Driving Innovation in Food Production with Custom Software
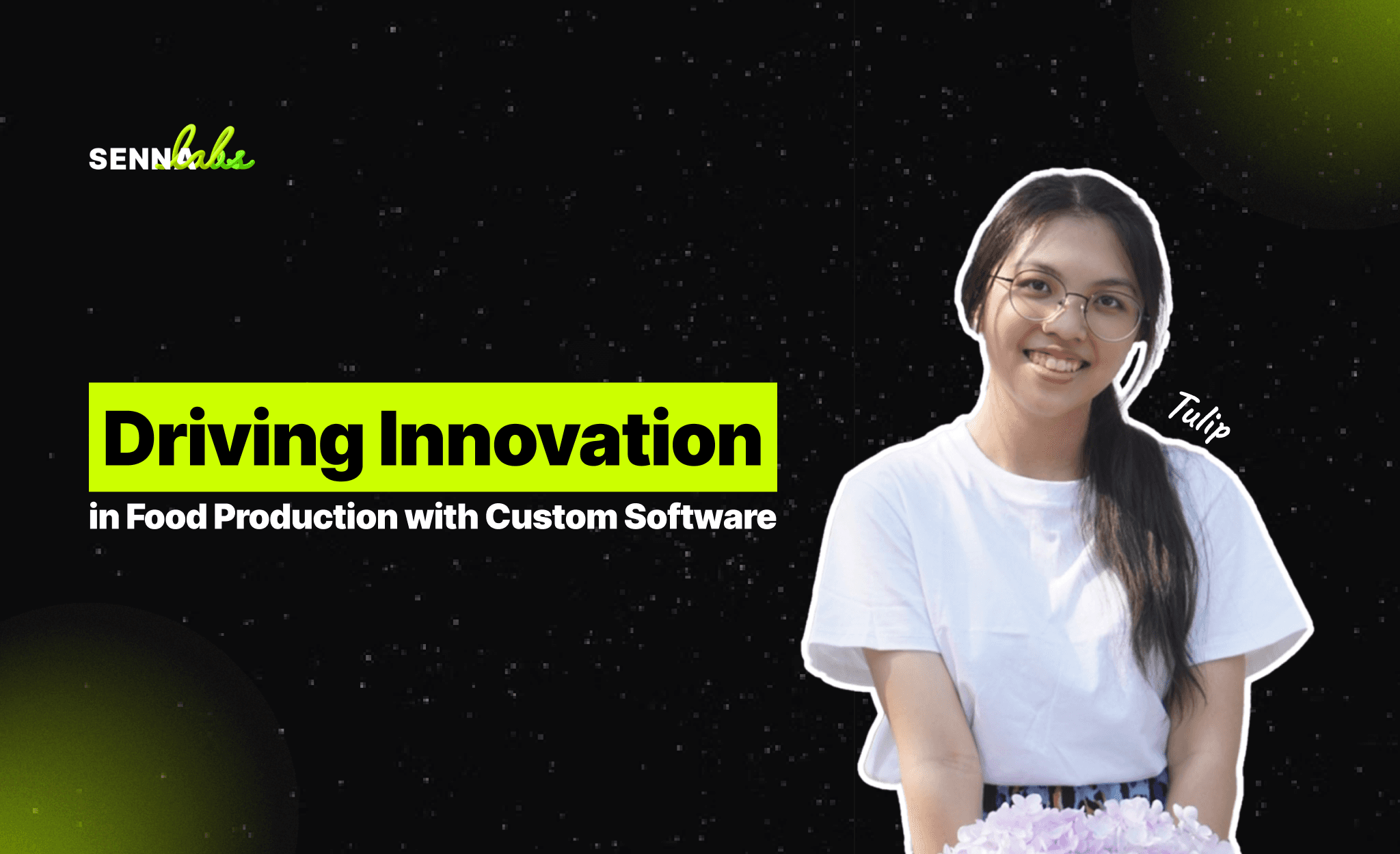
The food production industry faces increasing pressure to meet growing demand while ensuring product quality, regulatory compliance, and operational efficiency. In this fast-paced environment, traditional methods and generic software solutions often fall short. Custom software development is emerging as a transformative tool, enabling food manufacturers to innovate, streamline processes, and maintain stringent quality and safety standards.
This article explores how custom software solutions are revolutionizing food production, focusing on their role in optimizing operations, ensuring compliance with regulations, and enhancing product quality. It also highlights a use case where a food processing company implemented a custom quality control system to track production data and maintain product consistency.
Challenges in Food Production
The food production industry faces unique challenges that require tailored solutions:
1. Ensuring Product Quality and Consistency
Maintaining consistent quality across batches is critical for customer satisfaction and brand reputation. Manual processes often fail to deliver the precision required.
2. Meeting Safety and Regulatory Requirements
Compliance with food safety standards, such as HACCP, FDA, and ISO, requires meticulous tracking, reporting, and documentation.
3. Optimizing Production Efficiency
Food manufacturers must balance the need for high output with minimizing waste, reducing costs, and improving efficiency.
4. Managing Supply Chain Complexity
Coordinating suppliers, raw materials, and logistics is challenging, especially when dealing with perishable goods.
How Custom Software Drives Innovation in Food Production
Custom software is designed to address the specific needs of food manufacturers, offering a range of features that optimize processes and ensure compliance.
1. Quality Control Automation
Custom quality control systems monitor production in real time, ensuring consistency and detecting defects early.
-
Features:
-
Real-time monitoring of production parameters.
-
Automated alerts for deviations in quality standards.
-
Integration with sensors and IoT devices for precision tracking.
2. Regulatory Compliance Management
Custom software automates compliance tracking and documentation, simplifying audits and ensuring adherence to safety regulations.
-
Features:
-
Automatic generation of compliance reports.
-
Traceability tools to track the source of raw materials.
-
Real-time alerts for potential non-compliance.
3. Production Process Optimization
Custom solutions streamline workflows, optimize resource allocation, and improve production scheduling.
-
Features:
-
Real-time data on production efficiency and output.
-
Predictive analytics to identify potential bottlenecks.
-
Automated scheduling and resource management.
4. Supply Chain Integration
Custom software integrates supply chain data, ensuring seamless coordination between suppliers, production lines, and distribution channels.
-
Features:
-
Inventory tracking and replenishment alerts.
-
Supplier performance monitoring.
-
Dynamic adjustments to raw material procurement based on demand forecasts.
5. Data-Driven Decision Making
Custom software provides actionable insights into production trends, waste management, and cost optimization through advanced analytics.
-
Features:
-
Custom dashboards with KPIs for managers.
-
AI-driven recommendations for process improvements.
-
Waste and cost tracking for sustainability initiatives.
Use Case: Quality Control System for a Food Processing Company
The Challenge
A food processing company producing ready-to-eat meals faced challenges in maintaining product consistency and ensuring compliance with food safety standards.
-
Inconsistent Quality: Variability in production batches led to customer complaints.
-
Manual Processes: Quality checks were performed manually, increasing the risk of errors and delays.
-
Regulatory Pressure: Meeting compliance requirements required significant time and effort, impacting operational efficiency.
The Solution
The company implemented a custom quality control system to track production data, ensure consistency, and automate compliance processes.
Key Features of the Custom Software:
-
Real-Time Quality Monitoring:
-
Integrated sensors tracked production parameters, such as temperature, humidity, and ingredient ratios.
-
Alerts notified operators of deviations from preset standards.
-
Automated Compliance Reporting:
-
Generated detailed reports for audits and certifications.
-
Maintained a digital log of quality checks for traceability.
-
Production Analytics:
-
Provided insights into process efficiency and areas for improvement.
-
Monitored waste levels and suggested adjustments to minimize losses.
-
Batch Tracking and Traceability:
-
Enabled end-to-end tracking of raw materials and finished products.
-
Improved response time during recalls or investigations.
The Results
-
Improved Product Consistency:
-
Real-time monitoring and automated quality checks eliminated variability in production batches.
-
Enhanced Compliance:
-
Automated documentation ensured readiness for audits and reduced the risk of penalties.
-
Optimized Efficiency:
-
Insights from production analytics helped the company reduce waste and improve resource utilization.
-
Strengthened Customer Trust:
-
Consistently high-quality products and transparent processes boosted customer confidence in the brand.
Benefits of Custom Software in Food Production
1. Improved Quality Assurance
Custom solutions ensure consistent quality by automating monitoring and quality control processes.
2. Streamlined Compliance
Automated tracking and reporting simplify regulatory adherence, saving time and reducing the risk of errors.
3. Increased Efficiency
Real-time data and analytics optimize production processes, reducing waste and maximizing output.
4. Enhanced Traceability
Custom software provides end-to-end visibility into the supply chain, ensuring accountability and transparency.
5. Sustainability Goals
Custom solutions help manufacturers identify and reduce waste, supporting sustainability initiatives.
Conclusion
The food production industry requires innovation and precision to meet the demands of quality, safety, and efficiency. Custom software development is a critical tool for achieving these goals, enabling manufacturers to streamline processes, ensure compliance, and deliver consistently high-quality products.
The food processing company’s success with a custom quality control system demonstrates the transformative potential of tailored technology. By automating monitoring, enhancing traceability, and optimizing production, the company achieved greater efficiency and strengthened its reputation for quality.
As the food production industry evolves, custom software will continue to drive innovation, supporting manufacturers in navigating challenges and seizing opportunities for growth. For food producers aiming to stay competitive and sustainable, investing in custom software is a step toward a more efficient and resilient future.
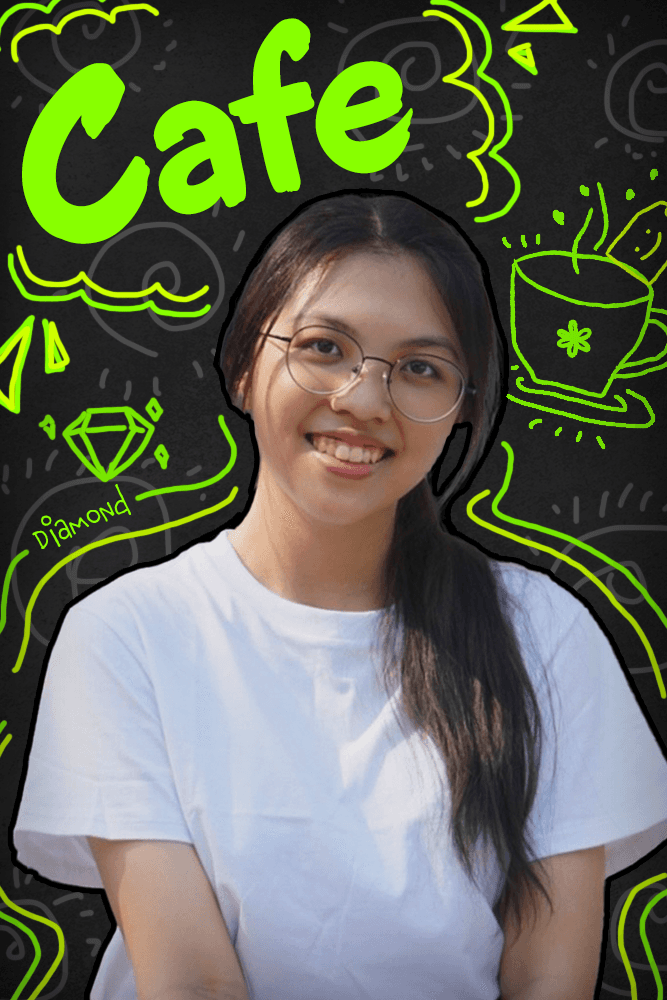
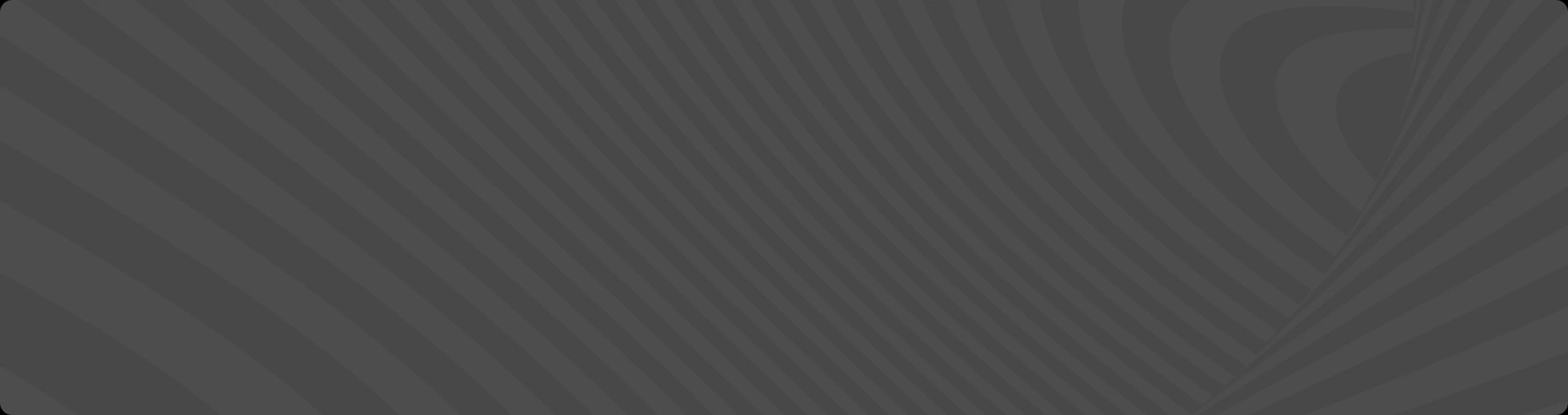
Subscribe to follow product news, latest in technology, solutions, and updates
บทความอื่นๆ
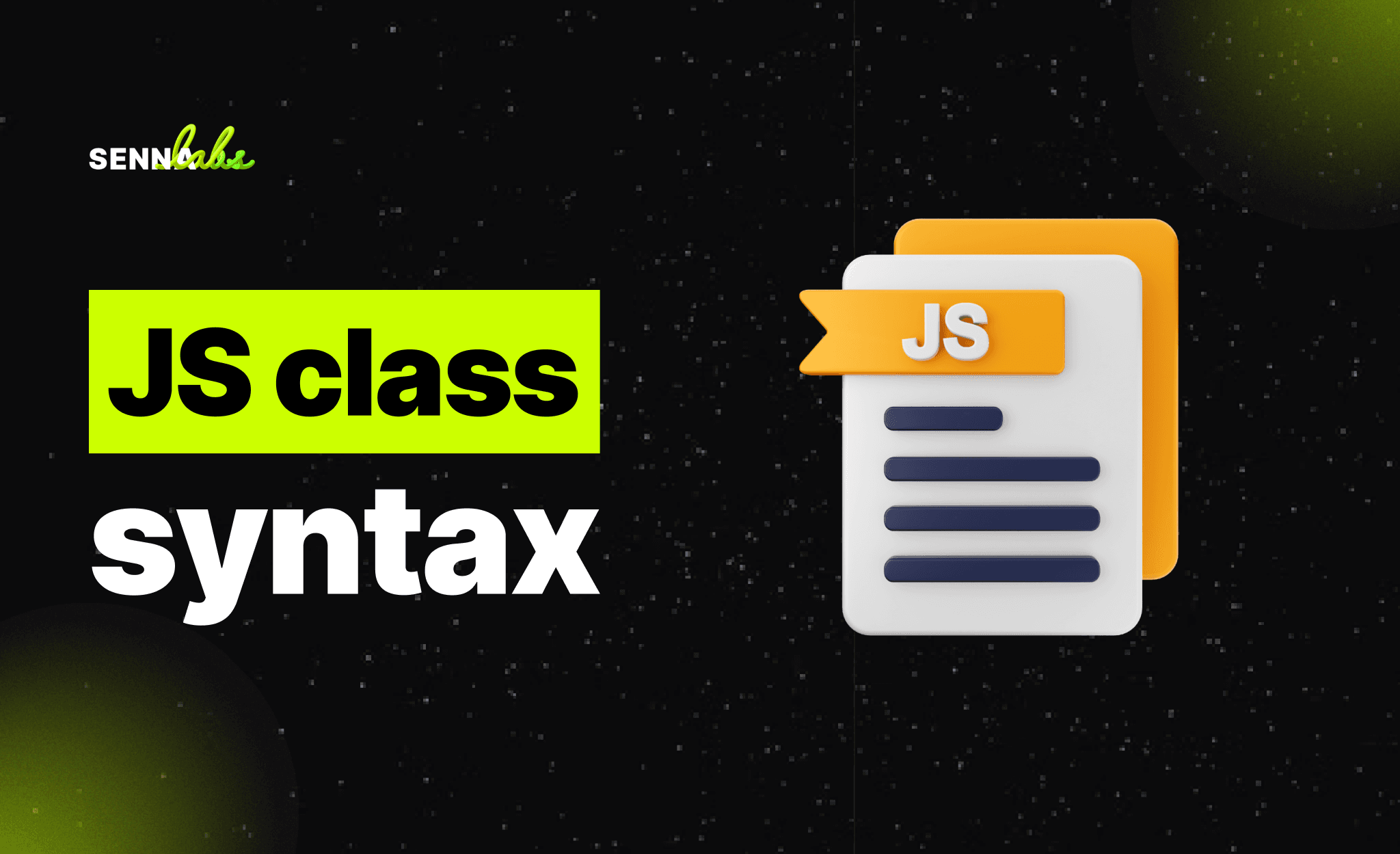
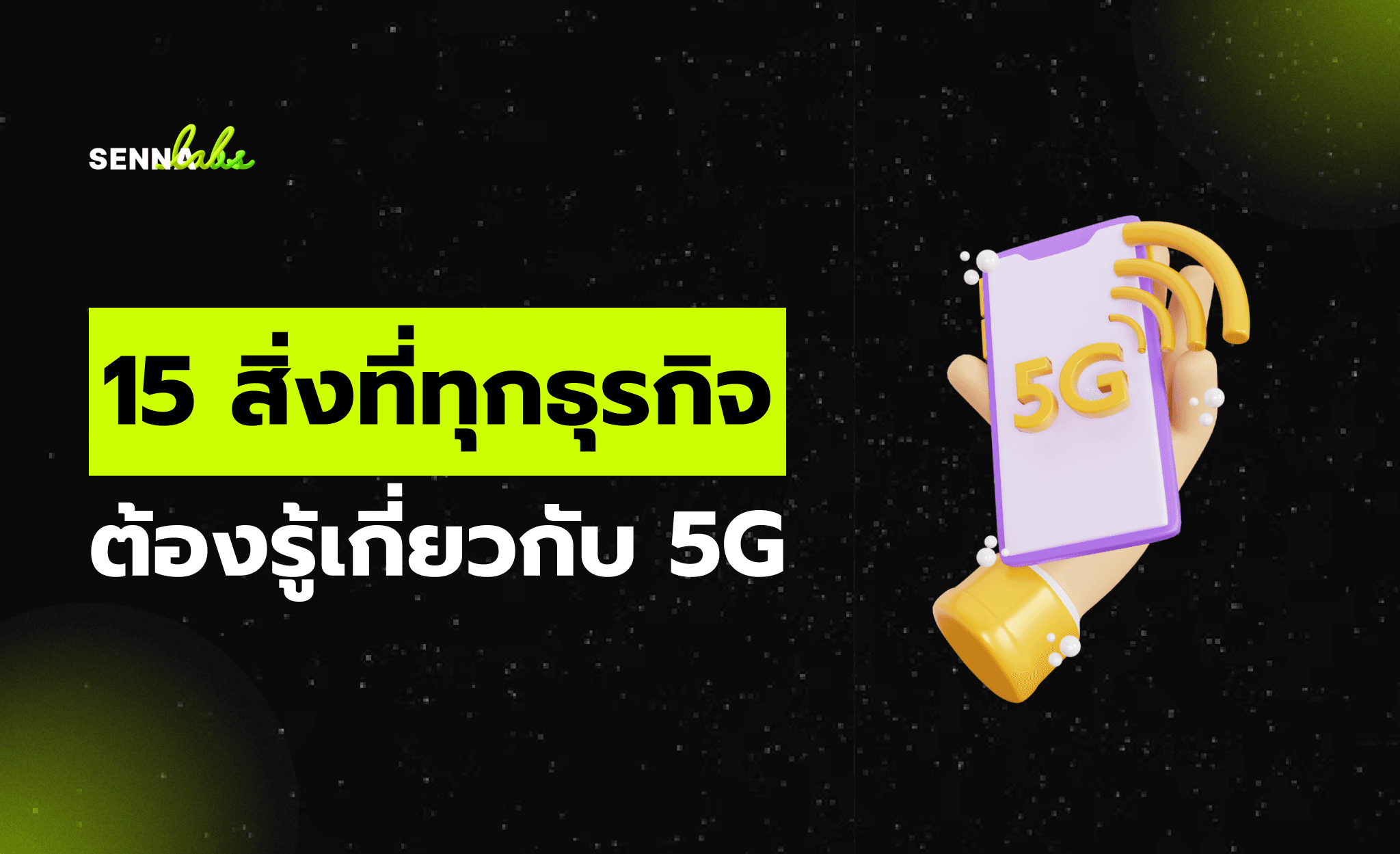
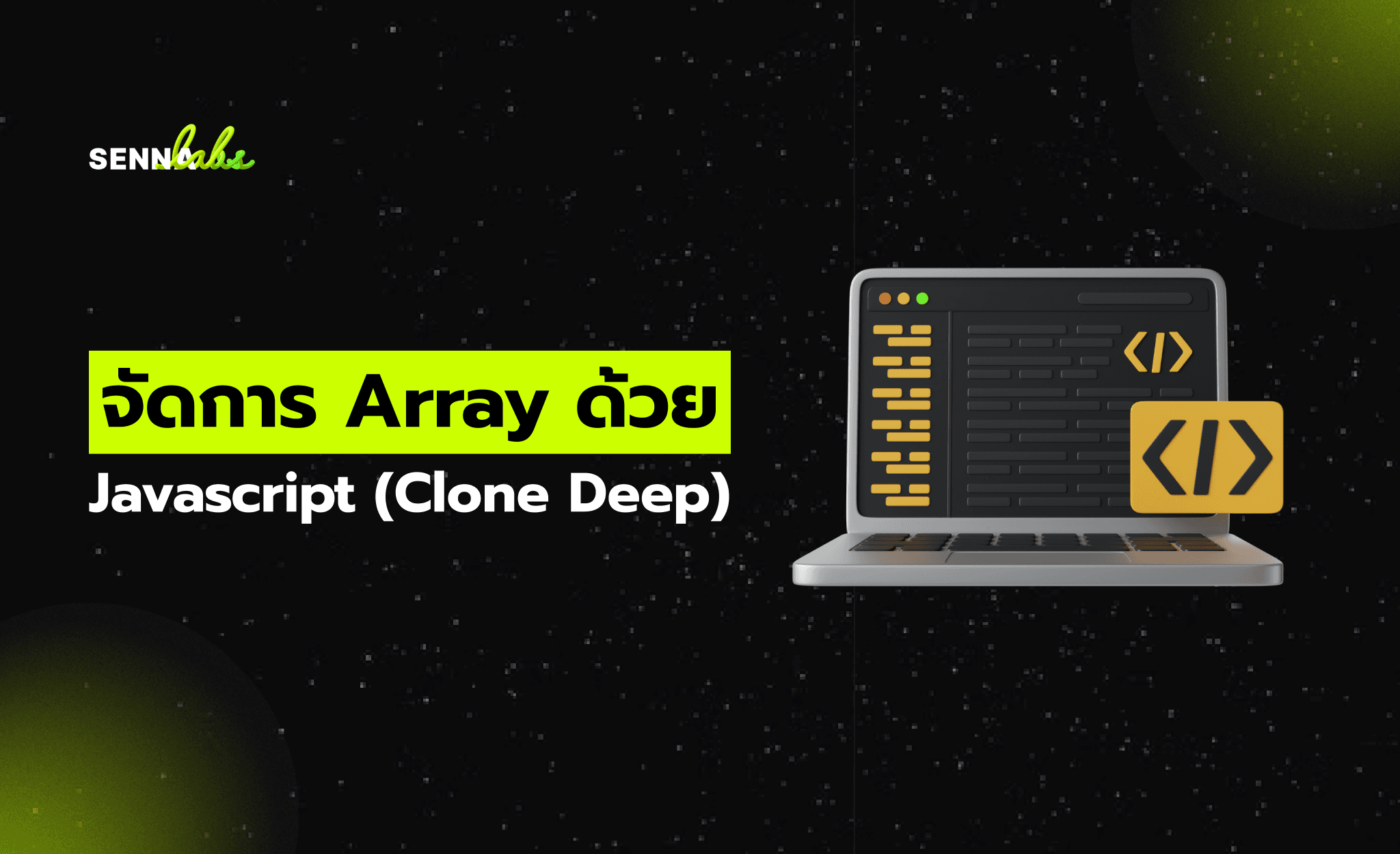
Let’s build digital products that are simply awesome !
We will get back to you within 24 hours!ติดต่อเรา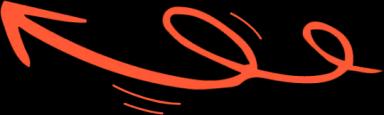
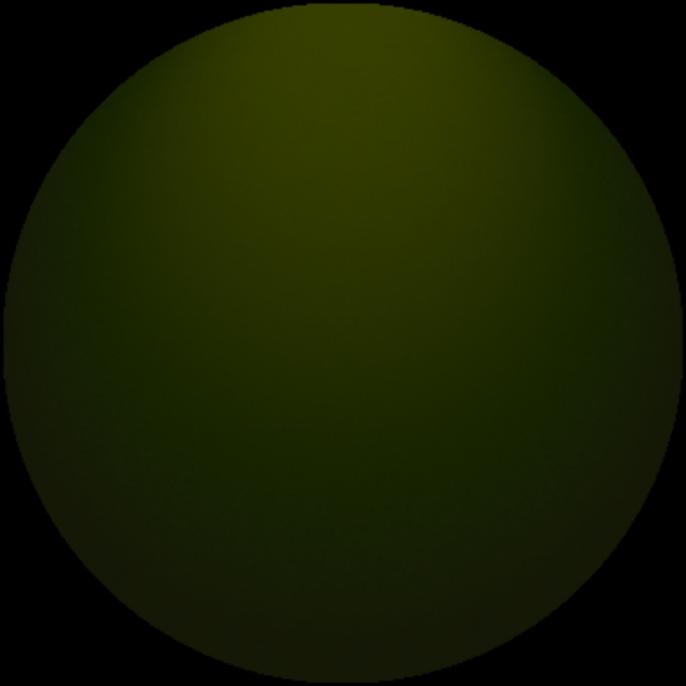
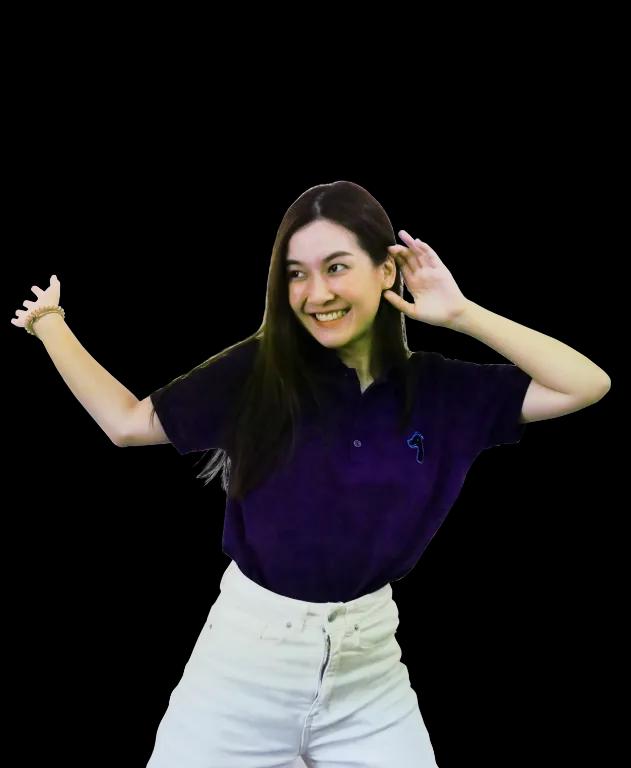
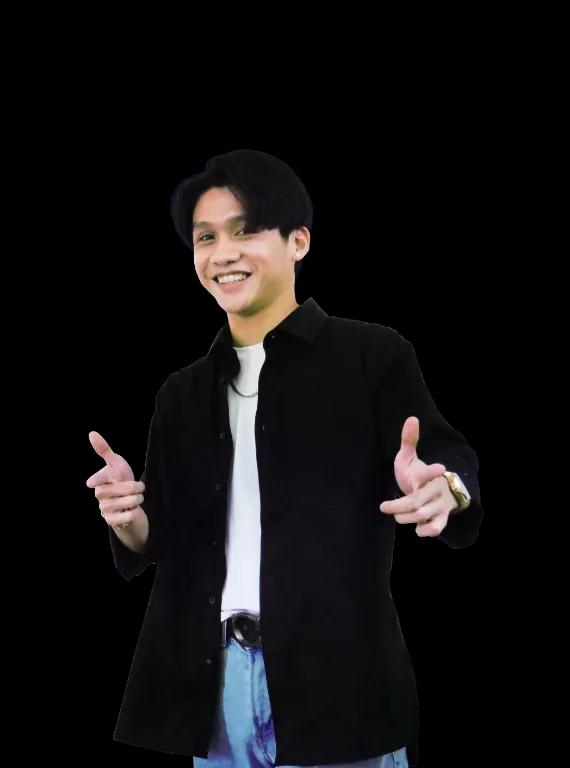
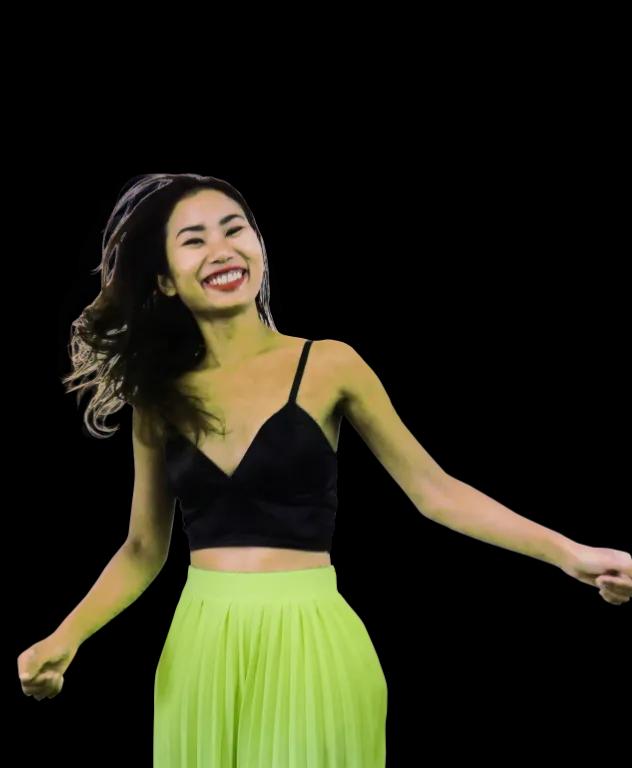
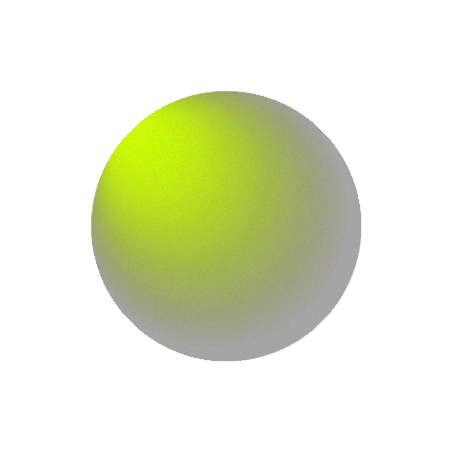
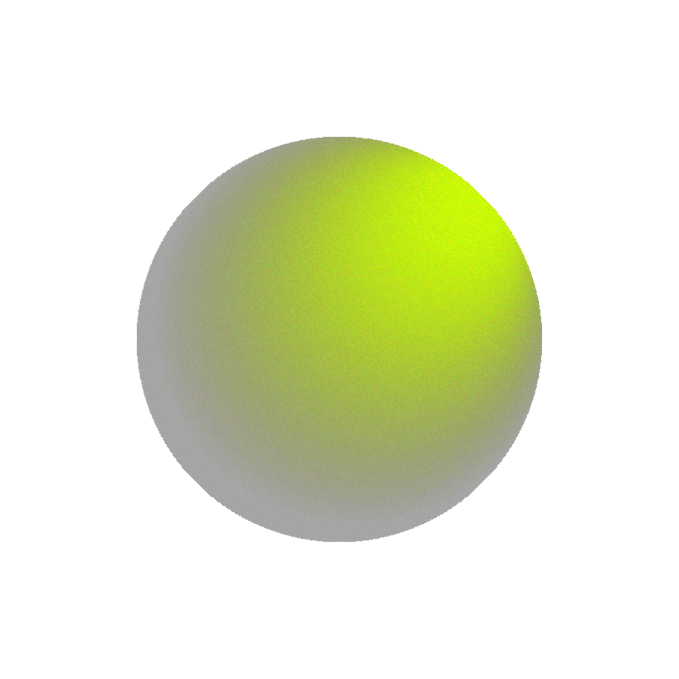
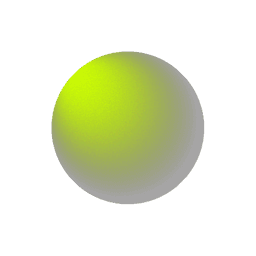
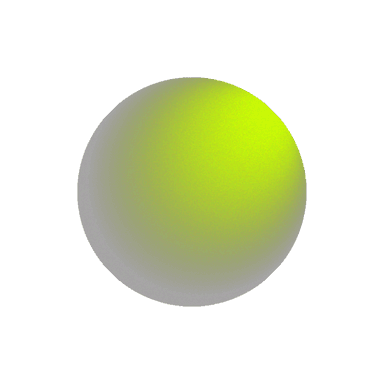
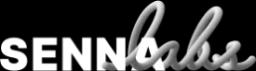