Ensuring Compliance with Industry Regulations Using WMS

Compliance with industry regulations is a critical aspect of warehouse operations, particularly in industries such as healthcare, food and beverage, and pharmaceuticals. Regulations often mandate strict controls over safety, labeling, and traceability to protect consumers and ensure operational integrity. However, manual methods of managing compliance can be time-consuming, error-prone, and costly.
Warehouse Management Systems (WMS) offer a streamlined solution for ensuring regulatory compliance. By automating processes, improving traceability, and providing real-time visibility, WMS tools help businesses adhere to regulations while maintaining efficiency. This article explores how WMS solutions support compliance and highlights the success of a medical supplies distributor that used WMS to meet stringent regulatory requirements.
The Challenges of Regulatory Compliance in Warehousing
Industries that deal with sensitive or regulated products face significant compliance challenges, including:
-
Traceability Requirements: Maintaining detailed records of product origins, movements, and destinations is essential for recalls and audits.
-
Safety Standards: Warehouses must ensure proper storage conditions, such as temperature and humidity, to preserve product integrity.
-
Labeling Regulations: Products must be labeled accurately with essential details, such as batch numbers, expiration dates, and regulatory certifications.
-
Audits and Inspections: Regulatory bodies require businesses to provide accurate, up-to-date documentation during inspections.
-
Risk of Penalties: Non-compliance can result in financial penalties, product recalls, or damage to reputation.
How WMS Ensures Compliance with Regulations
1. Traceability and Recordkeeping
WMS solutions enable end-to-end traceability by recording every movement of a product, from receipt to storage to shipment.
-
How It Works:
-
Products are tagged with unique identifiers, such as barcodes or RFID tags.
-
The WMS logs all transactions, creating a digital trail that can be accessed for audits or recalls.
-
Benefits:
-
Simplifies compliance with traceability regulations.
-
Provides detailed records for regulatory audits.
2. Labeling and Documentation
Accurate labeling is critical for compliance in industries like healthcare and food. WMS automates labeling processes, ensuring that products meet regulatory requirements.
-
How It Works:
-
The WMS generates and prints labels with all required information, including batch numbers, expiration dates, and certifications.
-
Integrated quality checks ensure labels are accurate before shipment.
-
Benefits:
-
Reduces labeling errors.
-
Ensures compliance with industry-specific labeling standards.
3. Environmental Monitoring
WMS systems integrated with IoT sensors monitor storage conditions to ensure compliance with safety regulations for temperature-sensitive products.
-
How It Works:
-
Sensors track temperature, humidity, and other environmental factors in real time.
-
The WMS triggers alerts if conditions deviate from acceptable ranges.
-
Benefits:
-
Protects product integrity and safety.
-
Ensures compliance with storage requirements for regulated items.
4. Automated Reporting for Audits
WMS simplifies reporting by providing automated, real-time access to compliance-related data, reducing the time and effort needed for audits and inspections.
-
How It Works:
-
Reports can be generated instantly, showing inventory status, product movements, and environmental conditions.
-
Historical data is stored securely and can be retrieved when needed.
-
Benefits:
-
Eases the audit process by ensuring all documentation is readily available.
-
Minimizes the risk of non-compliance penalties.
5. Recalls and Incident Management
In the event of a recall, WMS solutions enable businesses to quickly identify affected products and take corrective action.
-
How It Works:
-
The WMS tracks every product by lot or batch number, identifying where it was stored, sold, or shipped.
-
Automated workflows streamline the recall process, ensuring affected products are isolated and removed promptly.
-
Benefits:
-
Reduces response time during recalls.
-
Demonstrates regulatory compliance during investigations.
Real-World Use Case: A Medical Supplies Distributor’s Compliance Success
A medical supplies distributor faced significant challenges in complying with strict tracking and traceability regulations for products like surgical instruments and pharmaceuticals. Manual tracking methods led to frequent errors and delays during audits, exposing the company to potential regulatory penalties.
The Solution:
The distributor implemented a WMS designed for regulated industries. Key features included:
-
End-to-End Traceability: The WMS tracked products from receipt to shipment, recording every movement with detailed timestamps.
-
Automated Labeling: Labels were generated automatically to meet regulatory requirements, reducing human error.
-
Environmental Monitoring: IoT sensors integrated with the WMS ensured proper storage conditions for temperature-sensitive items.
The Results:
-
Improved Traceability: The company maintained complete visibility of product movements, simplifying compliance with traceability regulations.
-
Streamlined Audits: Automated reporting reduced audit preparation time, enabling quicker responses to regulatory inquiries.
-
Enhanced Customer Trust: Demonstrating compliance with regulations improved the distributor’s reputation among clients and regulatory bodies.
Industries That Benefit from WMS for Compliance
-
Healthcare and Pharmaceuticals: Ensures traceability of medicines and medical devices while maintaining proper storage conditions.
-
Food and Beverage: Tracks batches and expiration dates to comply with food safety standards.
-
Consumer Electronics: Manages hazardous materials and ensures compliance with environmental regulations.
-
Aerospace and Defense: Tracks high-value, regulated components to meet stringent safety and quality standards.
Key Features to Look for in a WMS for Compliance
-
Traceability Tools: Ensure the WMS can track products by batch, lot, or serial number with detailed records.
-
Labeling Integration: Look for systems that automate the generation of compliant labels.
-
Environmental Monitoring: Choose a solution that integrates with IoT sensors for real-time tracking of storage conditions.
-
Automated Reporting: Ensure the WMS provides customizable reports for audits and inspections.
-
Recall Management: Select a system with workflows for efficient recall processes.
Conclusion: A Smarter Approach to Regulatory Compliance
Regulatory compliance is a non-negotiable aspect of operations for businesses in industries dealing with sensitive or regulated products. A robust WMS simplifies the process, ensuring traceability, proper labeling, and adherence to storage requirements.
The success of the medical supplies distributor demonstrates the power of WMS in reducing compliance risks while enhancing operational efficiency. By investing in the right system, businesses can meet regulatory demands confidently and efficiently, fostering trust among stakeholders and ensuring long-term growth.
Ready to improve your compliance processes? Explore WMS solutions tailored to your industry and take control of your regulatory obligations today.
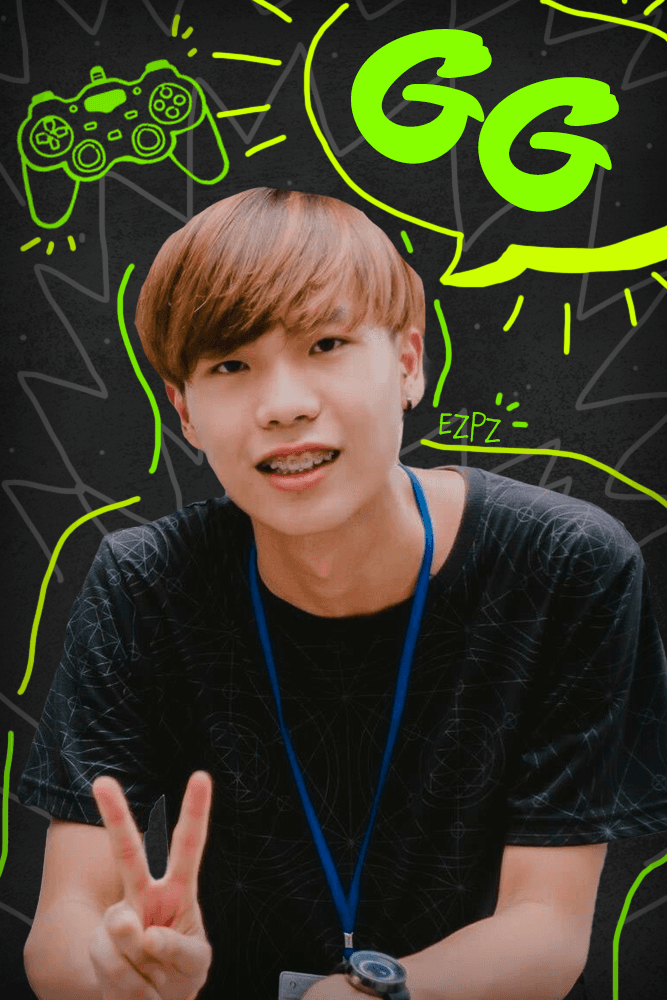
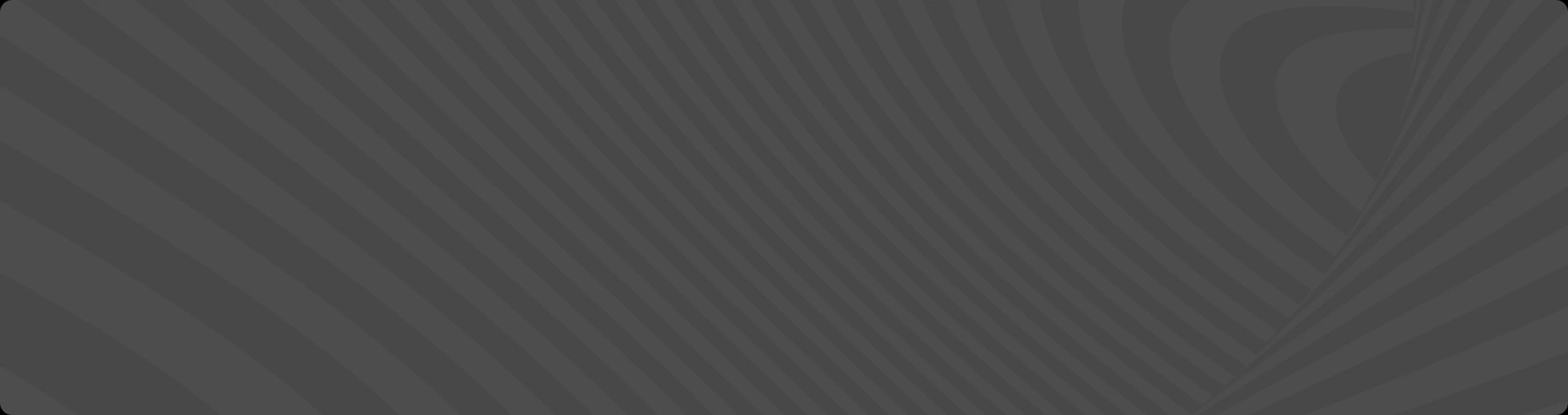
Subscribe to follow product news, latest in technology, solutions, and updates
Other articles for you
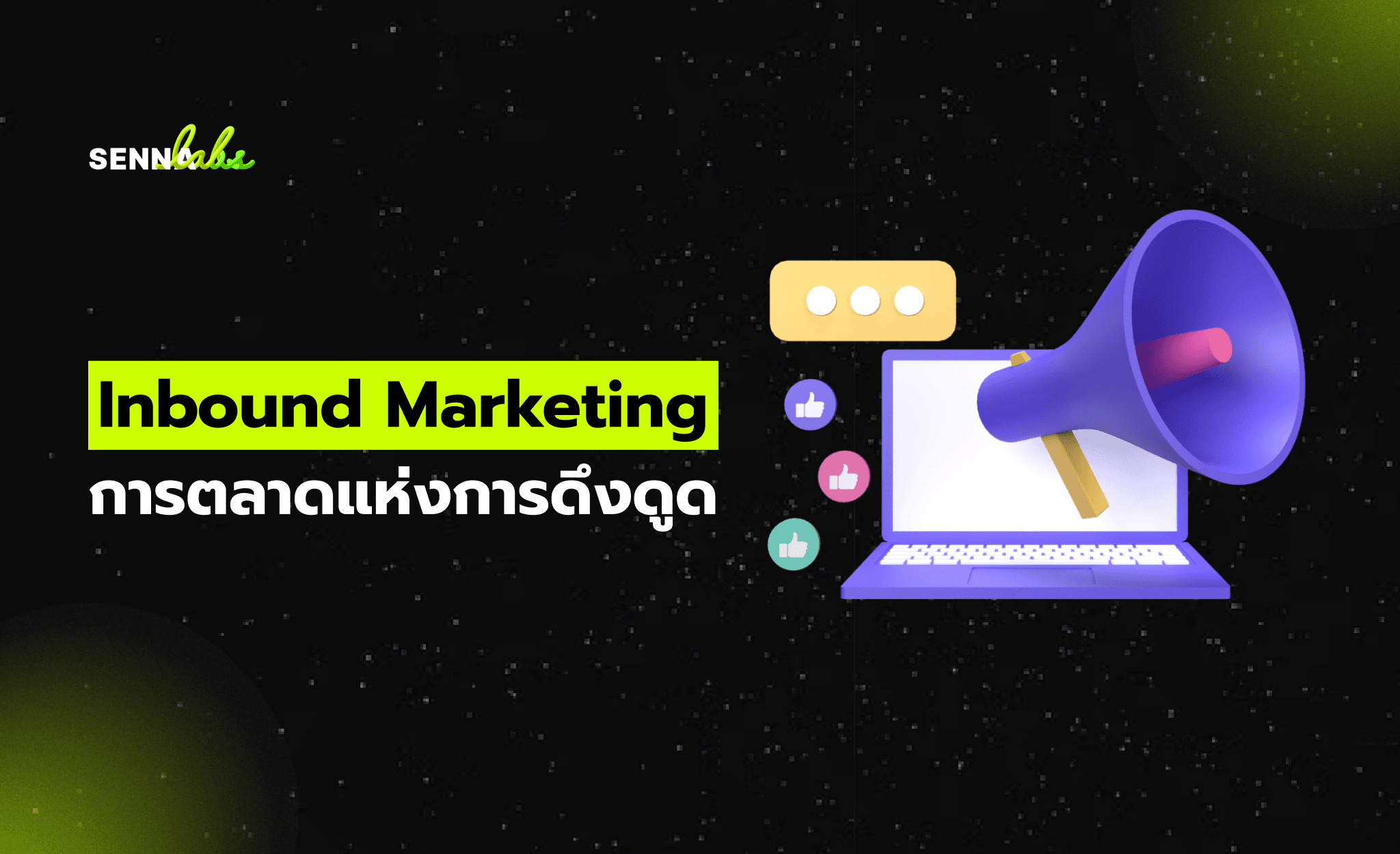
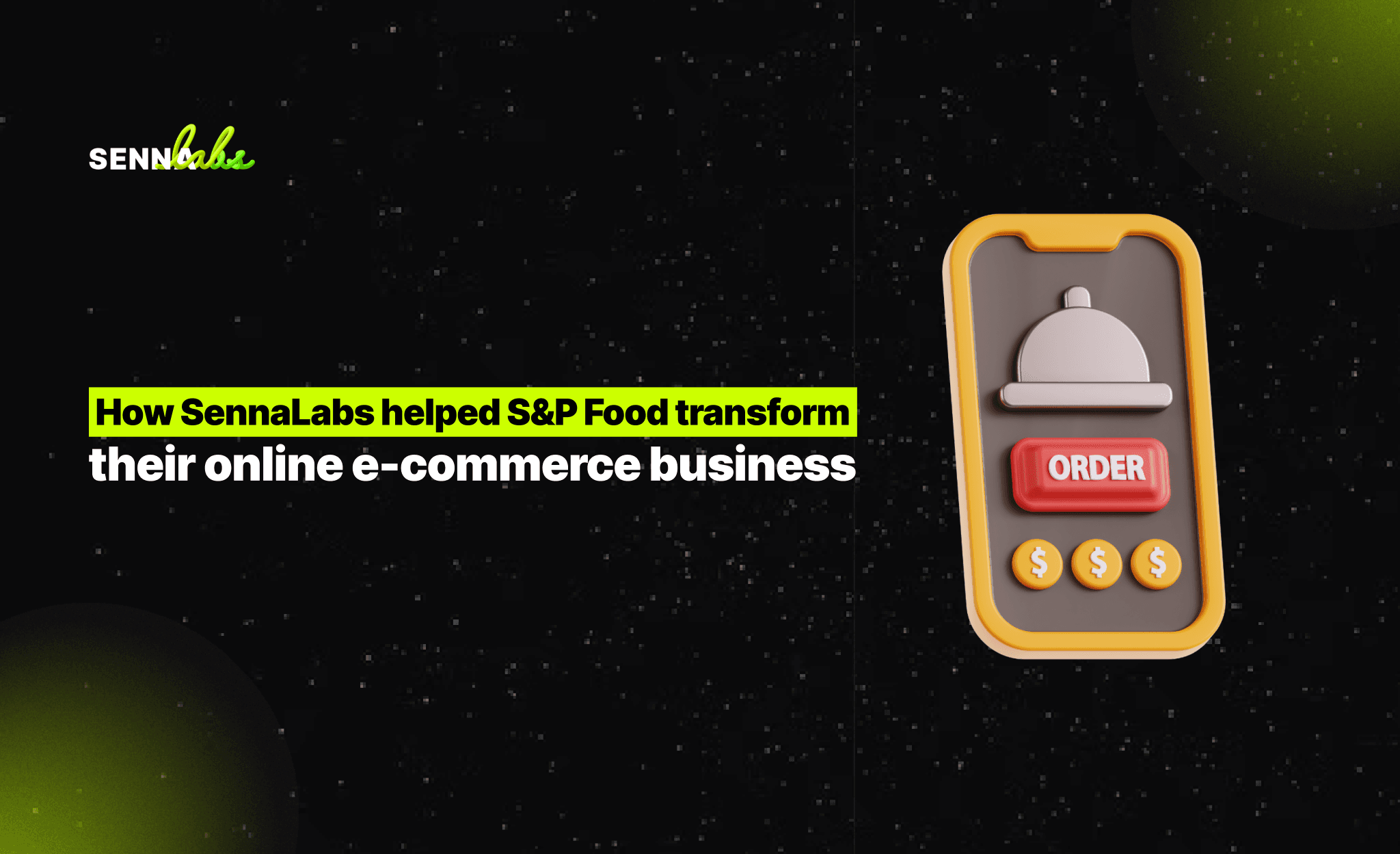
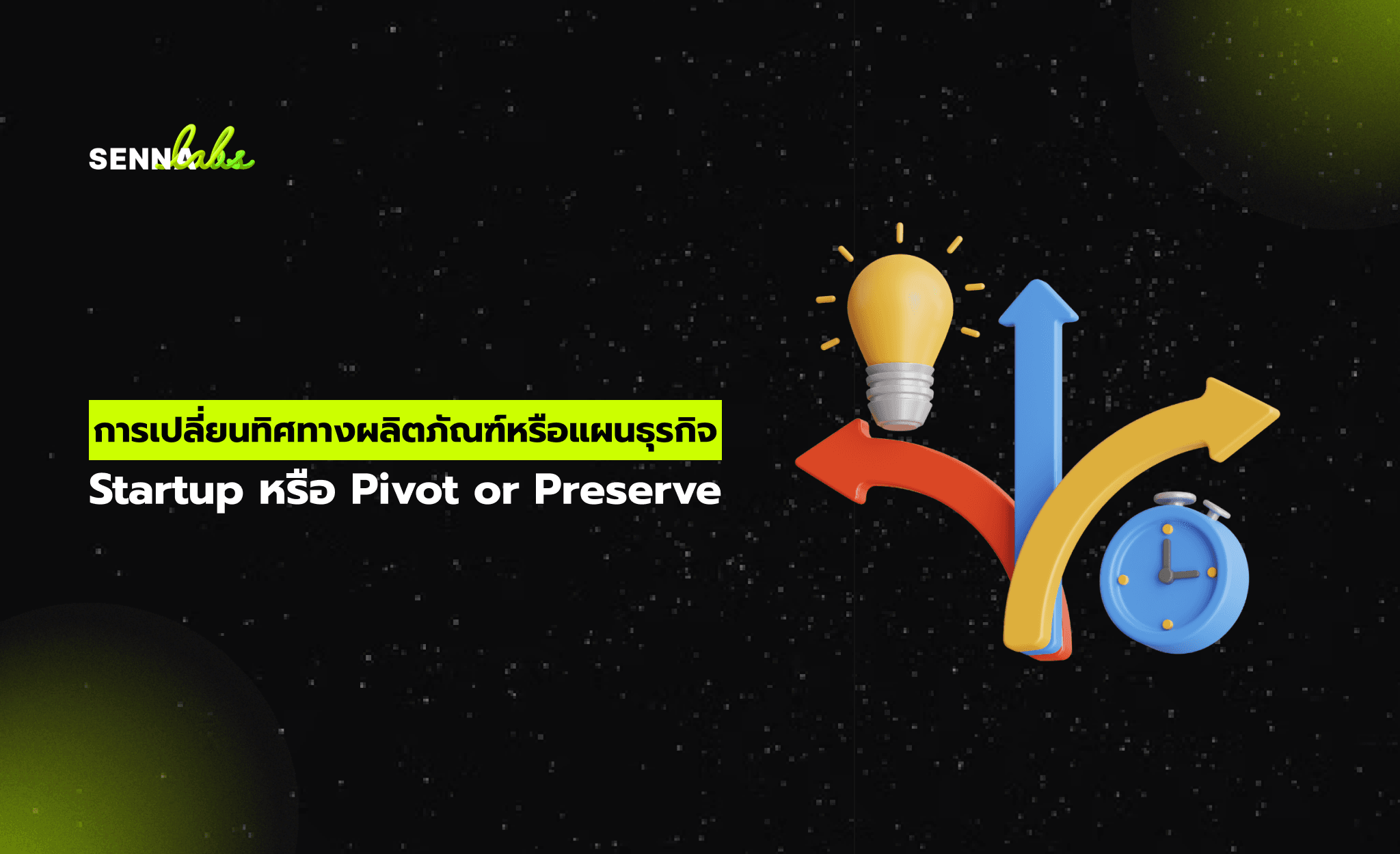
Let’s build digital products that are simply awesome !
We will get back to you within 24 hours!Go to contact us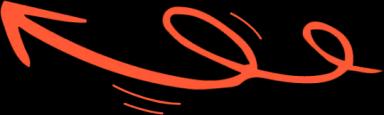
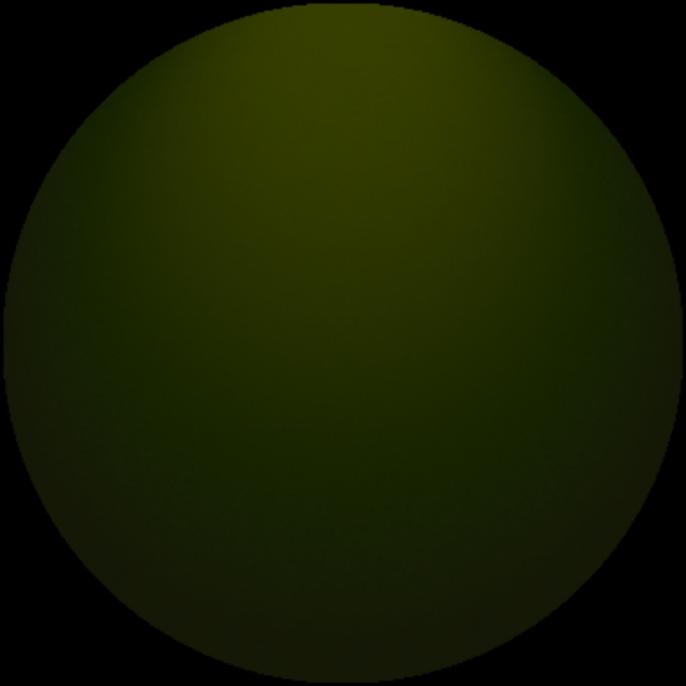
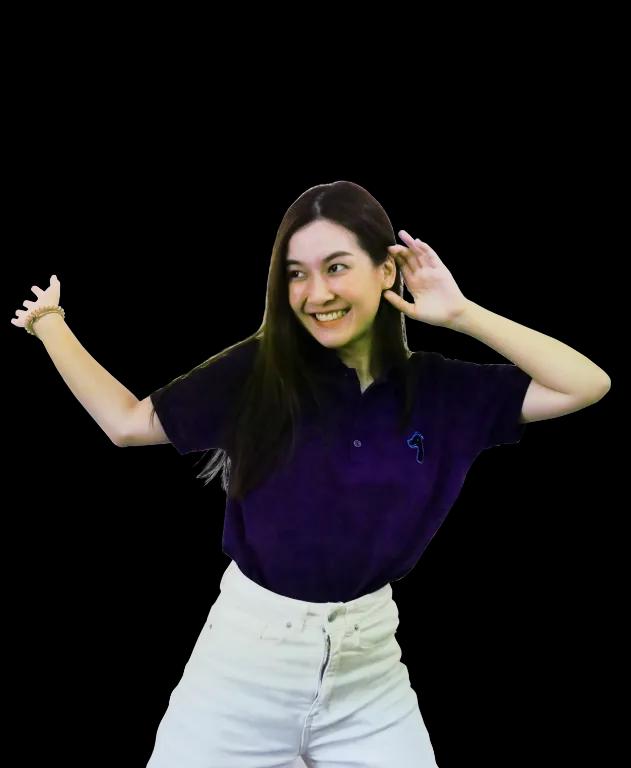
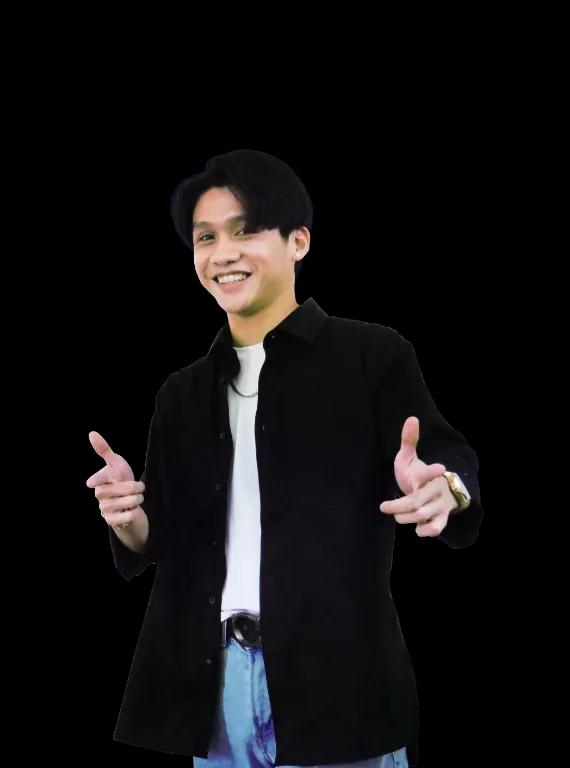
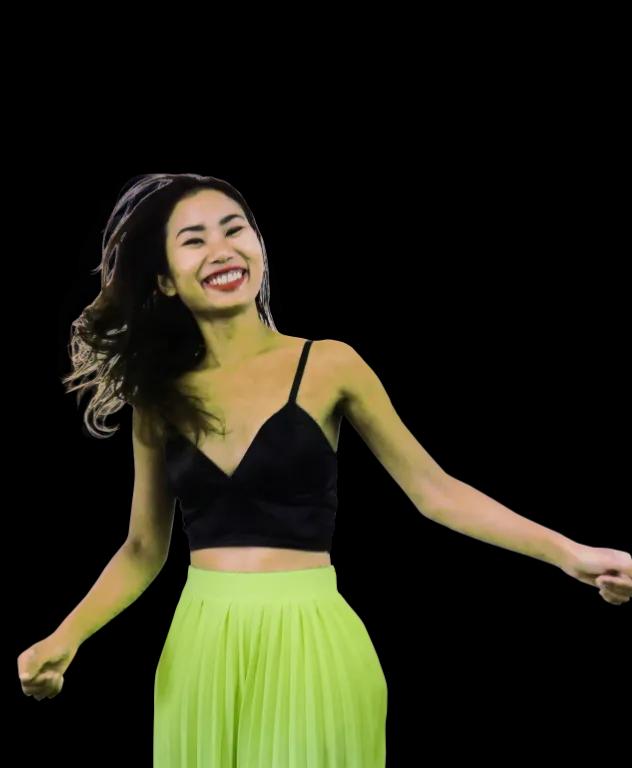
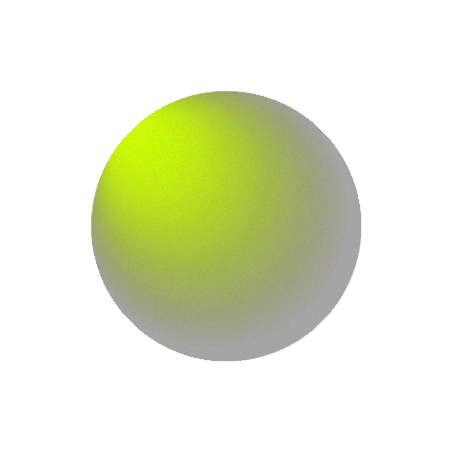
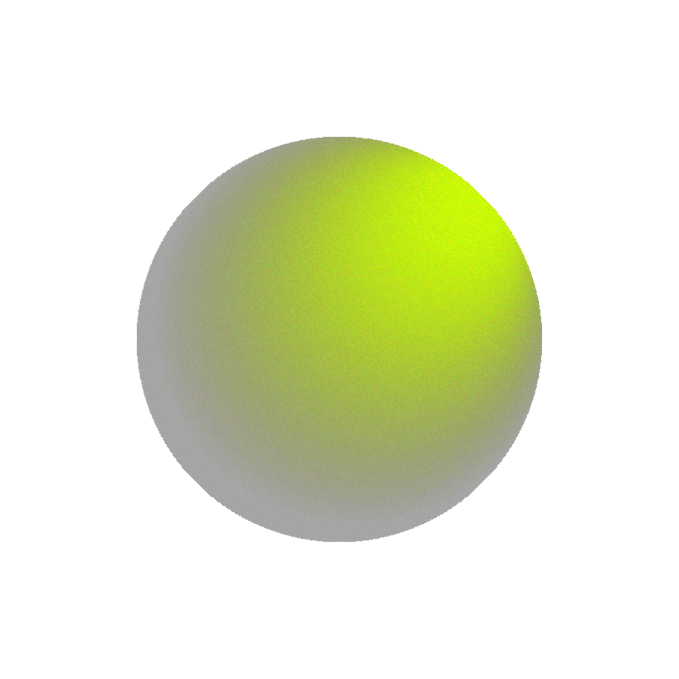
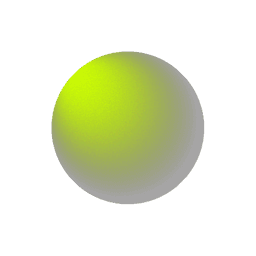
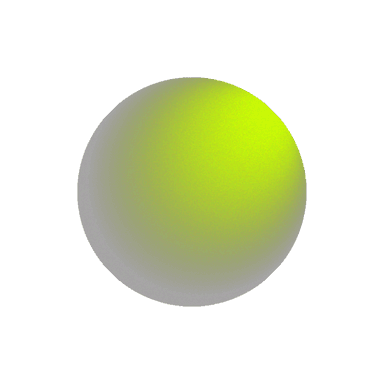
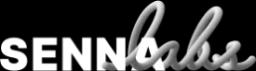