Revolutionizing the Manufacturing Industry: A Deep Dive into Modern Innovations
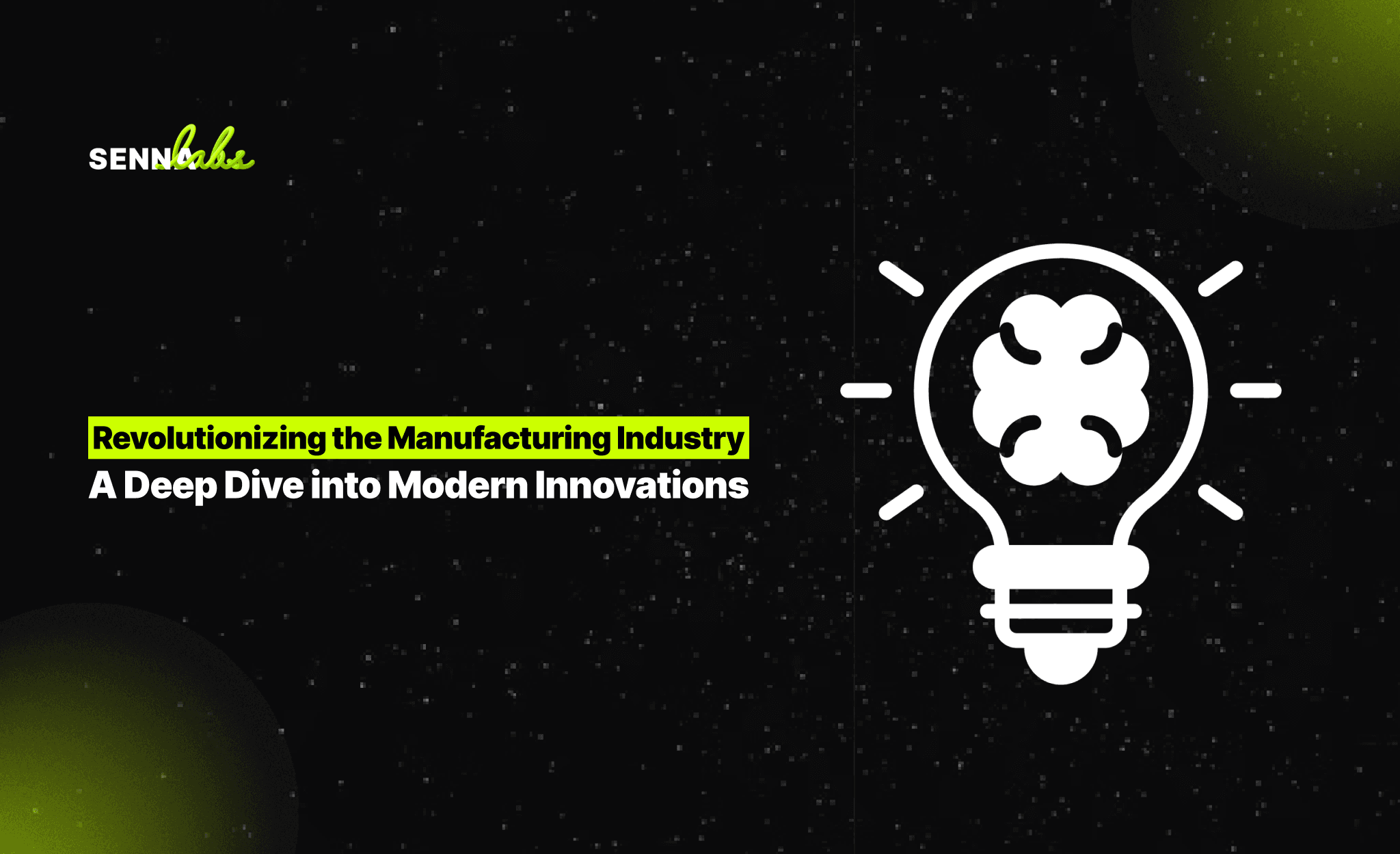
The age of the Industrial Revolution feels like a distant memory when you compare the clinking machines and steam-powered engines of yesteryears to today's computer-controlled machinery and automated processes. The manufacturing realm, once bound to manual labor and rudimentary machines, has been progressively marching into a new era. From the tactile to the digital, the analog to the automated, manufacturing today is an amalgam of advanced technologies and innovative strategies. As we stand at the threshold of what might be termed a second Industrial Revolution, we witness a sector that's not merely adapting but reinventing itself. It's a transformation driven by both necessity and ambition, a response to a dynamic global market that demands both speed and precision. But beyond the numbers and technology, it's a story of visionaries and engineers, of dreamers and doers. As we delve deeper into this realm, we will uncover the tapestry of innovations shaping modern manufacturing, woven with data, punctuated by case studies, and illuminated by expert insights.
Smart Manufacturing and Industry 4.0
One of the notable harbingers of change is the advent of Smart Manufacturing and Industry 4.0. This is more than just a buzzword; it's a holistic transformation where traditional manufacturing processes merge with digital technologies. The essence lies in real-time optimization of production through interconnected devices and making informed decisions via machine learning algorithms. The push towards such smart manufacturing is simple: in an increasingly competitive global landscape, there's a dire need for optimal efficiency, and this digital pivot promises precisely that. The path forward involves fostering collaboration between Information Technology (IT) and Operational Technology (OT), integrating sensors into machinery, and harnessing robust data analytics platforms.
Case Study: General Electric's Brilliant Factory:
In a bid to modernize manufacturing processes, GE integrated sensors and software into its factories. The result? A dramatic reduction in unplanned downtime, falling between 10-20%. This initiative stands as a beacon, illustrating the transformative power of smart manufacturing.
Additive Manufacturing (3D Printing)
Additive Manufacturing is evolving beyond prototyping, with its tentacles reaching deep into production realms. This innovative technique, building products layer by layer, allows for designs of unparalleled intricacy and significantly reduces waste. As the era of mass production gives way to mass customization, 3D printing is at the forefront, catering to unique consumer demands without compromising on efficiency.
Case Study Invisalign's Journey to Perfect Smiles:
Venturing beyond traditional braces, Invisalign exploited 3D printing to craft tailored orthodontic devices. Today, they have transformed over 35 million smiles worldwide, spotlighting the colossal potential of additive manufacturing in health and aesthetics.
Sustainable Manufacturing
In an age where climate change and environmental concerns dominate discussions, sustainable manufacturing emerges as the frontrunner. This approach, laser-focused on minimizing environmental footprints and championing workforce well-being, isn't just about eco-friendliness—it's also about economic prudence. Green practices can reduce costs, resonate with eco-conscious consumers, and prepare industries for impending stringent regulations.
Case Study: Adidas's Ocean-Saving Initiative:
Responding to the oceanic plastic crisis, Adidas collaborated with Parley for the Oceans, resulting in a pioneering footwear line made entirely from upcycled ocean plastic. This initiative, going beyond mere manufacturing to make a statement, showcases the intersection of innovation, sustainability, and social responsibility.
Augmented Reality (AR) in Training and Maintenance
Augmented Reality is breaking the confines of gaming and entertainment, making inroads into industrial landscapes. By overlaying digital data on the physical world, AR provides workers with invaluable insights, from complex task assistance to machinery maintenance cues. It's not just about tech immersion—it's about elevating workforce competence and efficiency.
Case Study: Boeing's Augmented Ascent:
By introducing AR glasses into their assembly processes, Boeing witnessed a staggering 25% reduction in wiring production time. But the real marvel? Error rates dropped to almost zero, underscoring AR's transformative impact on precision and productivity.
Supply Chain Digital Twins:
In a hyper-connected global economy, real-time insights into supply chains are not just beneficial—they're indispensable. Digital twins, offering virtual replicas of physical supply systems, promise such real-time monitoring, analysis, and optimization, ensuring operations remain smooth, efficient, and adaptive.
Case Study: Unilever's Digital Leap:
Unilever, embracing digital twin technology, revolutionized its supply chain mechanisms. The rewards were tangible: a 30% dip in stockouts and a 10% inventory reduction, echoing the immense potential of digital twins in fine-tuning global operations.
Manufacturing has always been the backbone of economies worldwide. From the first potter's wheel to today's robotic assembly lines, it's an industry that has continuously shaped and reshaped our daily lives. But the current innovations, from digitizing production floors to leveraging the vast realms of virtual data, are nothing short of revolutionary. These aren't just tweaks or upgrades; they're paradigm shifts in how we conceive, produce, and distribute. As industries embrace these changes, they're laying the foundation for a future that's sustainable, efficient, and in tune with both human and environmental needs. And while challenges persist, as they always do, the compass is clear: forward. By harmonizing the lessons of the past with the possibilities of the future, the manufacturing industry is not just responding to change—it's leading it. With every integrated sensor, every AR module, and every digital twin, it promises a horizon where technology augments human potential, ensuring that the best days of manufacturing still lie ahead.
Reference:
Deloitte Insights
General Electric
Statista
Invisalign's Process
Nature
Adidas x Parley
PwC on AR
Boeing's AR Usage
Gartner on Digital Twins
Unilever's Implementation
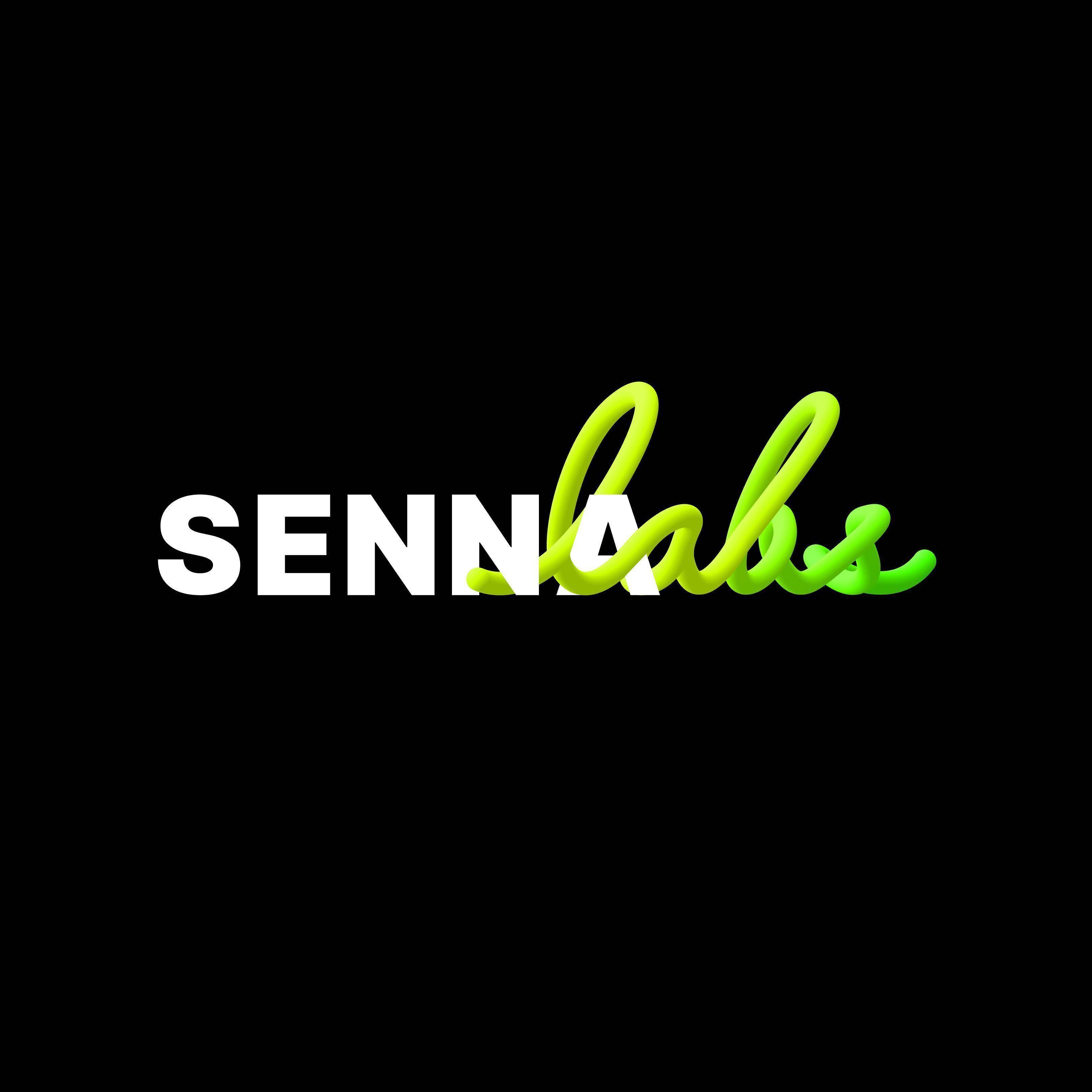
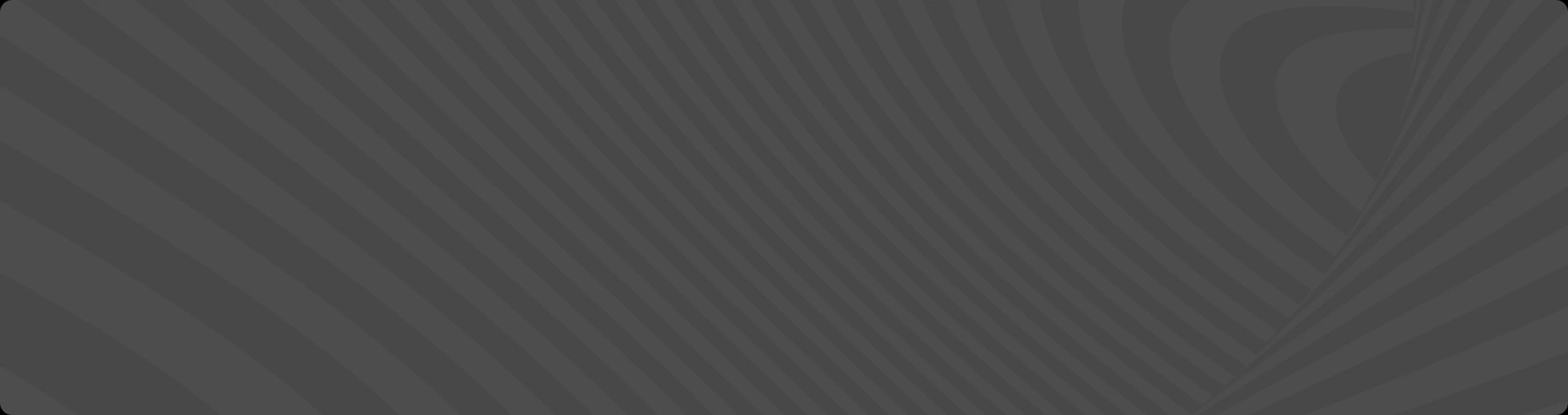
Subscribe to follow product news, latest in technology, solutions, and updates
Other articles for you
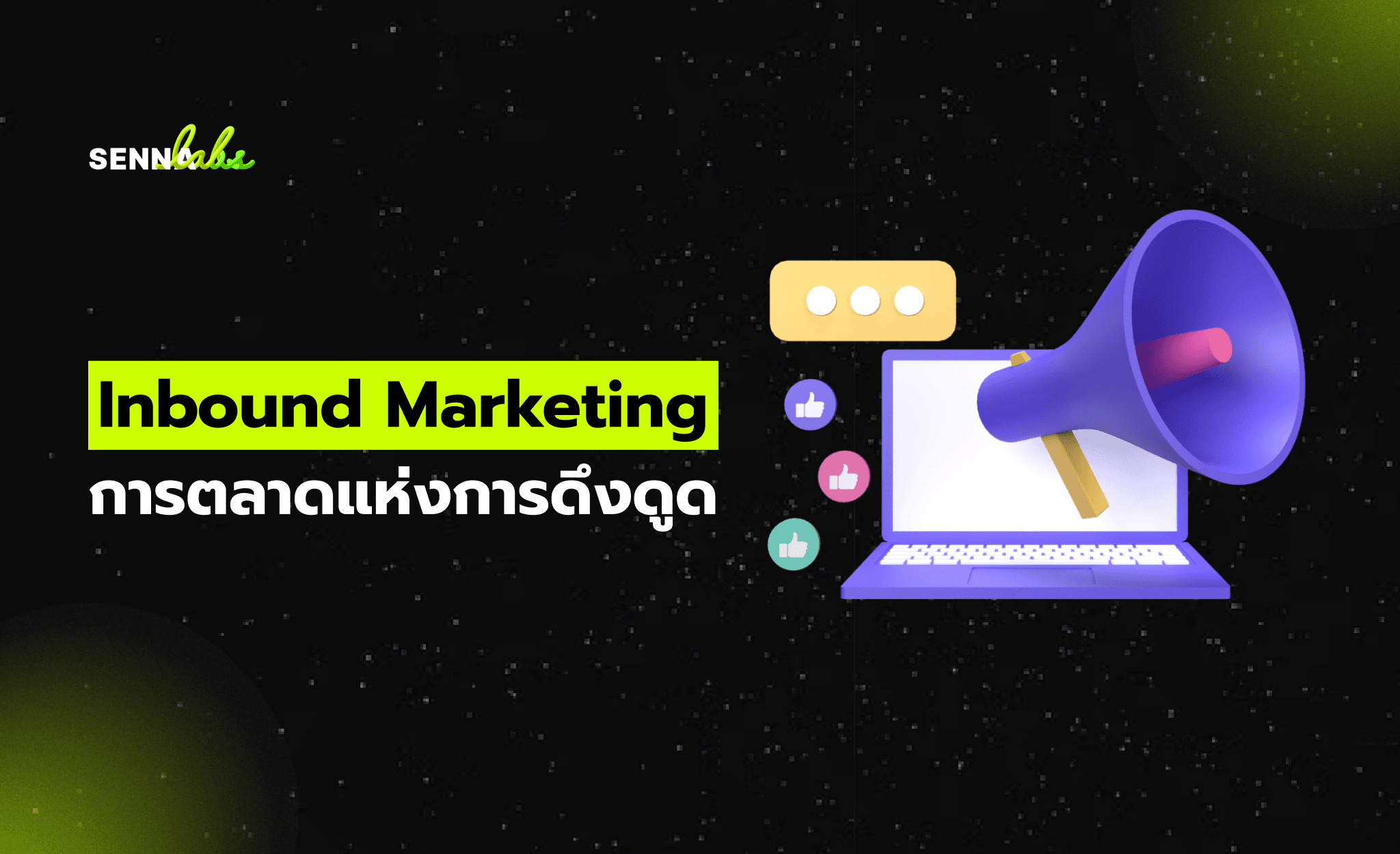
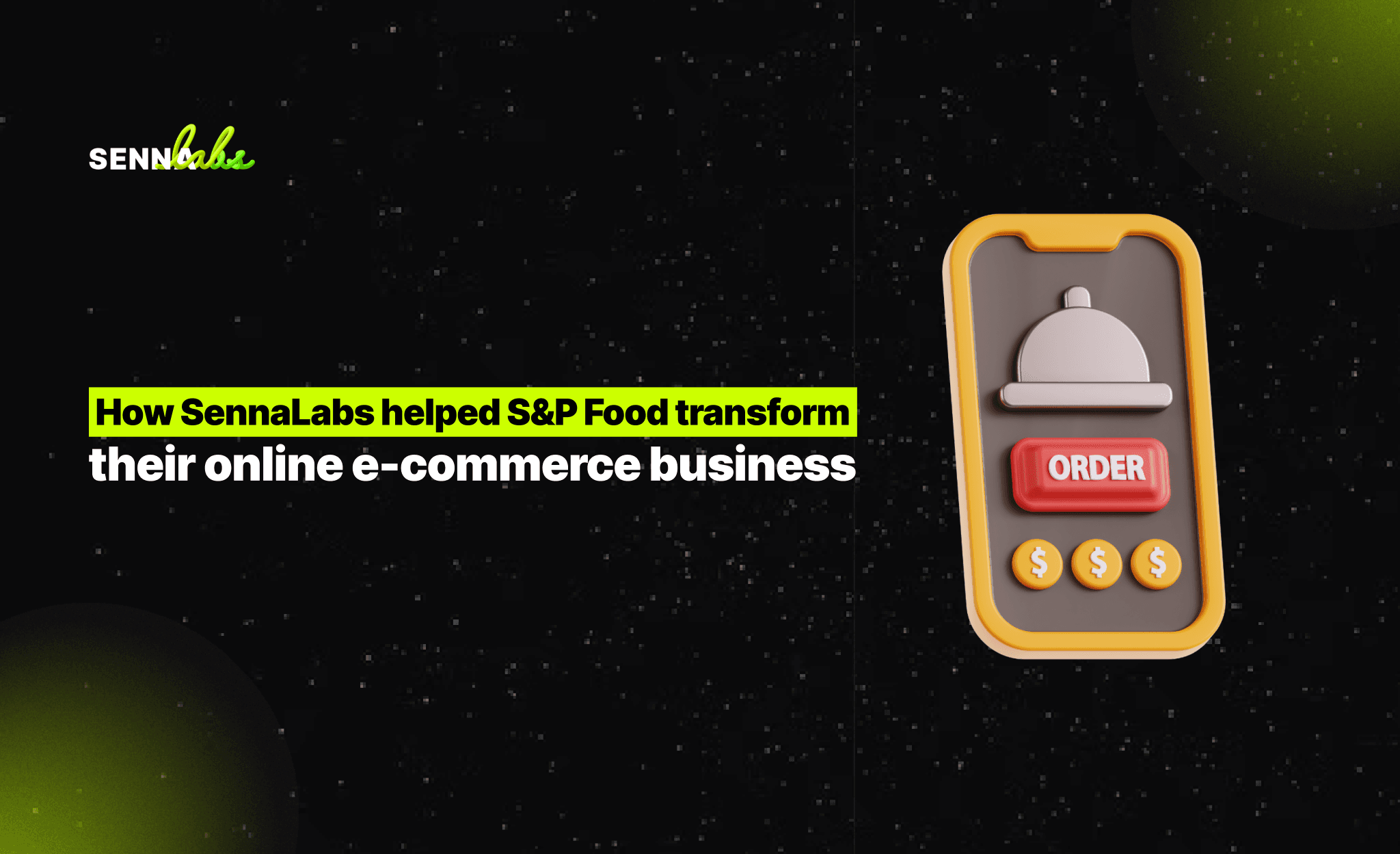
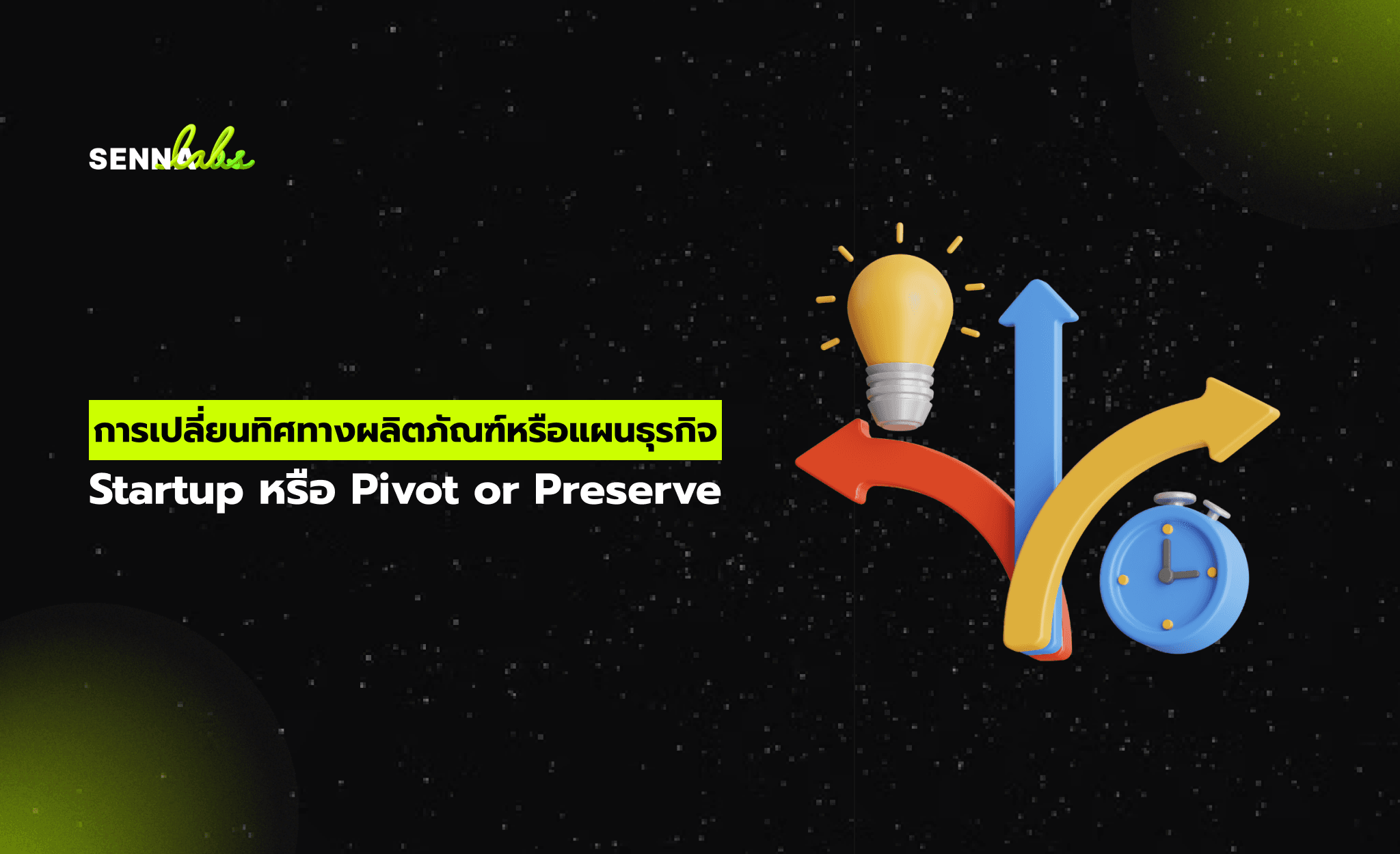
Let’s build digital products that are simply awesome !
We will get back to you within 24 hours!Go to contact us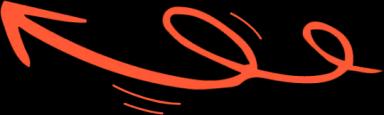
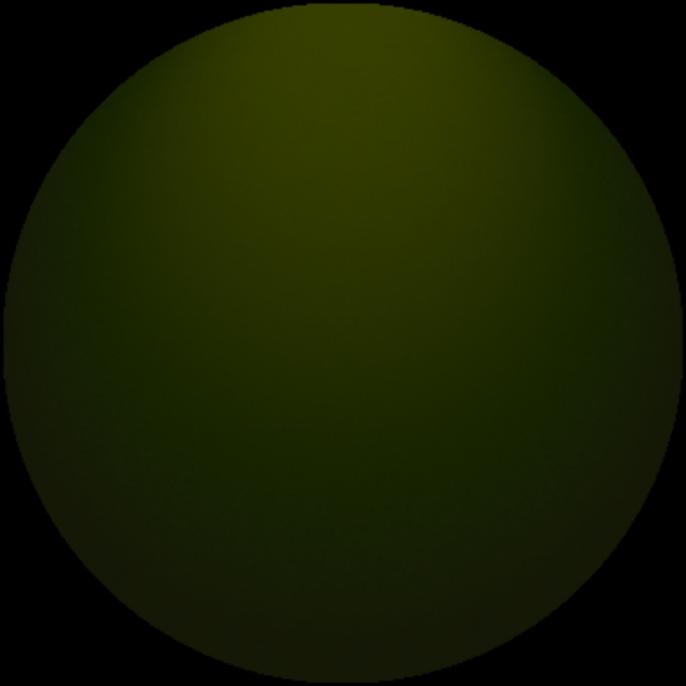
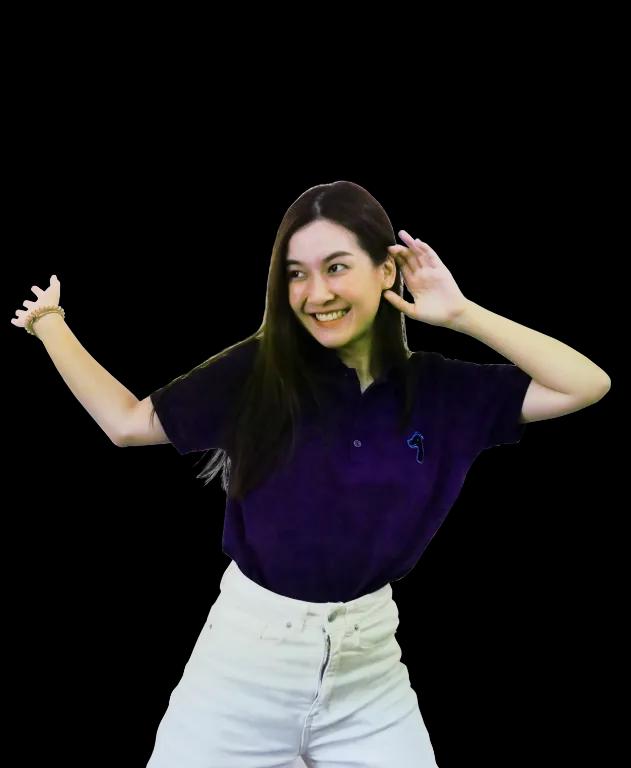
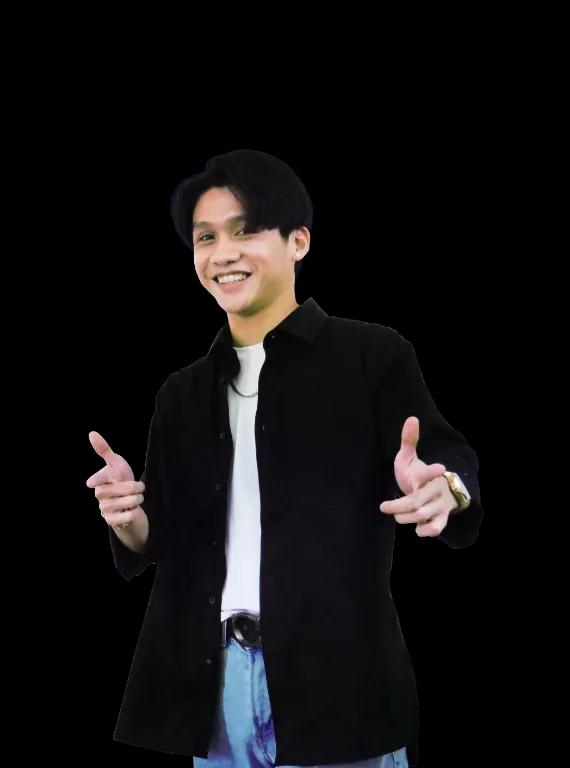
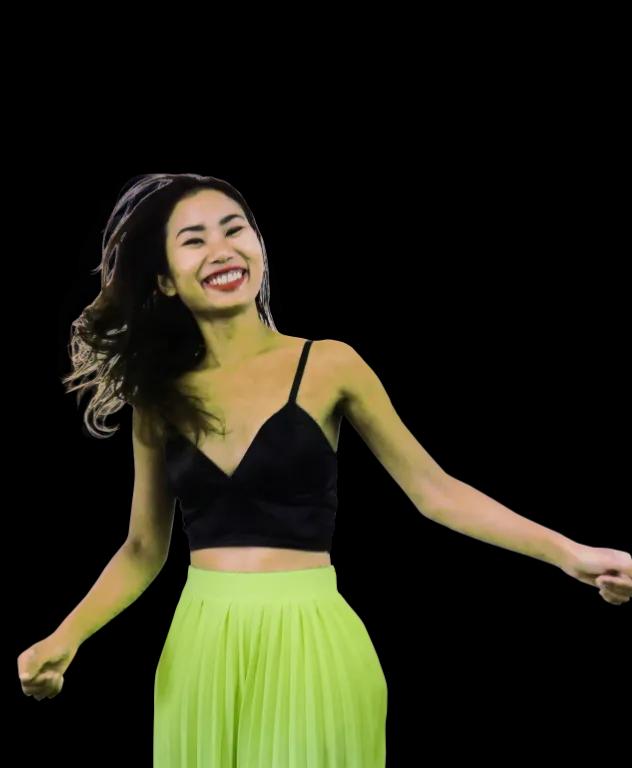
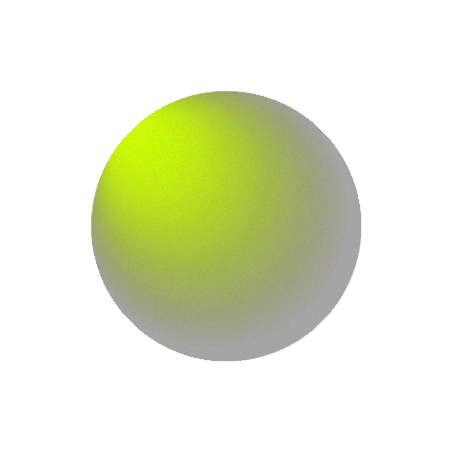
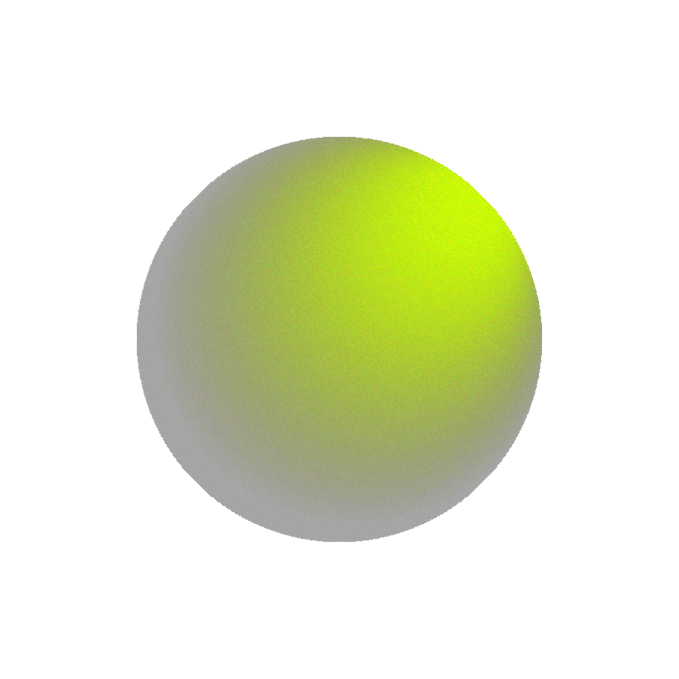
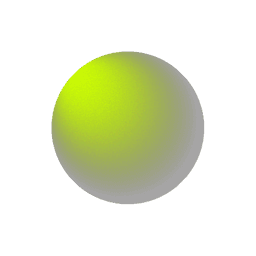
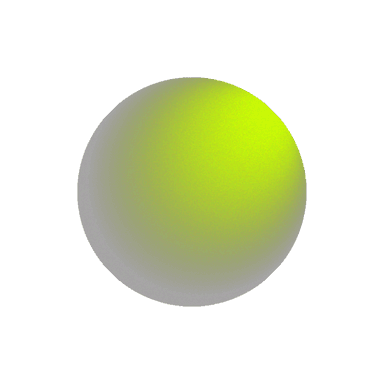
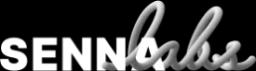