiency: Automated tracking replaced manual stock checks, saving staff time and reducing errors.
-
Enhanced Loss Prevention: The system provided actionable insights that helped the store implement targeted security measures, such as adjusting camera placement and increasing staff oversight during high-theft periods.
-
Increased Profitability: Lower shrinkage rates translated into higher margins and improved bottom-line performance.
Key Features to Look for in Advanced Inventory Management Systems
Retailers seeking to minimize shrinkage should prioritize systems with the following features:
-
Real-Time Tracking: Provides instant visibility into inventory levels and movements.
-
RFID Integration: Enhances control over high-value items by enabling precise tracking and monitoring.
-
Automated Alerts: Notifies managers of anomalies, such as unauthorized item removal or stock discrepancies.
-
Analytics and Reporting: Offers insights into shrinkage patterns, helping retailers implement effective loss prevention strategies.
-
Spoilage Monitoring: Tracks perishable inventory and alerts staff before items expire.
-
Scalability: Supports growth by managing larger inventories or multiple locations effectively.
Why Shrinkage Management Matters for Retail Success
Shrinkage is a direct drain on profitability, and reducing it is essential for maintaining financial health and operational efficiency. Key benefits of advanced inventory management systems include:
-
Increased Profitability: Lower shrinkage rates directly improve margins.
-
Enhanced Customer Experience: Ensuring inventory availability by minimizing losses leads to better customer satisfaction.
-
Improved Operational Control: Automation and real-time tracking simplify inventory management and reduce manual errors.
-
Proactive Loss Prevention: Advanced analytics and tracking tools help retailers address shrinkage risks before they escalate.
Conclusion:
Advanced inventory management systems offer powerful tools for minimizing shrinkage caused by theft, spoilage, or mismanagement. By leveraging technologies like RFID, real-time tracking, and automated alerts, retailers can gain greater control over their inventory and reduce losses.
For the convenience store in our use case, implementing RFID technology resulted in a 35% reduction in shrinkage, improved efficiency, and increased profitability. This success demonstrates the transformative potential of modern inventory tools in addressing shrinkage challenges.
If your business struggles with inventory losses, investing in advanced inventory management systems can help you safeguard your stock, improve operations, and boost your bottom line.
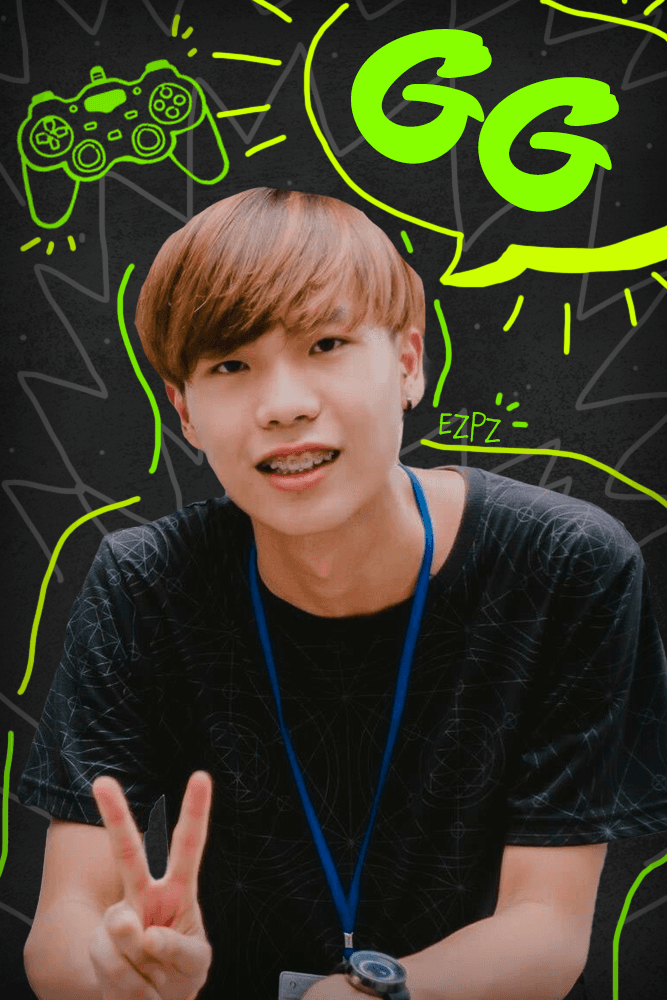
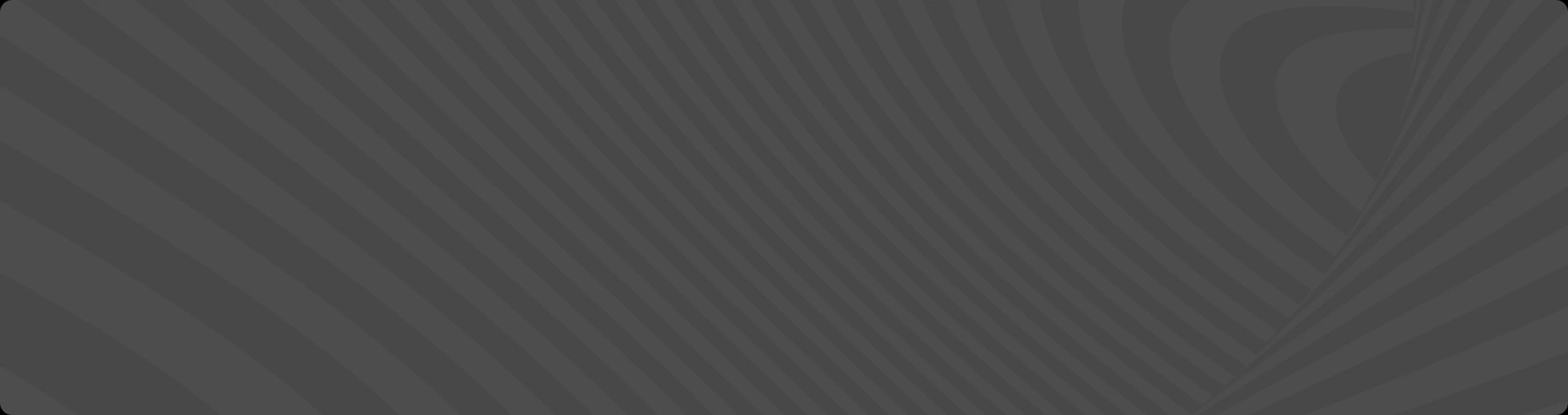
Subscribe to follow product news, latest in technology, solutions, and updates
Other articles for you
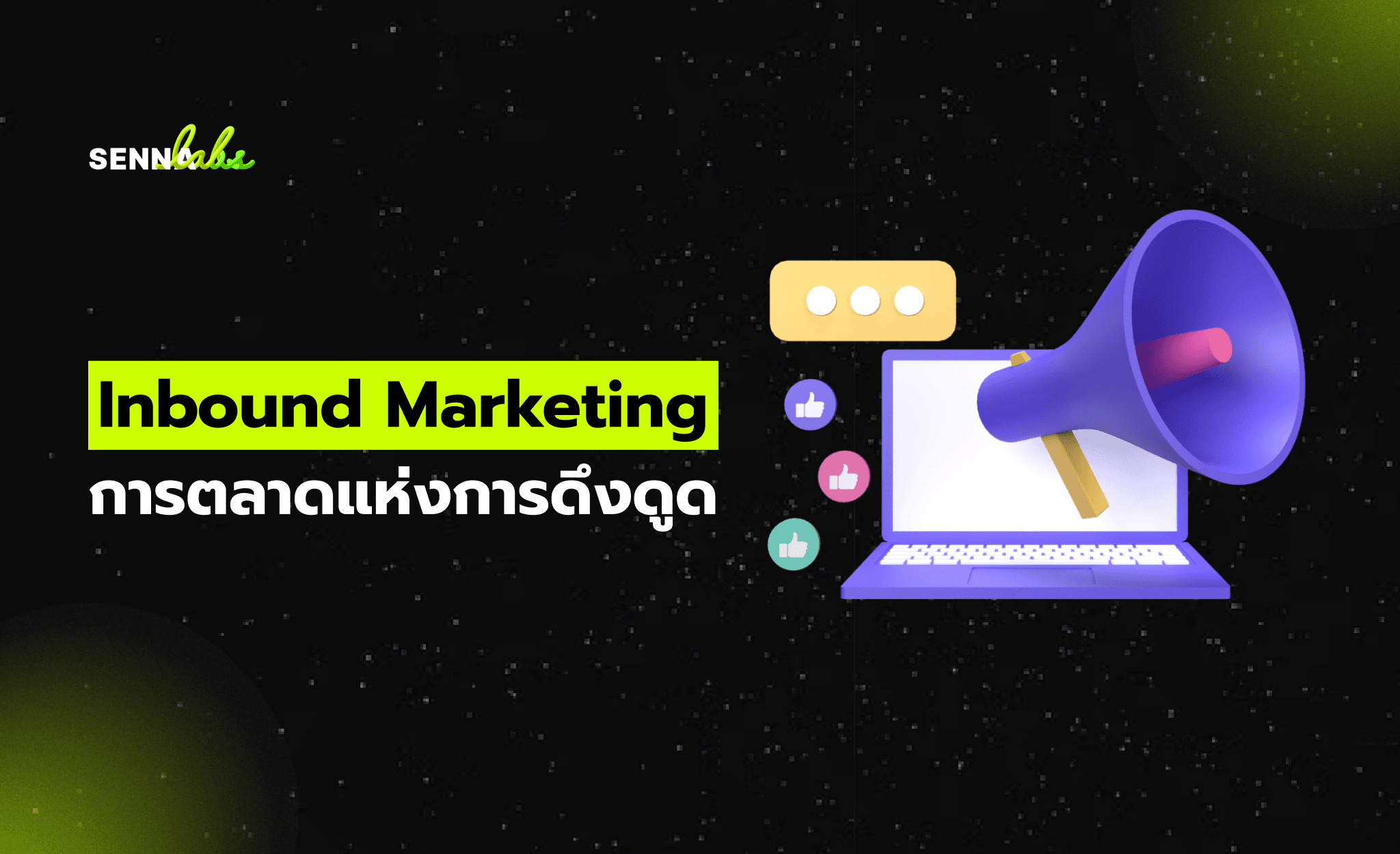
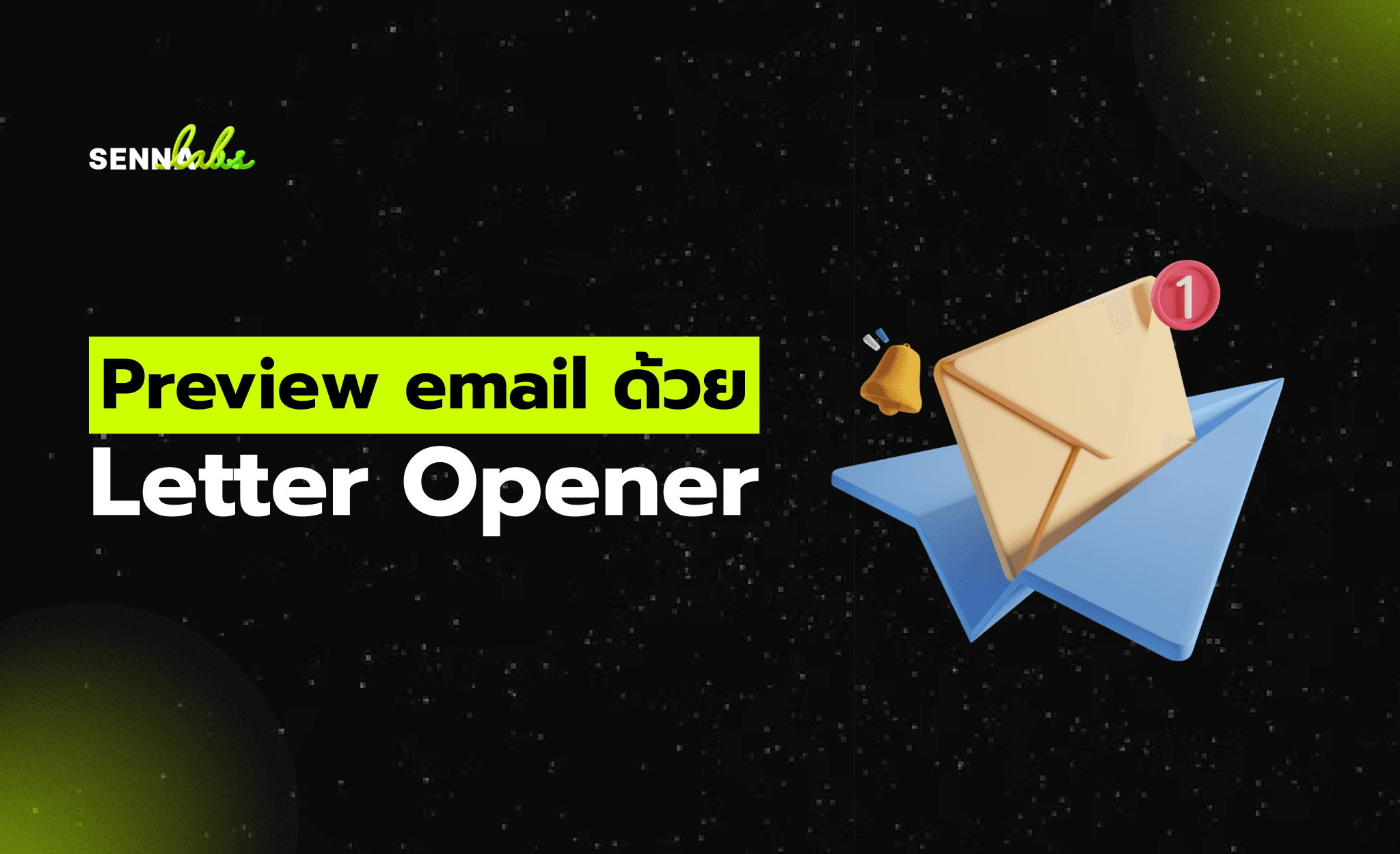
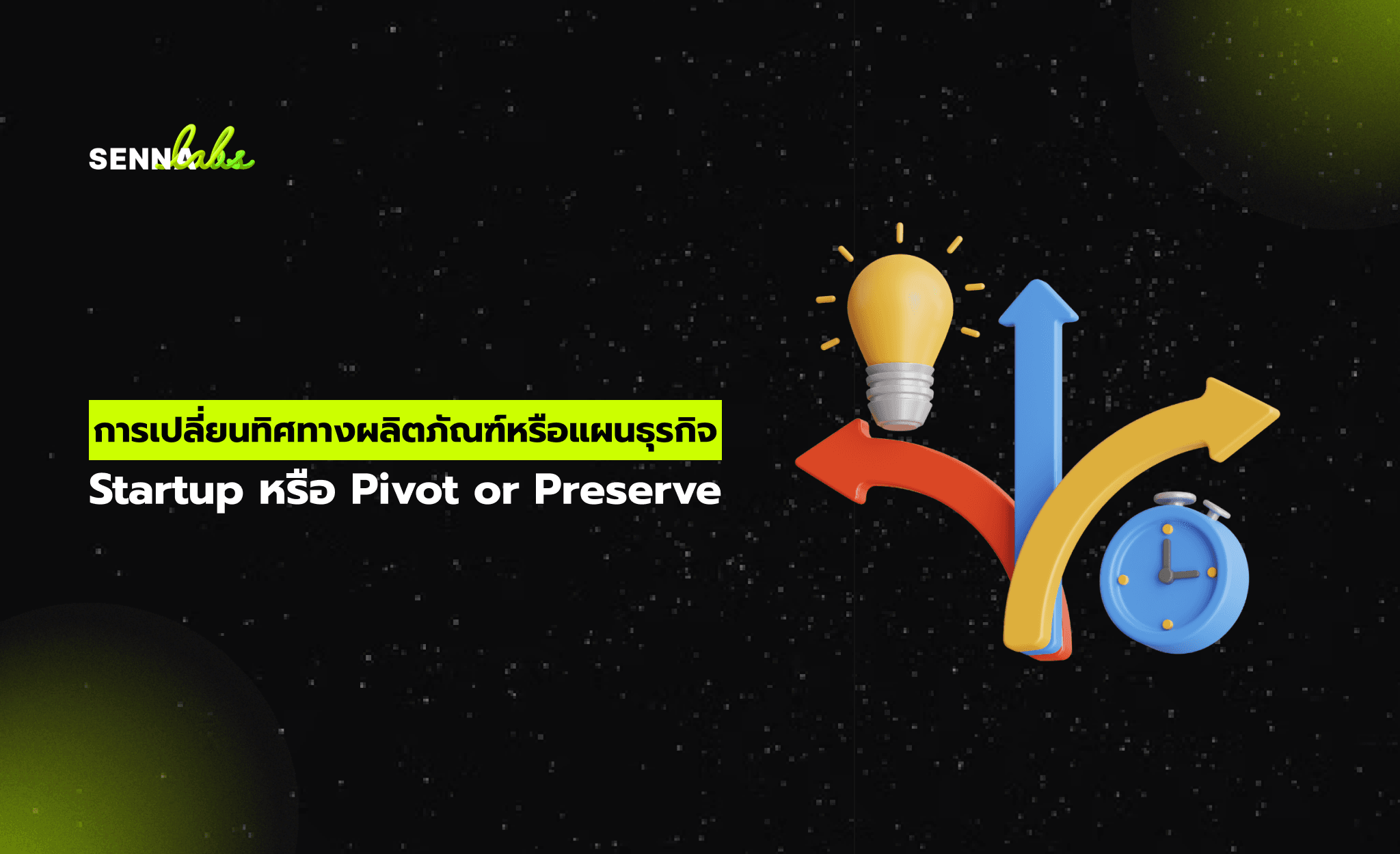
Let’s build digital products that are simply awesome !
We will get back to you within 24 hours!Go to contact us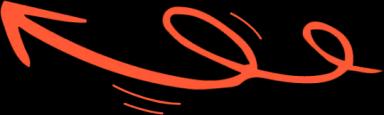
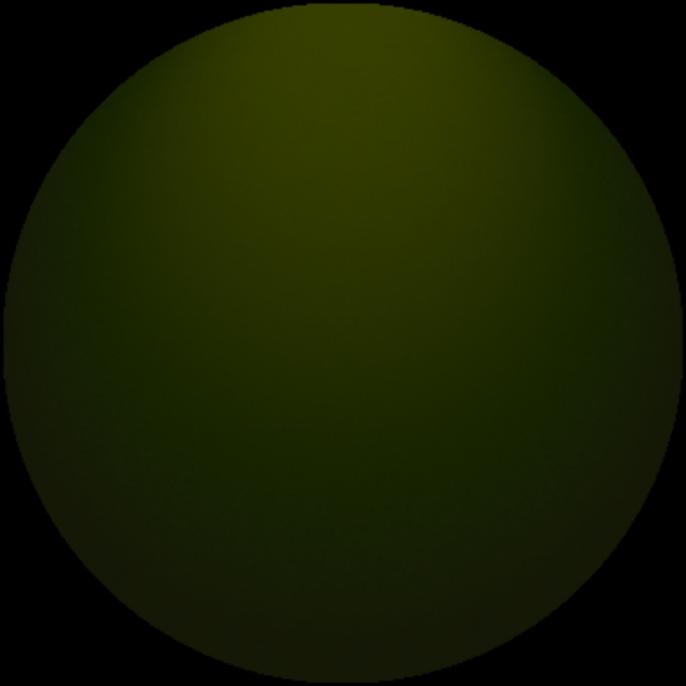
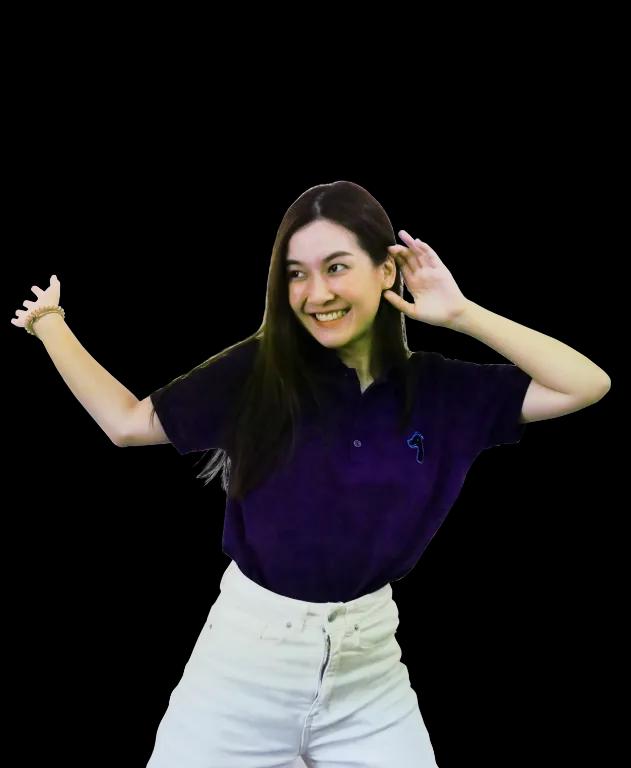
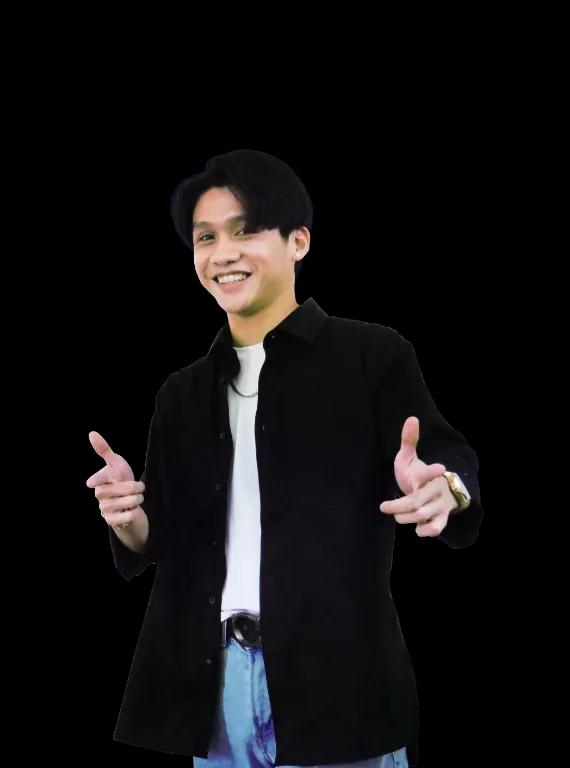
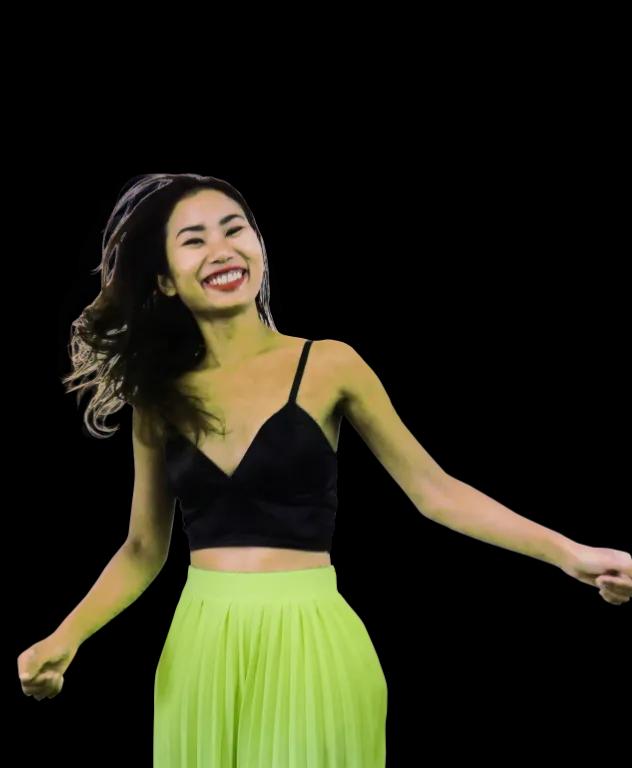
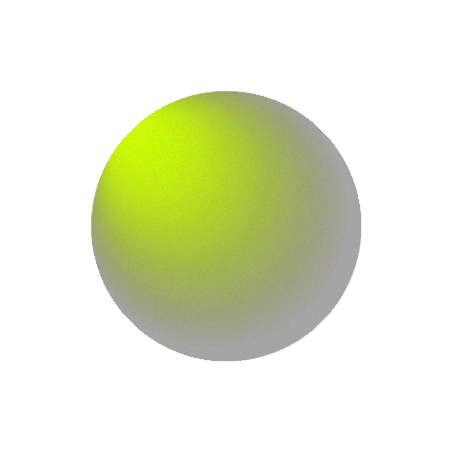
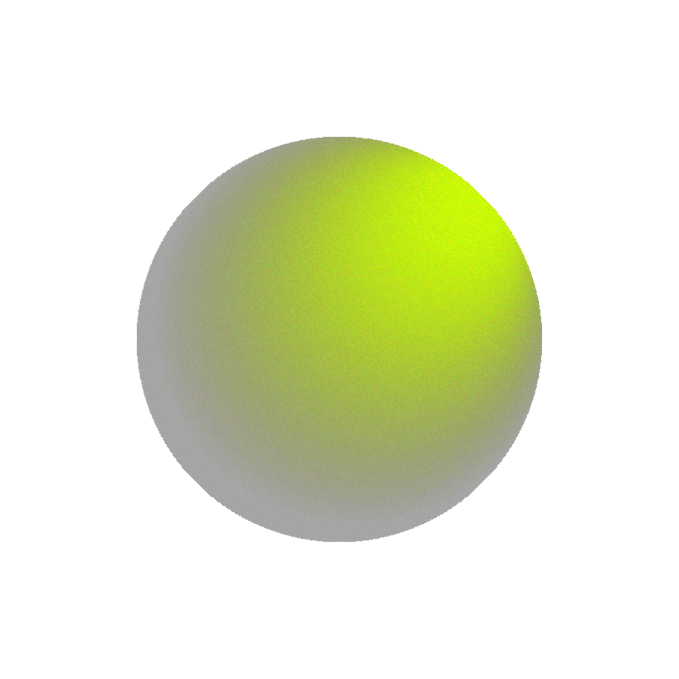
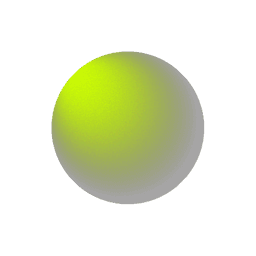
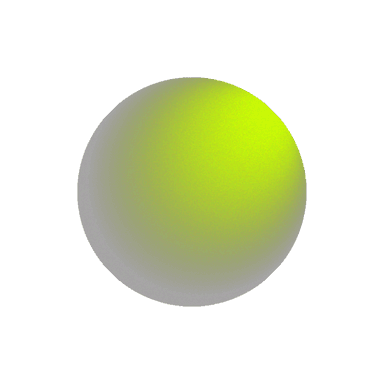
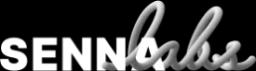