Digital Maturity in the Manufacturing Sector: Driving Efficiency and Innovation
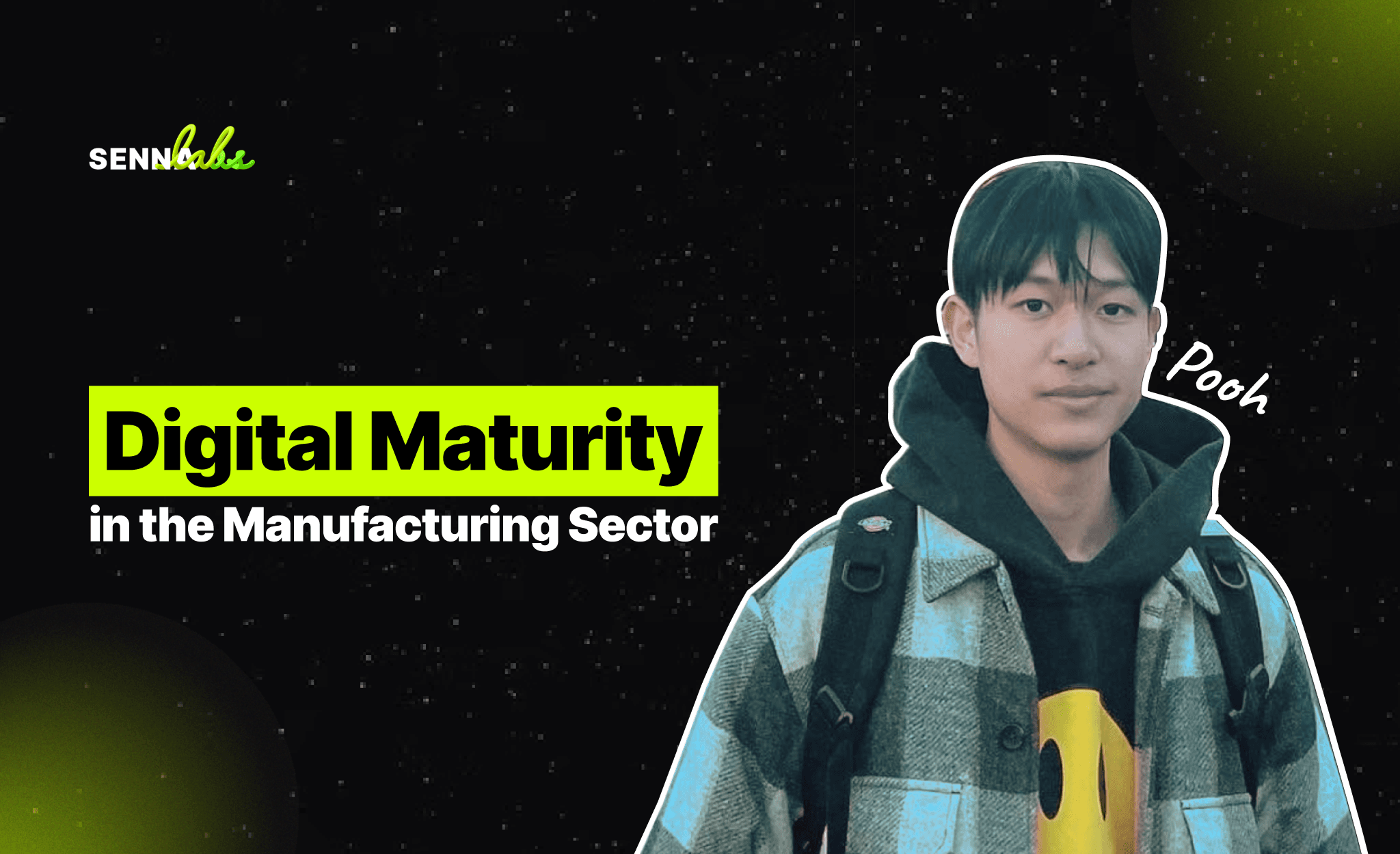
The manufacturing industry is in the midst of a technological revolution. With the advent of advanced technologies such as the Internet of Things (IoT), Artificial Intelligence (AI), and automation, factories are increasingly able to optimize processes, improve efficiency, and reduce costs. However, adopting these technologies effectively requires a comprehensive understanding of an organization's current digital capabilities—a challenge that many manufacturers face. To overcome this, a Digital Maturity Assessment (DMA) plays a crucial role.
A Digital Maturity Assessment helps manufacturers evaluate their readiness for digital transformation by identifying gaps in technology infrastructure, data management, and operational efficiency. By leveraging the insights from a DMA, manufacturers can develop a clear roadmap for implementing digital technologies like IoT, AI, and automation to drive efficiency and innovation across production lines and supply chains.
In this article, we’ll explore how DMA can help the manufacturing sector embrace digital transformation, leading to smarter production lines, predictive maintenance, and better supply chain management. Additionally, we’ll look at a real-world use case where a manufacturing plant significantly reduced machine downtime and improved equipment efficiency through IoT and AI-based systems.
Understanding Digital Maturity in the Manufacturing Sector
Digital maturity refers to an organization's ability to leverage digital technologies effectively across its operations. In the context of manufacturing, this includes the use of advanced tools such as IoT sensors, AI-driven analytics, cloud computing, and automation technologies to streamline processes, monitor equipment performance, and optimize the supply chain.
Achieving digital maturity in the manufacturing sector is not only about adopting the latest technologies; it’s also about fostering a culture of continuous improvement, data-driven decision-making, and seamless integration between different parts of the production process. Manufacturers with higher levels of digital maturity are better equipped to:
-
Reduce operational inefficiencies
-
Increase flexibility and responsiveness to market changes
-
Optimize asset utilization
-
Enhance product quality
-
Enable predictive maintenance
However, many manufacturers still rely on outdated systems, manual processes, and siloed data, which limit their ability to reap the benefits of digital transformation. This is where a Digital Maturity Assessment comes into play.
The Role of a Digital Maturity Assessment (DMA)
A Digital Maturity Assessment is a comprehensive evaluation of an organization's current digital capabilities. It provides manufacturers with insights into how effectively they are using digital tools, technologies, and data to achieve business objectives. A DMA identifies areas where improvements are needed and offers recommendations for optimizing processes, technology adoption, and organizational readiness.
The assessment typically focuses on several key areas:
-
Technology Infrastructure: Evaluating the current state of digital technologies, including the integration of IoT, AI, and cloud computing systems.
-
Data Utilization: Assessing how well data is collected, analyzed, and used to inform decision-making across production, quality control, and supply chain management.
-
Operational Efficiency: Measuring the level of automation, process optimization, and real-time monitoring capabilities in the production environment.
-
Employee Skills and Culture: Gauging the organization’s readiness to adopt new digital technologies, including employee skills and training programs.
-
Supply Chain Integration: Reviewing how well digital tools are being used to manage inventory, logistics, and supplier relationships.
By conducting a DMA, manufacturers gain a clear understanding of their digital strengths and weaknesses, allowing them to prioritize investments in technologies that will deliver the greatest impact on efficiency, productivity, and innovation.
Leveraging IoT, AI, and Automation for Smarter Manufacturing
As manufacturers aim to increase efficiency and reduce costs, IoT, AI, and automation are becoming integral to their digital transformation strategies. These technologies offer numerous benefits, from real-time monitoring of equipment to predictive maintenance and smarter decision-making across production lines and supply chains.
1. IoT Sensors: Real-Time Data for Optimized Operations
IoT sensors are one of the most transformative technologies in manufacturing. These devices collect real-time data from machines, equipment, and production lines, providing manufacturers with insights into machine performance, production efficiency, and equipment health.
IoT-enabled manufacturing allows for continuous monitoring of production processes, enabling real-time adjustments to optimize output and reduce waste. Additionally, IoT data can be used to automate quality control processes, ensuring that products meet specifications and reducing the need for manual inspections.
Benefits of IoT in Manufacturing:
-
Real-time performance tracking: Manufacturers can track machine performance, energy usage, and other key metrics in real time.
-
Improved product quality: Continuous monitoring helps detect defects early in the production process, minimizing rework and waste.
-
Predictive maintenance: IoT data can be used to predict equipment failures before they happen, reducing downtime and maintenance costs.
2. AI and Predictive Maintenance: Minimizing Downtime and Costs
Predictive maintenance is another key area where digital maturity can have a transformative impact on manufacturing. Traditionally, maintenance has been performed on a reactive or scheduled basis. However, this approach can lead to unplanned downtime and unnecessary costs if machines fail between scheduled maintenance intervals.
By integrating AI-based predictive maintenance systems with IoT sensors, manufacturers can monitor the condition of equipment in real time and predict when maintenance is required. AI algorithms analyze data from IoT sensors to identify patterns that indicate potential failures, allowing maintenance teams to take action before a breakdown occurs.
Benefits of Predictive Maintenance:
-
Reduced machine downtime: Predictive maintenance minimizes unplanned downtime by addressing potential issues before they lead to equipment failure.
-
Lower maintenance costs: By performing maintenance only when necessary, manufacturers can reduce labor and spare part costs associated with routine maintenance schedules.
-
Extended equipment lifespan: Monitoring machine health in real time helps identify inefficiencies or wear and tear early, leading to longer equipment life.
3. Automation: Streamlining Production Lines
Automation has long been a staple of modern manufacturing, but with advances in digital technologies, manufacturers can now automate more complex tasks and processes. Robotic process automation (RPA), machine learning, and AI-driven systems are enabling manufacturers to automate not only repetitive tasks but also decision-making processes in production and supply chain management.
Automation helps reduce the reliance on manual labor, increases production speeds, and enhances accuracy across the manufacturing process. It also frees up employees to focus on higher-value tasks such as process optimization and innovation.
Benefits of Automation:
-
Increased production efficiency: Automated processes reduce human error and ensure consistent quality.
-
Scalability: Automation allows manufacturers to quickly scale operations up or down in response to changing demand.
-
Cost savings: By reducing labor costs and minimizing errors, automation leads to significant cost savings over time.
Supply Chain Optimization Through Digital Maturity
Beyond the production line, digital maturity also plays a crucial role in optimizing the supply chain. As manufacturers adopt digital tools and technologies, they can gain greater visibility into their supply chain, enabling better inventory management, demand forecasting, and supplier collaboration.
Digital supply chain management involves using IoT sensors, cloud-based platforms, and AI-driven analytics to monitor the movement of goods, predict demand fluctuations, and optimize inventory levels in real time. By leveraging these technologies, manufacturers can reduce lead times, improve order fulfillment, and minimize inventory holding costs.
Benefits of Supply Chain Optimization:
-
Improved demand forecasting: AI-driven analytics help predict market demand more accurately, allowing manufacturers to adjust production levels accordingly.
-
Enhanced supplier collaboration: Cloud-based platforms enable real-time communication and collaboration with suppliers, improving response times and reducing delays.
-
Reduced inventory costs: Smarter inventory management ensures that manufacturers have the right amount of stock at the right time, minimizing excess inventory and stockouts.
Real-World Use Case: Achieving Digital Maturity with IoT and AI
To illustrate the impact of digital maturity in the manufacturing sector, let’s look at a real-world example of how a manufacturing plant used a Digital Maturity Assessment to optimize its operations.
The Challenge:
A manufacturing plant was facing high levels of machine downtime and inefficient equipment performance, which led to delays in production and increased operational costs. The plant relied heavily on reactive maintenance strategies, where issues were addressed only after machines had already broken down. This approach not only caused unplanned downtime but also increased maintenance costs.
The Digital Maturity Assessment:
The manufacturing plant conducted a Digital Maturity Assessment to evaluate its current digital capabilities and identify areas for improvement. The DMA revealed that the plant lacked real-time data on machine performance and was not using predictive maintenance technologies to prevent equipment failures.
The Solution:
Based on the DMA recommendations, the plant implemented IoT sensors across its machinery to collect real-time data on equipment performance, energy usage, and temperature fluctuations. The plant also adopted an AI-based predictive maintenance system, which analyzed the IoT data to predict when machines were likely to fail.
The Results:
-
Reduced machine downtime by 20%: The predictive maintenance system allowed the plant to address potential equipment issues before they led to breakdowns, significantly reducing downtime.
-
Improved overall equipment efficiency (OEE): With real-time performance data, the plant optimized machine usage, leading to better equipment efficiency and higher production output.
-
Lowered maintenance costs: By performing maintenance only when necessary, the plant reduced labor and spare part costs associated with routine maintenance schedules.
Conclusion
Digital maturity is essential for manufacturers looking to thrive in today’s competitive landscape. By conducting a Digital Maturity Assessment, manufacturers can identify opportunities to optimize their processes, integrate advanced technologies like IoT and AI, and automate critical tasks across production lines and supply chains.
As seen in the real-world use case, increasing digital maturity leads to smarter production lines, reduced machine downtime, and better overall equipment efficiency. Manufacturers that invest in their digital capabilities will be better positioned to improve operational efficiency, enhance product quality, and stay ahead of industry disruptions in the years to come.
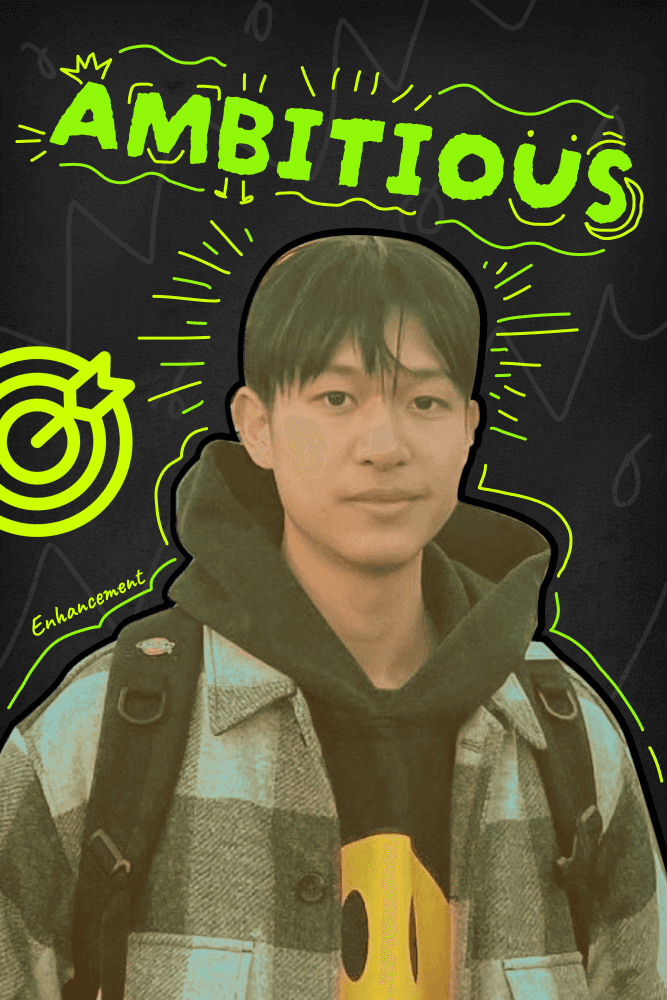
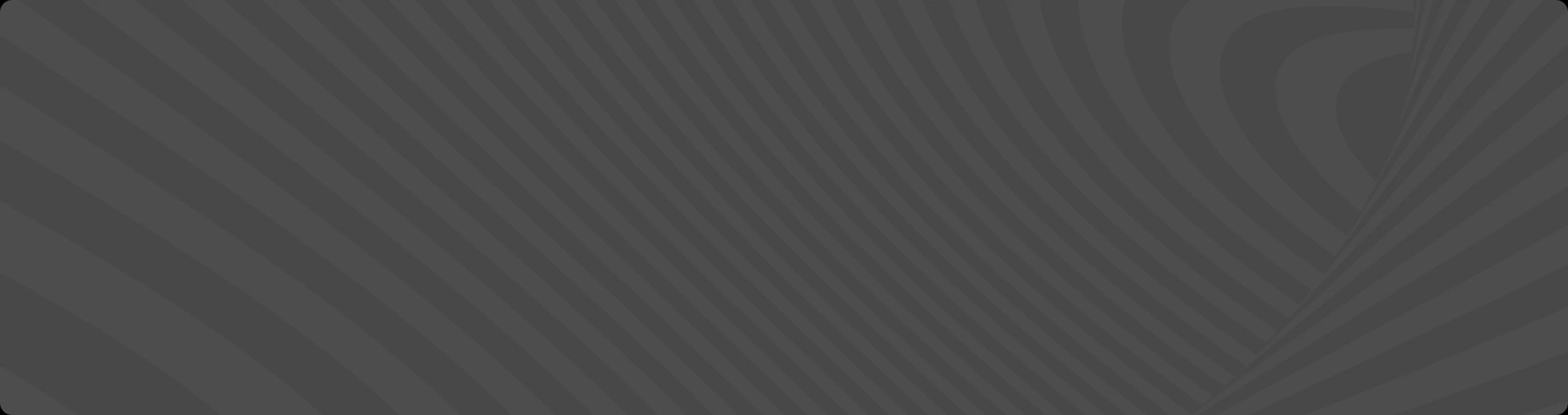
Subscribe to follow product news, latest in technology, solutions, and updates
Other articles for you

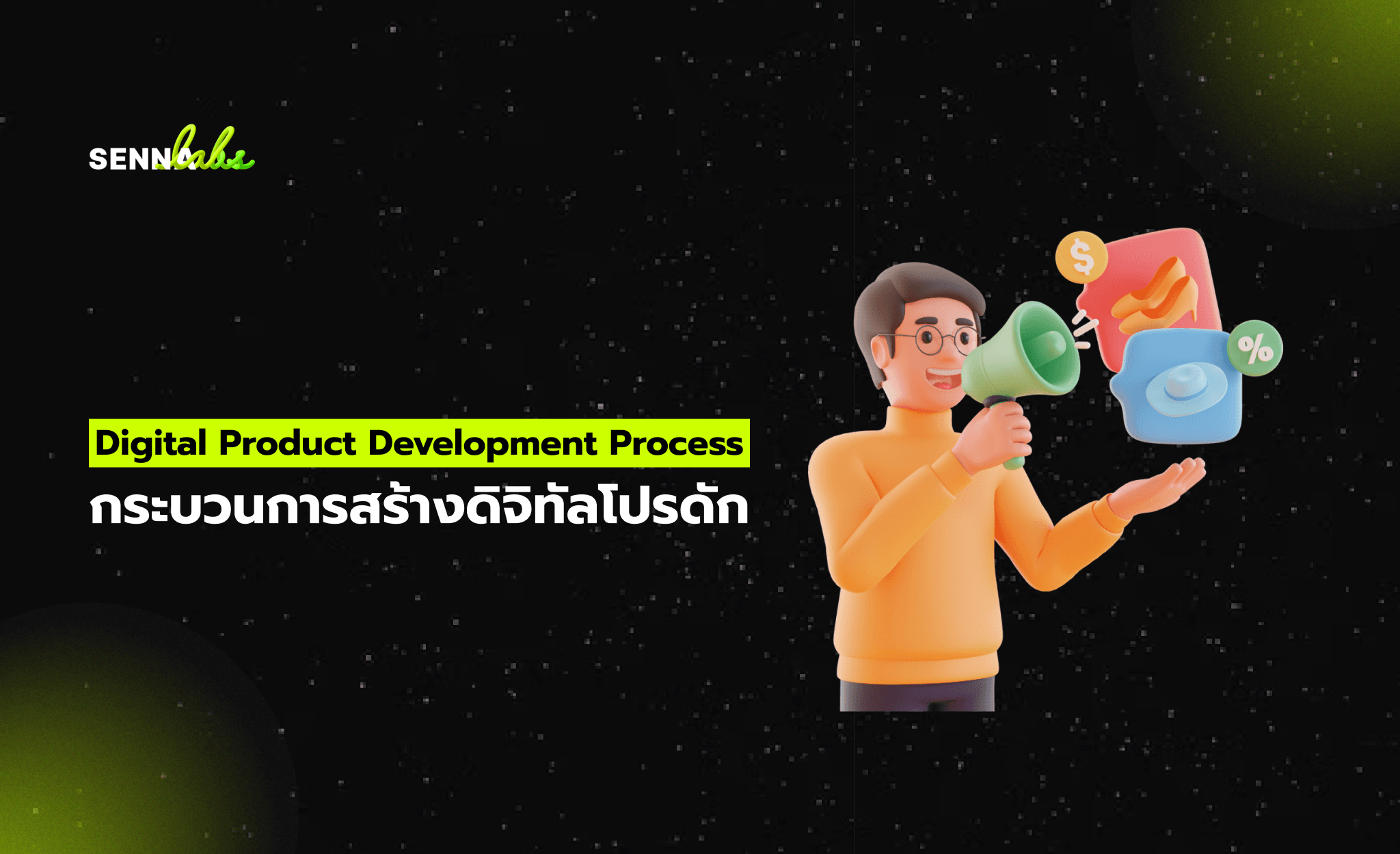
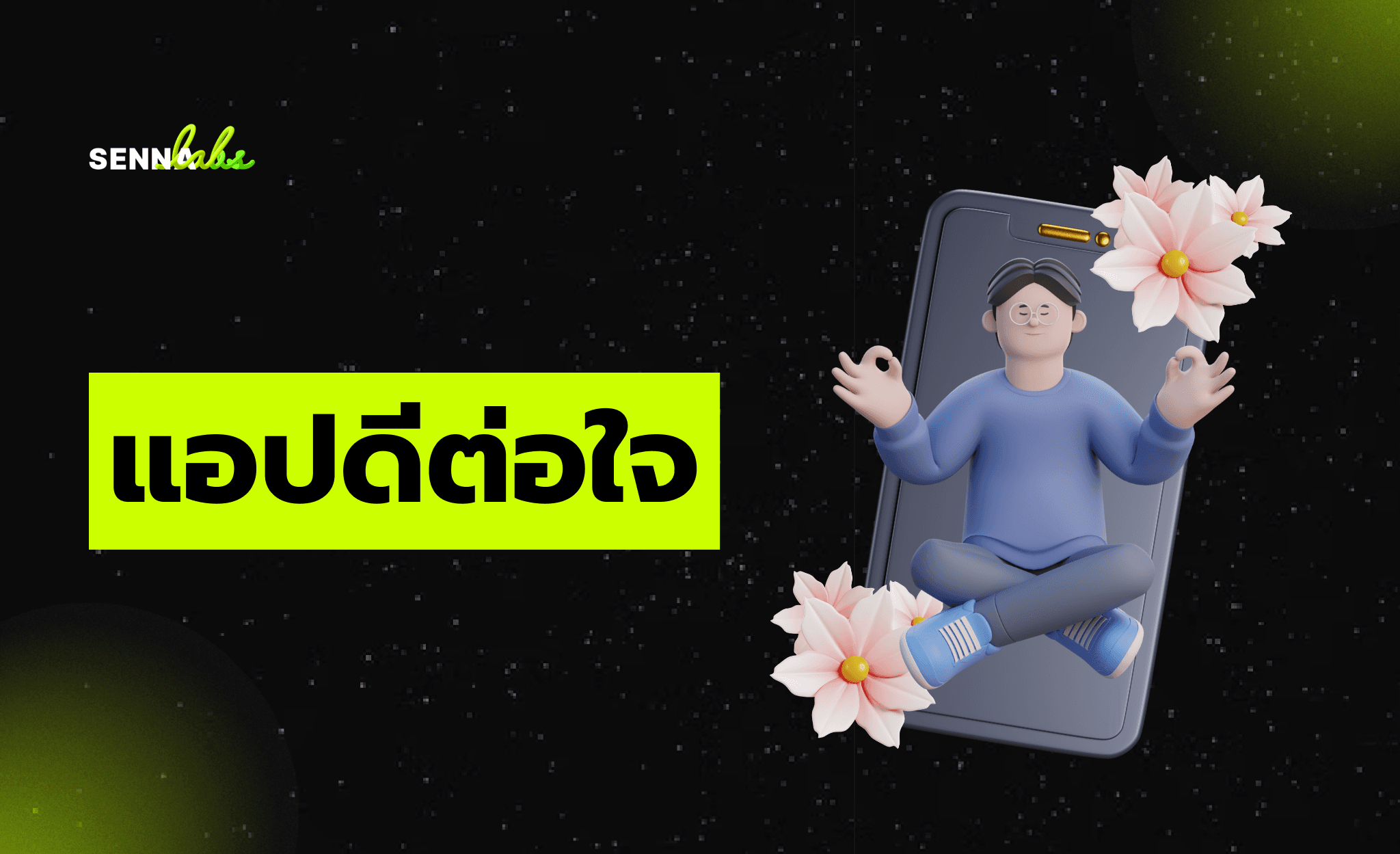
Let’s build digital products that are simply awesome !
We will get back to you within 24 hours!Go to contact us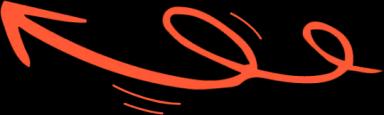
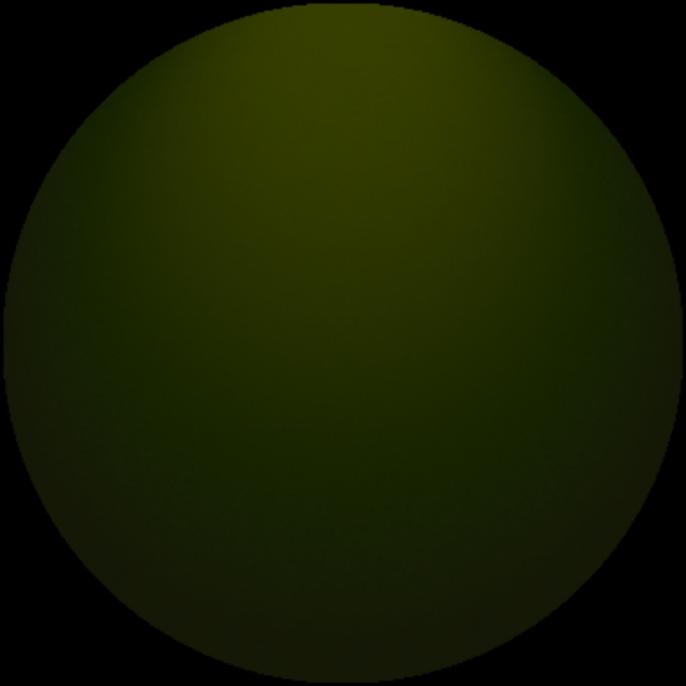
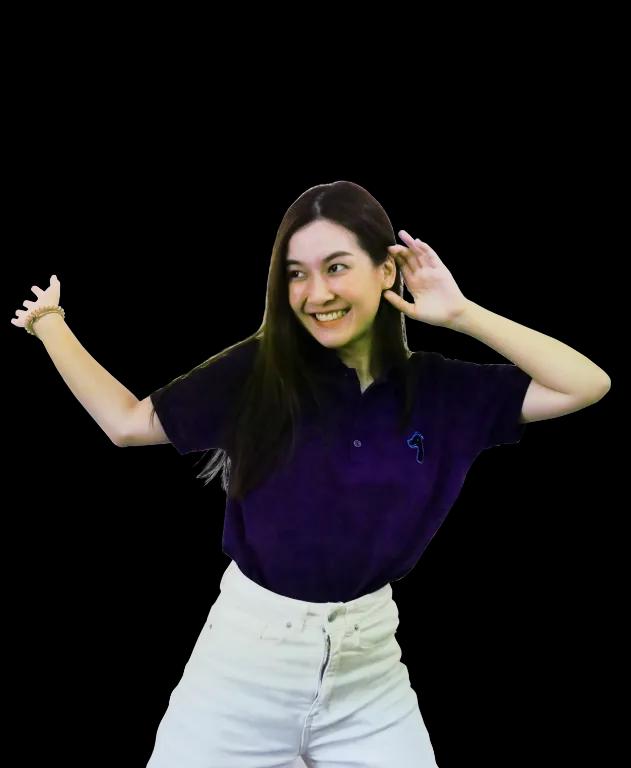
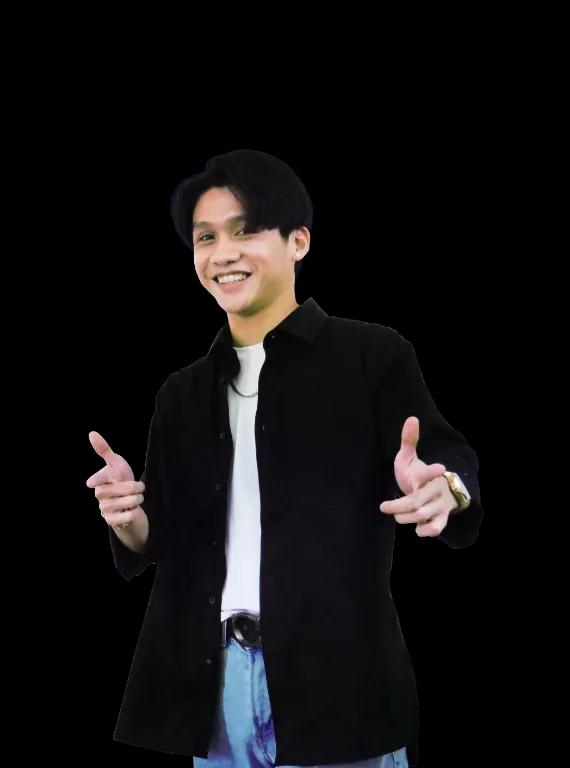
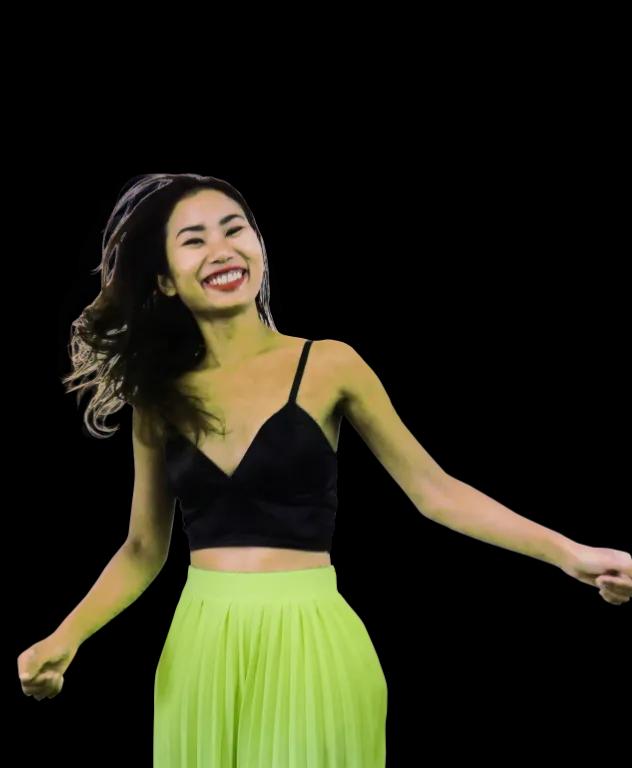
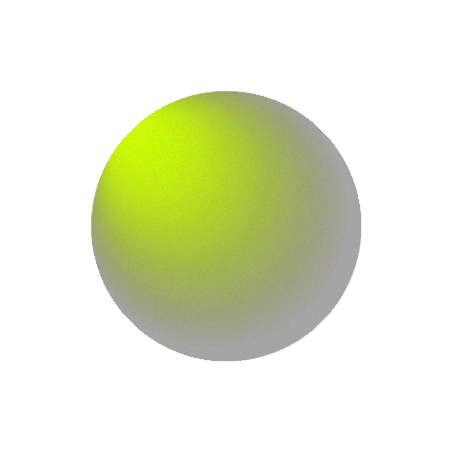
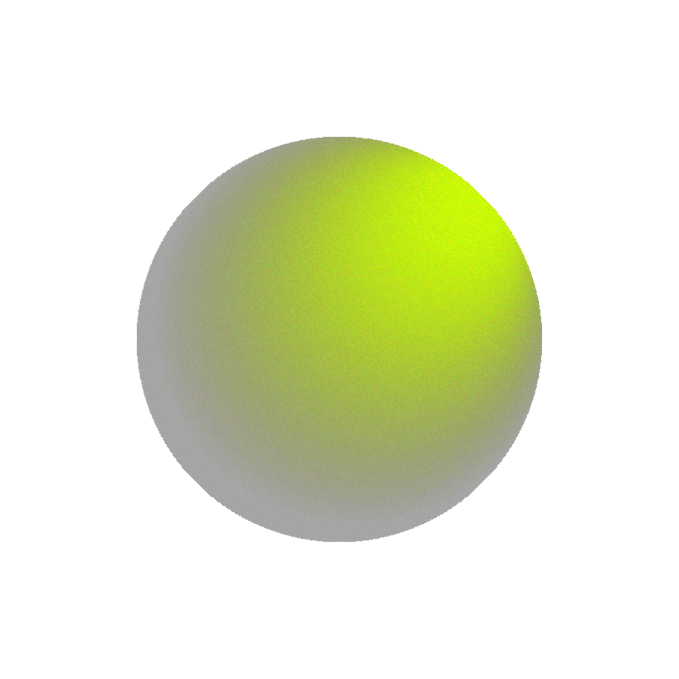
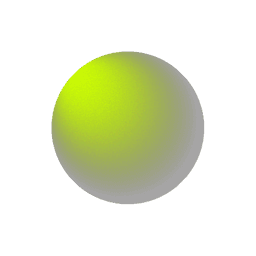
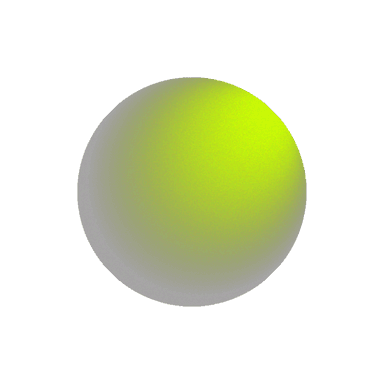
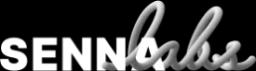