The Role of WMS in Improving Supply Chain Efficiency
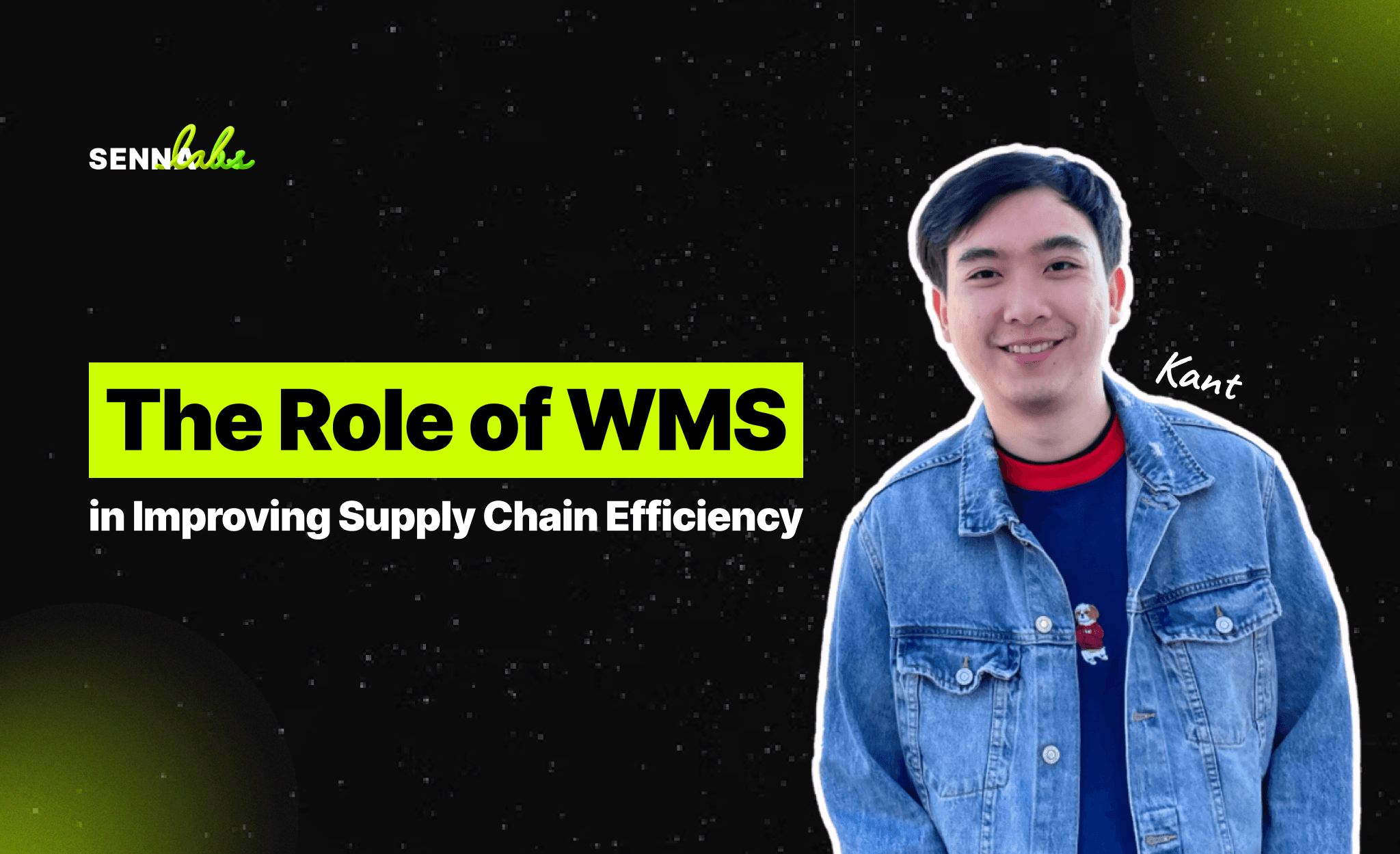
In today’s globalized marketplace, supply chains are more complex than ever, involving multiple stakeholders, interconnected systems, and tight timelines. To thrive in this environment, businesses need tools that enhance visibility, reduce inefficiencies, and promote seamless collaboration across the supply chain. This is where a Warehouse Management System (WMS) plays a critical role.
A WMS provides businesses with real-time data and tools to optimize inventory management, streamline operations, and improve supplier coordination. By integrating a WMS into their supply chain, companies can reduce lead times, enhance decision-making, and improve overall efficiency. In this article, we’ll explore how a WMS transforms supply chain management and share a real-world example of how a manufacturing firm improved supplier collaboration using this technology.
Challenges in Traditional Supply Chain Management
Without a WMS, businesses often face challenges that can disrupt their supply chain, including:
-
Limited Visibility: Lack of real-time inventory data makes it difficult to track stock levels and shipments accurately.
-
Lengthy Lead Times: Inefficient workflows and poor communication with suppliers can result in delays.
-
Inaccurate Forecasting: Inconsistent or outdated data hinders accurate demand forecasting, leading to overstocking or stockouts.
-
Inefficient Supplier Collaboration: Misaligned schedules between warehouses and suppliers create bottlenecks and inefficiencies.
These challenges highlight the need for a robust solution to manage inventory and improve coordination across the supply chain.
How a WMS Improves Supply Chain Efficiency
1. Enhanced Visibility Across the Supply Chain
A WMS provides real-time visibility into inventory levels, shipments, and order statuses across all locations. This transparency enables businesses to make informed decisions and respond proactively to changes in demand or supply.
-
How It Works: The WMS integrates with ERP systems, transportation management software, and supplier databases to create a unified view of the supply chain.
-
Benefits:
-
Accurate tracking of inbound and outbound shipments.
-
Faster identification of potential disruptions.
-
Better alignment between inventory levels and customer demand.
2. Reduced Lead Times
By streamlining warehouse operations and automating workflows, a WMS helps businesses reduce lead times for both procurement and order fulfillment.
-
How It Works:
-
Automated inventory replenishment triggers orders to suppliers based on real-time stock levels.
-
Optimized picking, packing, and shipping processes ensure faster order fulfillment.
-
Benefits:
-
Quicker response to changes in demand.
-
Reduced delays in production due to inventory shortages.
3. Improved Supplier Collaboration
A WMS fosters better communication and coordination with suppliers by providing real-time updates on inventory needs and delivery schedules.
-
How It Works: Suppliers can access shared portals or dashboards to view demand forecasts, delivery schedules, and inventory levels in real time.
-
Benefits:
-
Minimized stockouts and overstocking.
-
Streamlined deliveries that align with production schedules.
-
Enhanced trust and collaboration with suppliers.
4. Optimized Inventory Management
With a WMS, businesses can maintain optimal inventory levels by automating stock replenishment and forecasting future needs.
-
How It Works:
-
Advanced analytics in the WMS predict future demand based on historical data and trends.
-
Automated alerts notify teams when inventory reaches predefined thresholds.
-
Benefits:
-
Reduced carrying costs associated with excess inventory.
-
Improved service levels by ensuring stock availability.
5. Data-Driven Decision-Making
WMS solutions generate detailed reports and analytics on supply chain performance, enabling businesses to identify bottlenecks and optimize processes.
-
How It Works:
-
Real-time data on warehouse operations, supplier performance, and shipping times feed into dashboards and reports.
-
AI-driven insights recommend process improvements.
-
Benefits:
-
Faster identification of inefficiencies.
-
Better allocation of resources.
-
Increased overall supply chain agility.
Real-World Use Case: A Manufacturing Firm’s Success Story
A manufacturing firm faced challenges in coordinating supplier deliveries and production schedules. Their manual processes led to frequent delays, excess inventory, and inefficiencies in aligning production with raw material availability.
Solution: The firm implemented a Warehouse Management System (WMS) integrated with their ERP and supplier portals. Key features included:
-
Real-Time Inventory Tracking: The WMS monitored raw material levels and automatically notified suppliers when inventory needed replenishing.
-
Delivery Scheduling: Suppliers accessed a shared portal to view production schedules and align deliveries accordingly.
-
Automated Replenishment: The WMS triggered purchase orders based on forecasted demand and predefined thresholds.
Results:
-
Reduced Lead Times: Lead times for raw material delivery decreased by 20%, ensuring uninterrupted production.
-
Improved Supplier Coordination: Suppliers delivered materials on time, reducing delays and stockouts.
-
Enhanced Production Efficiency: With synchronized deliveries and production schedules, the firm minimized downtime and improved operational efficiency.
Best Practices for WMS Integration in Supply Chains
-
Map Your Supply Chain Needs: Understand your inventory, supplier, and production requirements before selecting a WMS.
-
Ensure Seamless Integration: Choose a WMS that integrates with your ERP, supplier systems, and other tools for end-to-end visibility.
-
Leverage Automation: Automate repetitive tasks like stock replenishment, order tracking, and delivery scheduling to improve efficiency.
-
Train Your Team: Provide comprehensive training to warehouse staff and suppliers on how to use the WMS effectively.
-
Monitor and Optimize: Continuously analyze data from the WMS to identify areas for improvement and refine processes.
Conclusion: A Smarter Supply Chain with WMS
A Warehouse Management System is more than just a tool for inventory management—it’s a strategic asset that drives efficiency across the entire supply chain. By enhancing visibility, reducing lead times, and fostering better collaboration with suppliers, a WMS empowers businesses to operate more efficiently and respond to market demands with agility.
The success of the manufacturing firm in synchronizing supplier deliveries and production schedules demonstrates the transformative potential of a WMS. Whether you’re managing raw materials for production or fulfilling customer orders, integrating a WMS into your supply chain can unlock new levels of performance and profitability.
Start your journey toward a more efficient supply chain by exploring WMS solutions that align with your business needs today.

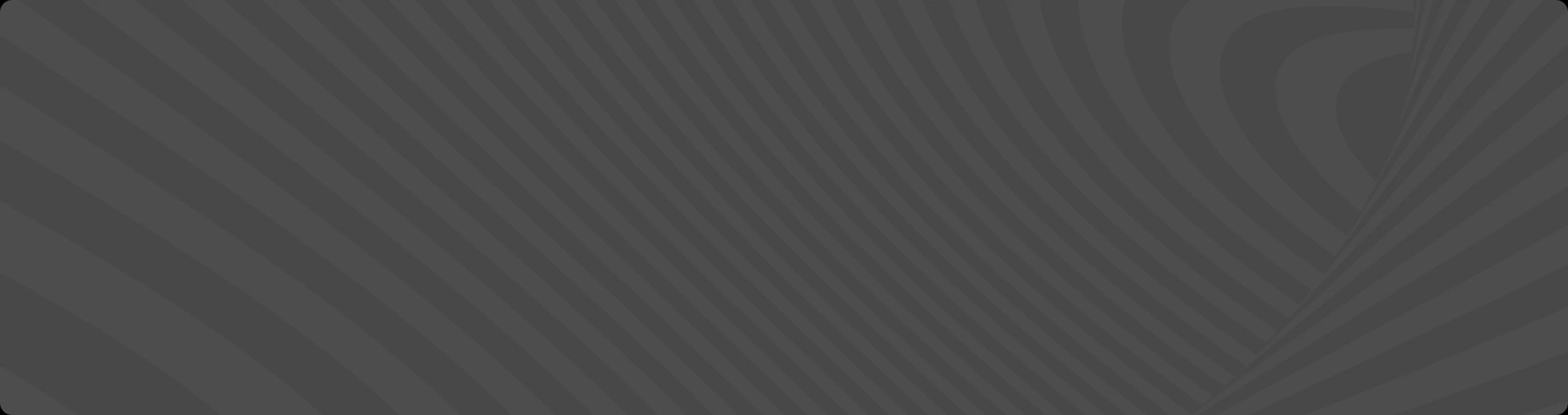
Subscribe to follow product news, latest in technology, solutions, and updates
Other articles for you
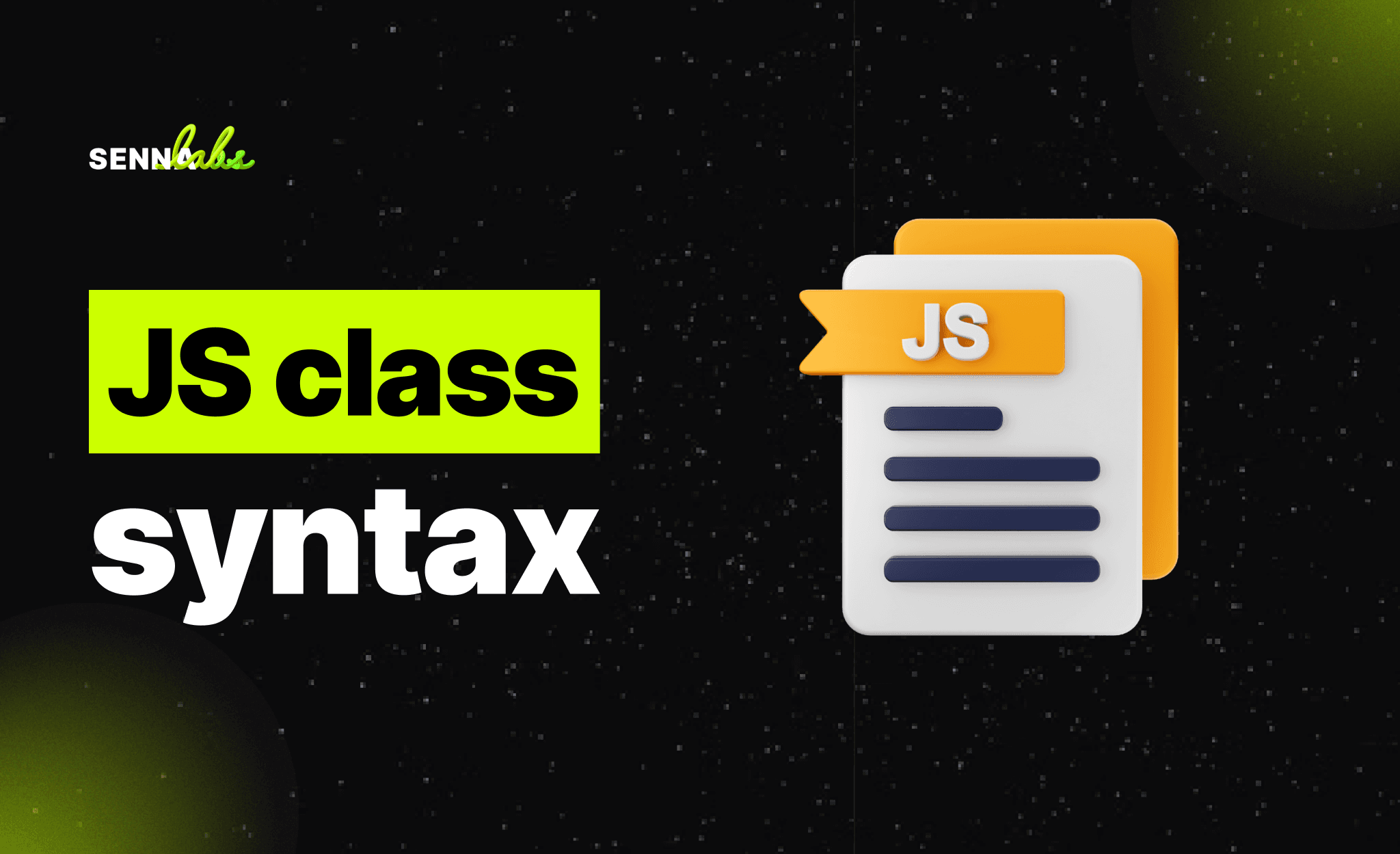
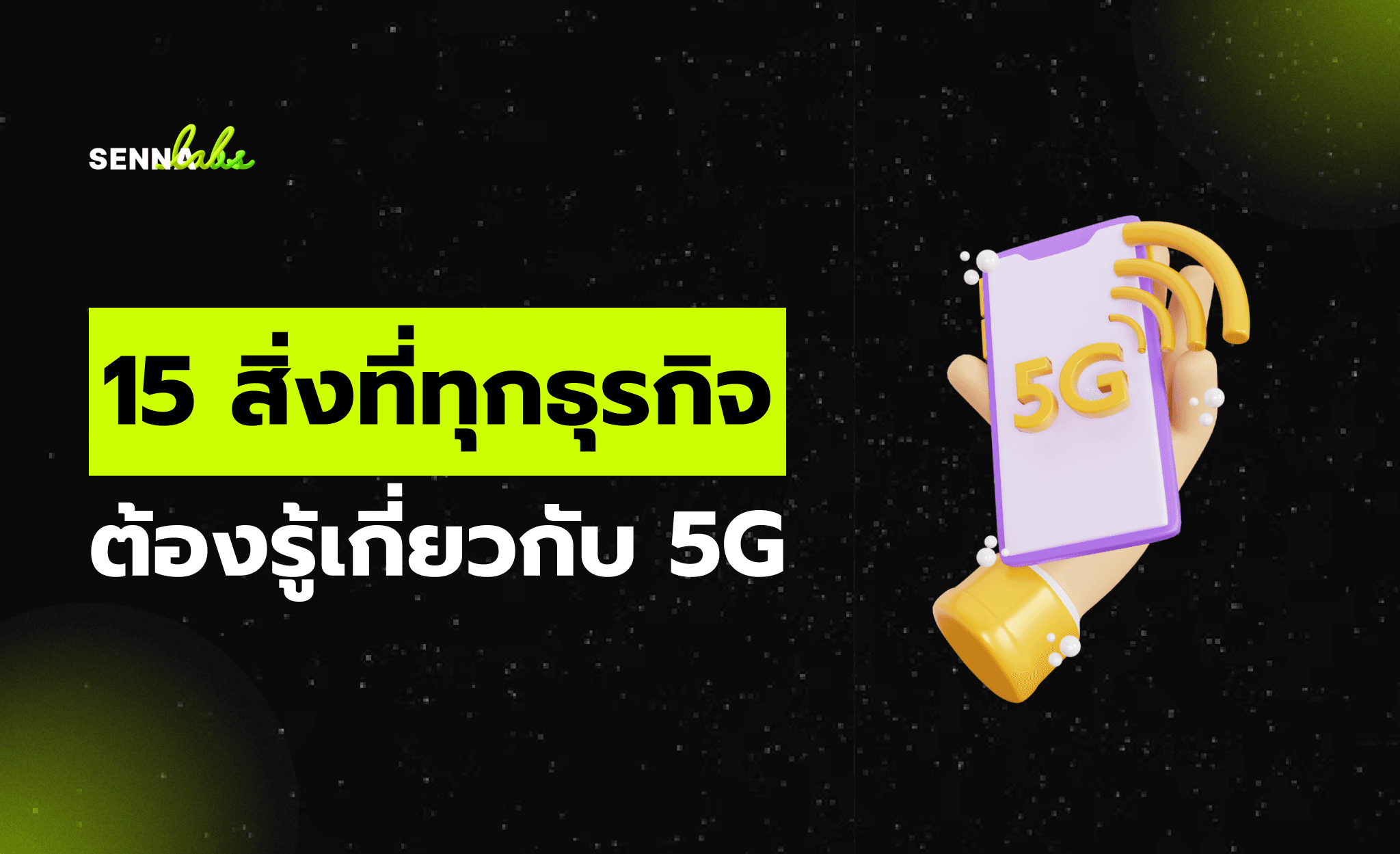
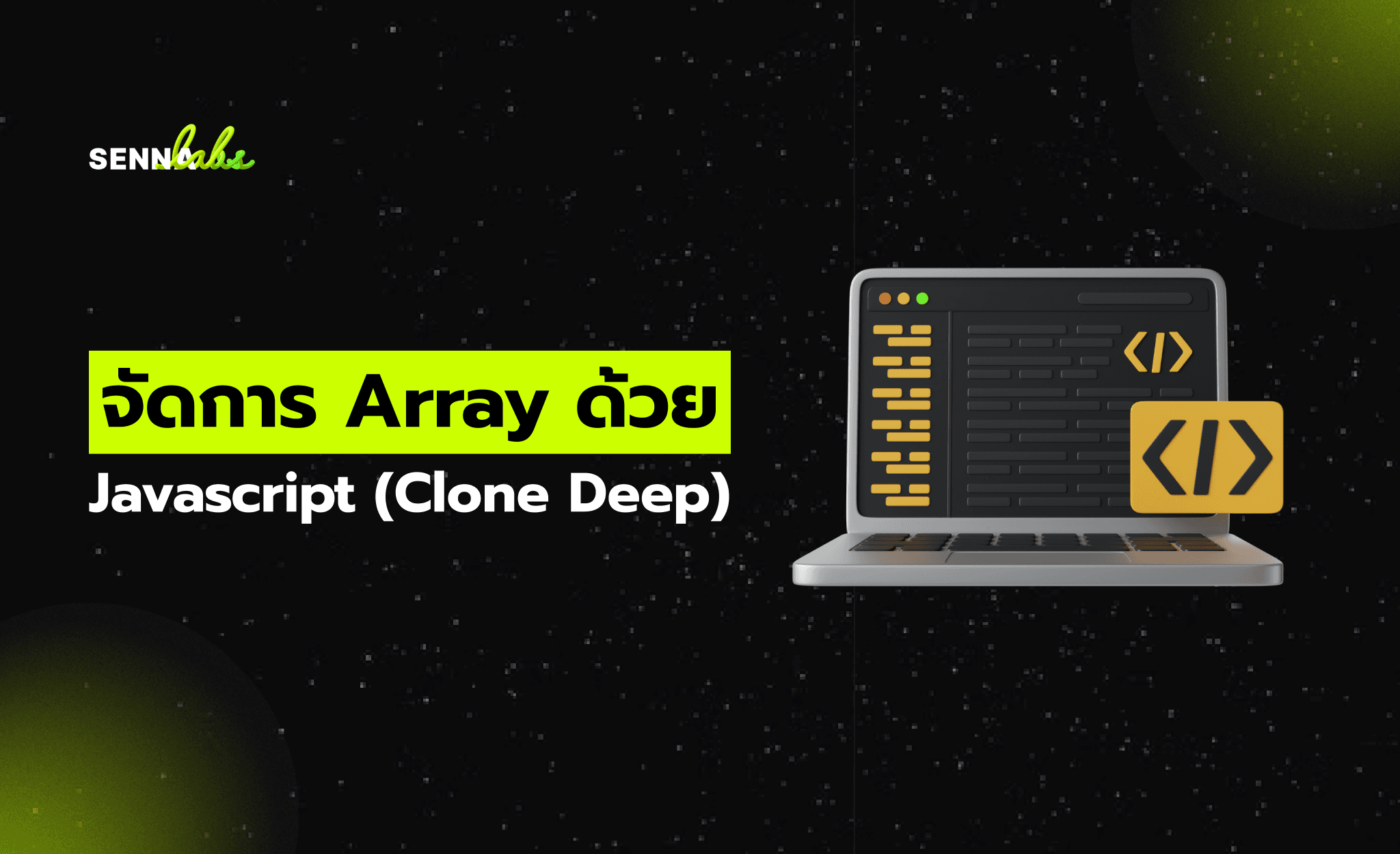
Let’s build digital products that are simply awesome !
We will get back to you within 24 hours!Go to contact us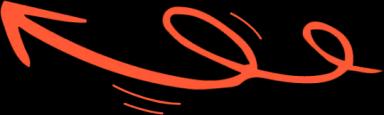
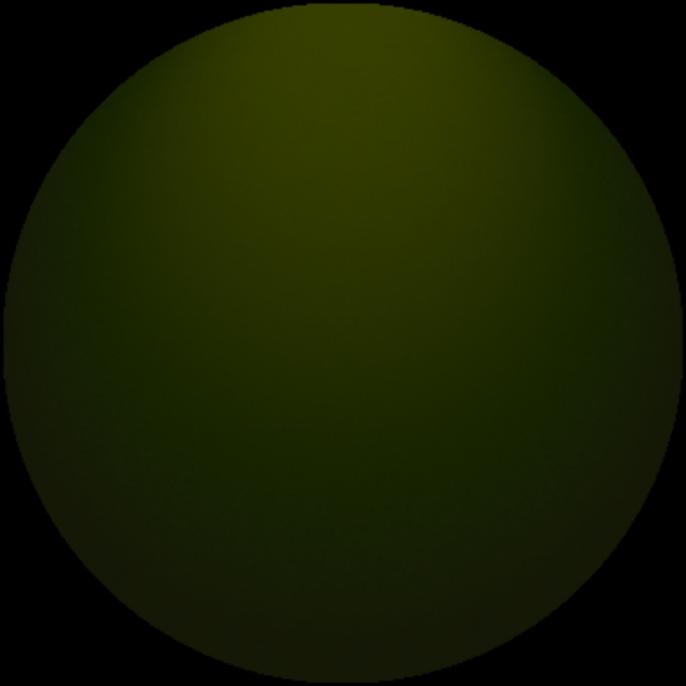
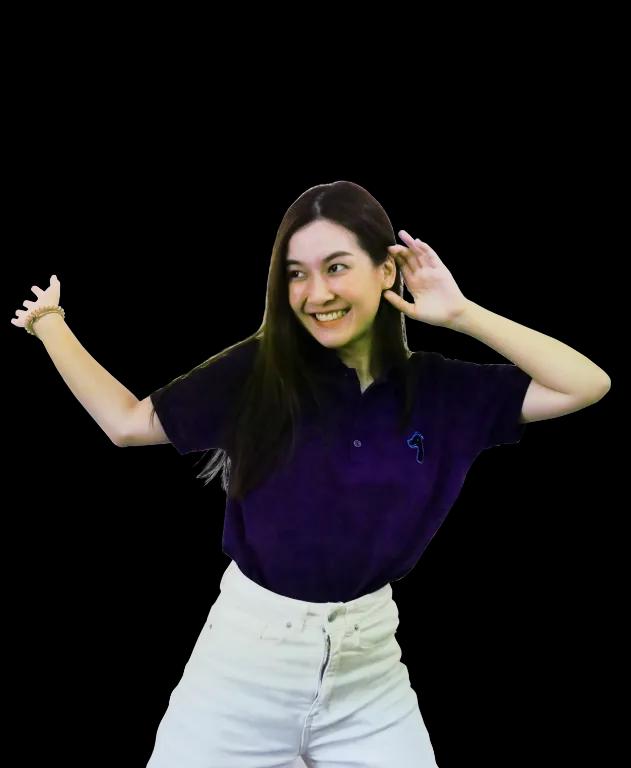
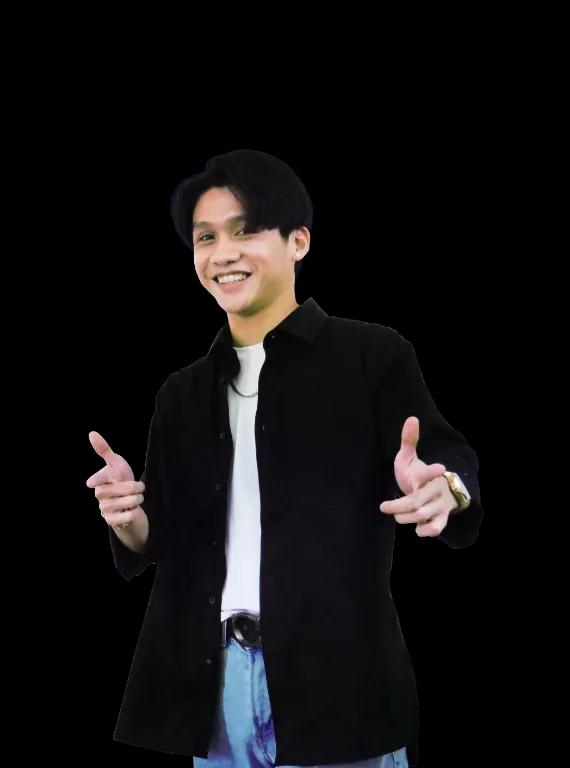
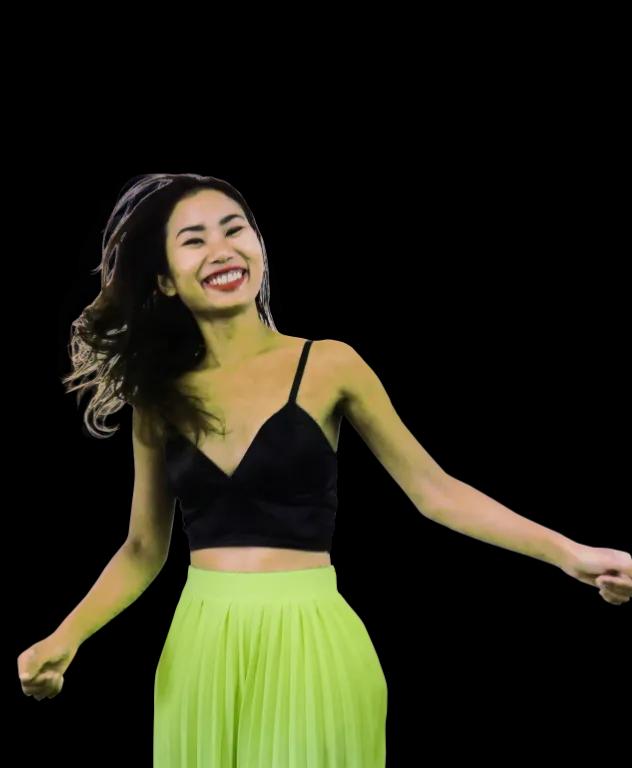
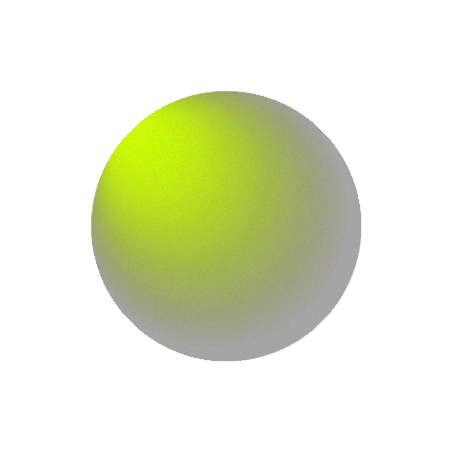
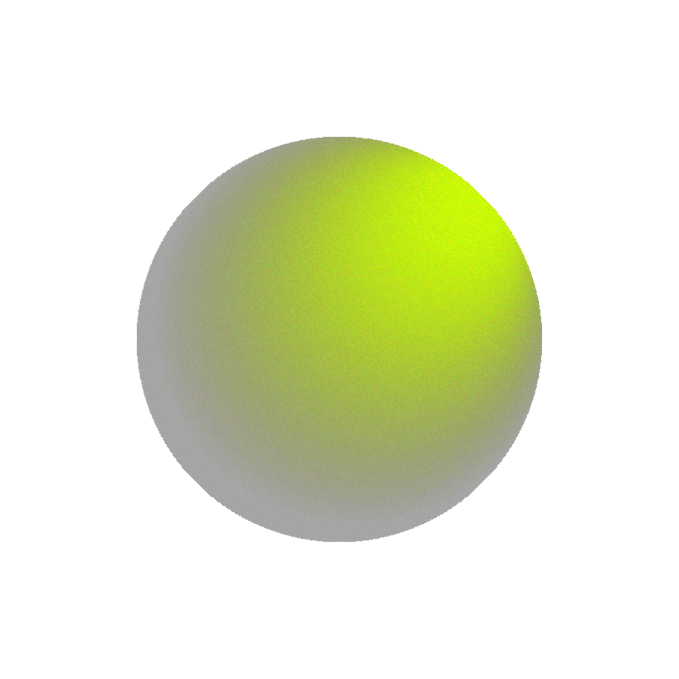
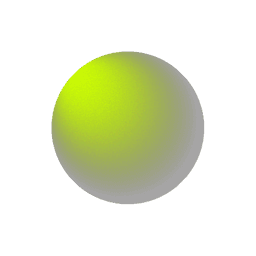
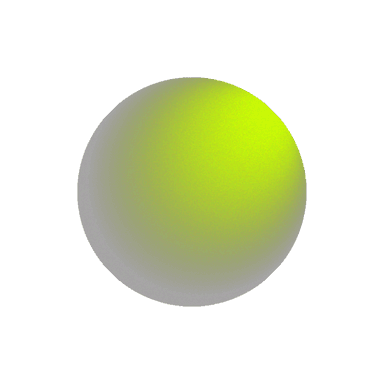
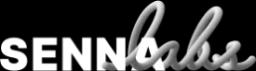