Predictive Maintenance Software in Manufacturing: Revolutionizing Efficiency and Reducing Downtime
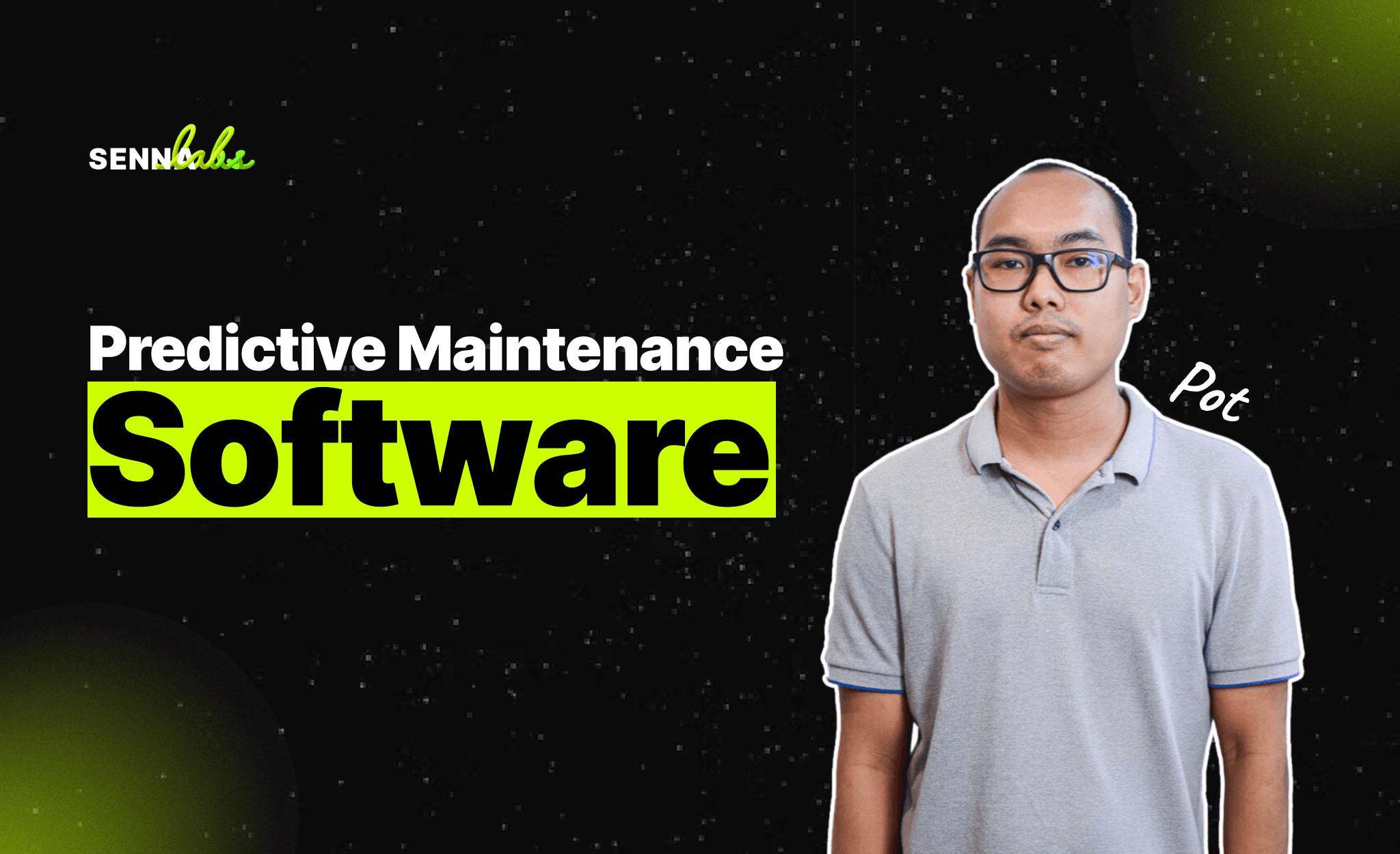
In the ever-evolving landscape of manufacturing, maintaining optimal operational efficiency is paramount. Unplanned downtime can lead to significant financial losses, disrupt supply chains, and erode customer trust. Enter predictive maintenance software—an innovative solution that leverages advanced analytics, machine learning, and IoT (Internet of Things) to predict equipment failures before they happen, thereby transforming the maintenance paradigm from reactive to proactive.
What is Predictive Maintenance?
Predictive maintenance (PdM) is a technique that uses data-driven tools and technologies to monitor the condition of equipment and predict when maintenance should be performed. This approach differs from traditional maintenance strategies, such as reactive maintenance (repairing equipment after failure) and preventive maintenance (scheduled maintenance regardless of equipment condition). PdM aims to maximize equipment uptime, enhance productivity, and minimize maintenance costs.
How Predictive Maintenance Software Works
-
Data Collection: PdM software collects data from various sensors embedded in manufacturing equipment. These sensors monitor a range of parameters, including temperature, vibration, pressure, and more.
-
Data Processing: The collected data is processed and analyzed using advanced algorithms and machine learning models. This analysis helps identify patterns and anomalies that indicate potential equipment failures.
-
Prediction and Alerts: Based on the analysis, the software predicts when a piece of equipment is likely to fail and sends alerts to maintenance teams. This allows them to perform maintenance tasks at the optimal time, preventing unexpected breakdowns.
-
Integration with IoT and ERP Systems: PdM software can integrate with IoT devices and Enterprise Resource Planning (ERP) systems, providing a seamless flow of information across the manufacturing ecosystem. This integration enhances decision-making and streamlines maintenance operations.
Benefits of Predictive Maintenance Software
-
Reduced Downtime: By predicting failures before they occur, PdM significantly reduces unplanned downtime. This ensures that manufacturing processes remain uninterrupted and production schedules are adhered to.
-
Cost Savings: Preventing unexpected equipment failures and optimizing maintenance schedules can lead to substantial cost savings. Manufacturers can avoid costly repairs and extend the lifespan of their equipment.
-
Improved Safety: Predictive maintenance helps identify potential safety hazards before they lead to accidents, thereby enhancing workplace safety.
-
Enhanced Productivity: With equipment running smoothly and reliably, overall productivity increases. Maintenance tasks can be planned and executed without disrupting the production flow.
-
Data-Driven Insights: PdM software provides valuable insights into equipment performance and health, enabling manufacturers to make informed decisions about asset management and process improvements.
Implementing Predictive Maintenance Software
For manufacturers considering the implementation of predictive maintenance software, here are some key steps to ensure a successful deployment:
-
Assess Current Maintenance Practices: Evaluate your existing maintenance strategies and identify areas where predictive maintenance can add value.
-
Invest in the Right Technology: Choose a PdM solution that fits your specific needs. Look for features such as real-time monitoring, machine learning capabilities, and integration with existing systems.
-
Start Small and Scale: Begin with a pilot project on critical equipment to demonstrate the value of PdM. Once proven, scale the implementation across other assets.
-
Train Your Team: Ensure that your maintenance and operations teams are trained to use the new software effectively. Familiarity with data analysis and interpretation is crucial for maximizing the benefits of PdM.
-
Monitor and Optimize: Continuously monitor the performance of your PdM system and make adjustments as needed. Regularly review the data and refine your maintenance strategies based on insights gained.
Conclusion
Predictive maintenance software is a game-changer for the manufacturing industry. By leveraging the power of data and advanced analytics, manufacturers can achieve unprecedented levels of efficiency, reliability, and cost-effectiveness. As an IT consulting company specializing in custom software solutions, we are committed to helping businesses harness the potential of predictive maintenance technology to stay ahead in a competitive market. Contact us today to learn how we can tailor a PdM solution to meet your unique needs and drive your manufacturing operations to new heights.
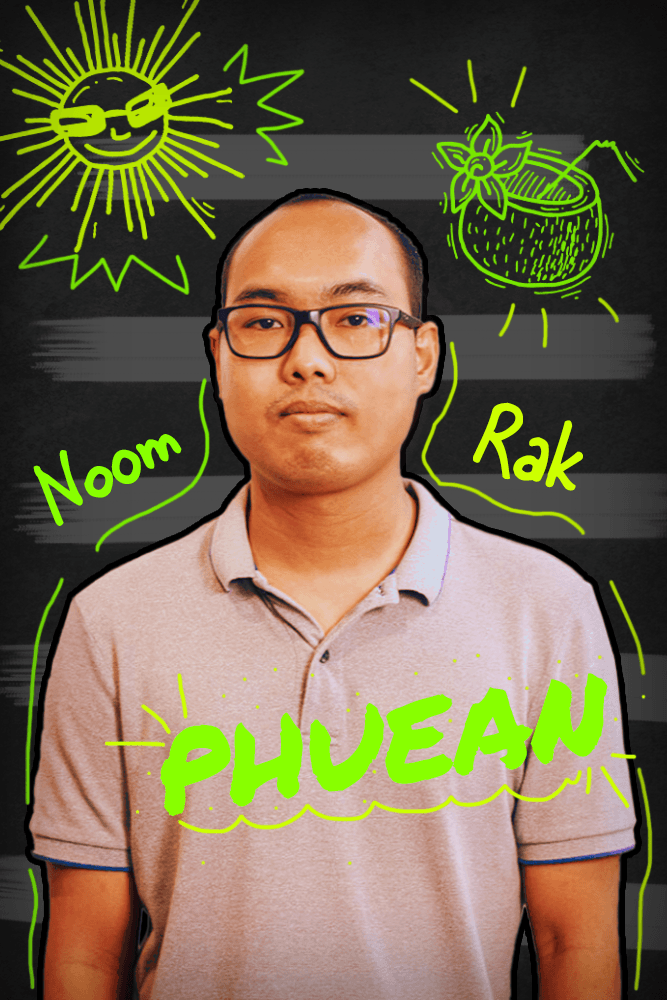
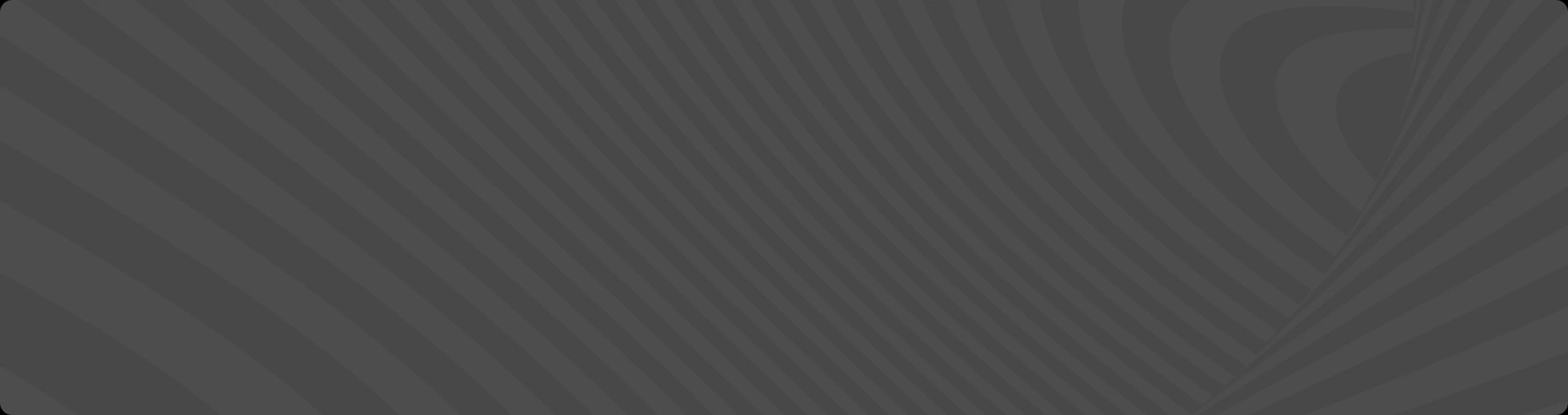
Subscribe to follow product news, latest in technology, solutions, and updates
Other articles for you
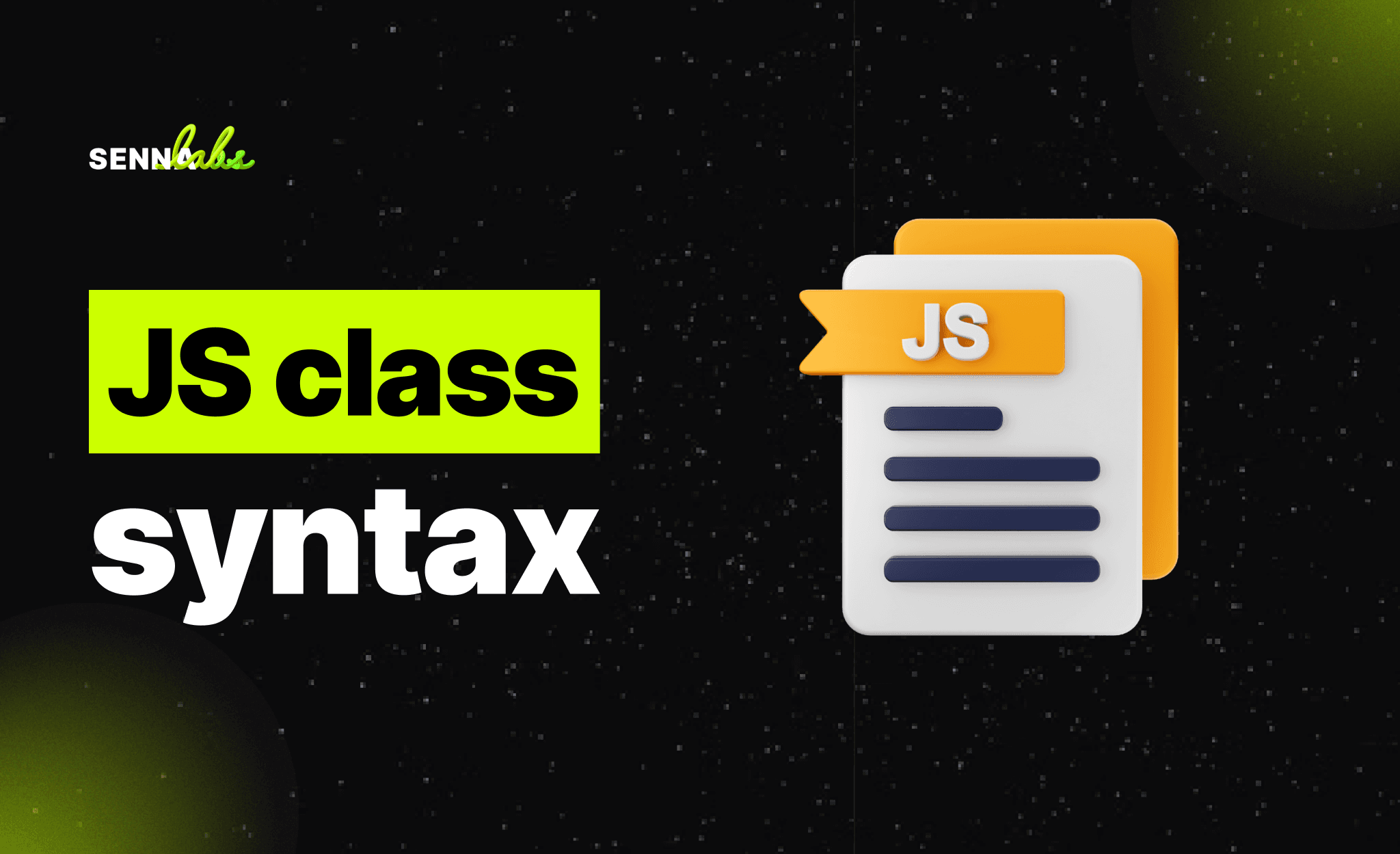
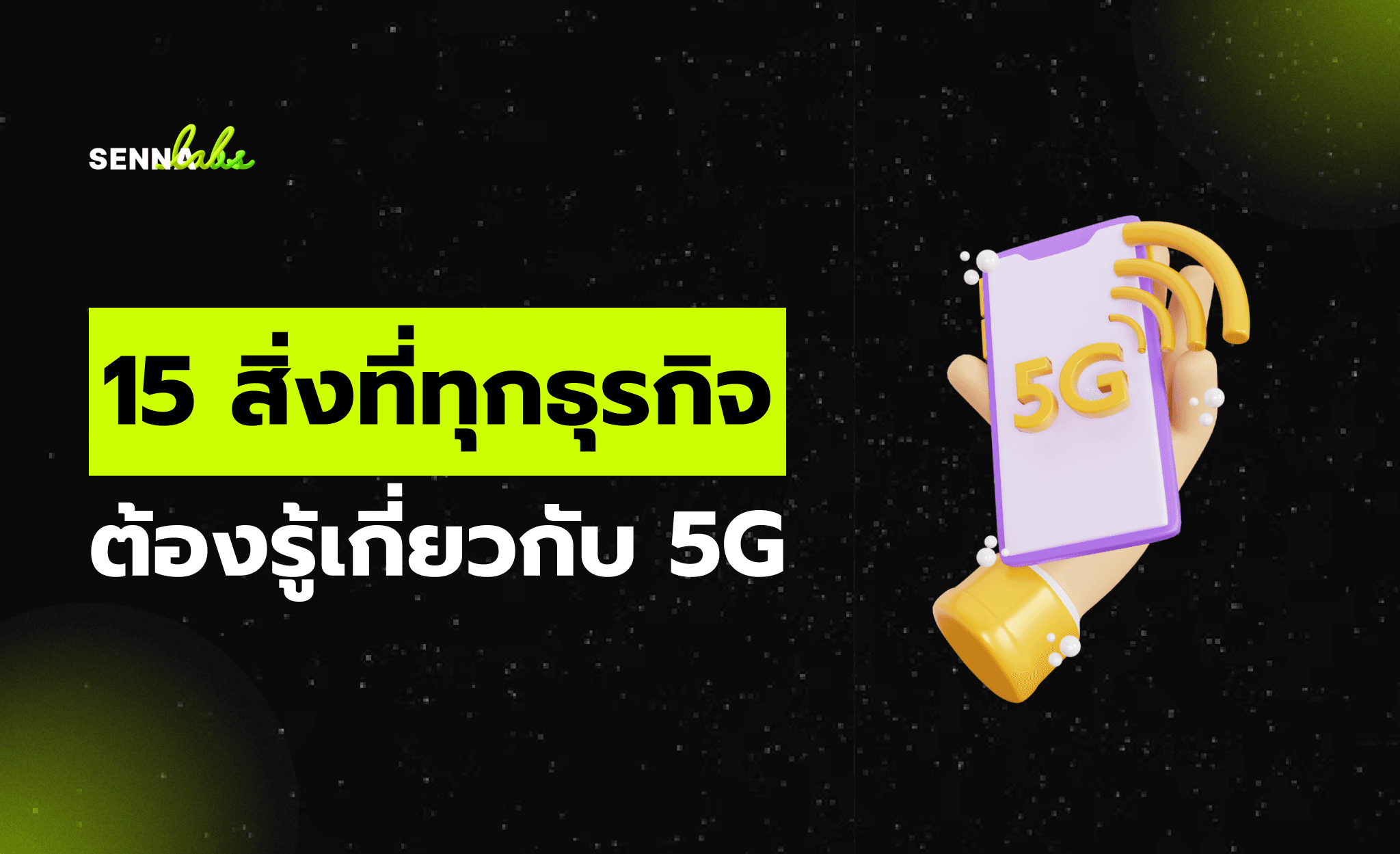
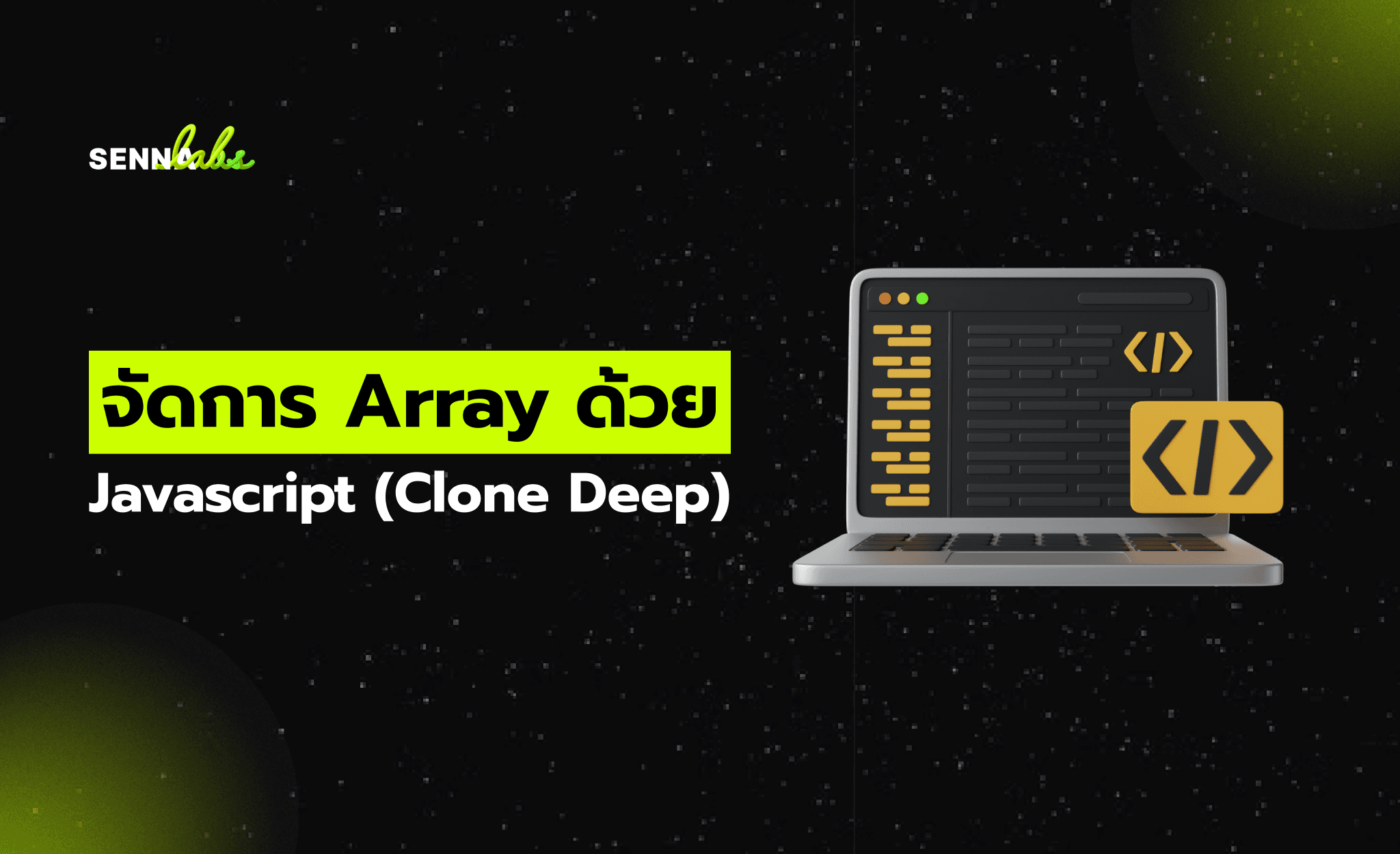
Let’s build digital products that are simply awesome !
We will get back to you within 24 hours!Go to contact us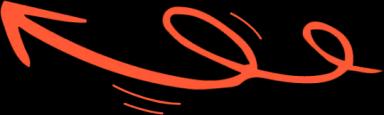
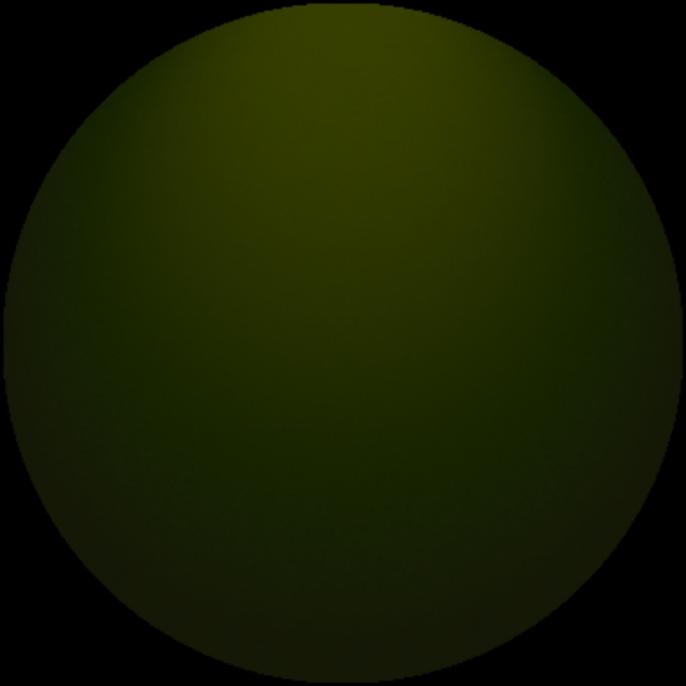
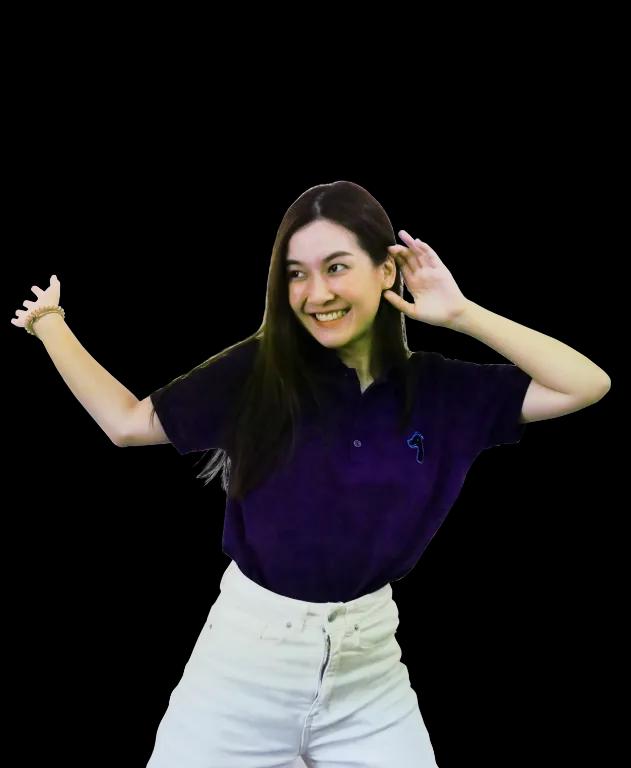
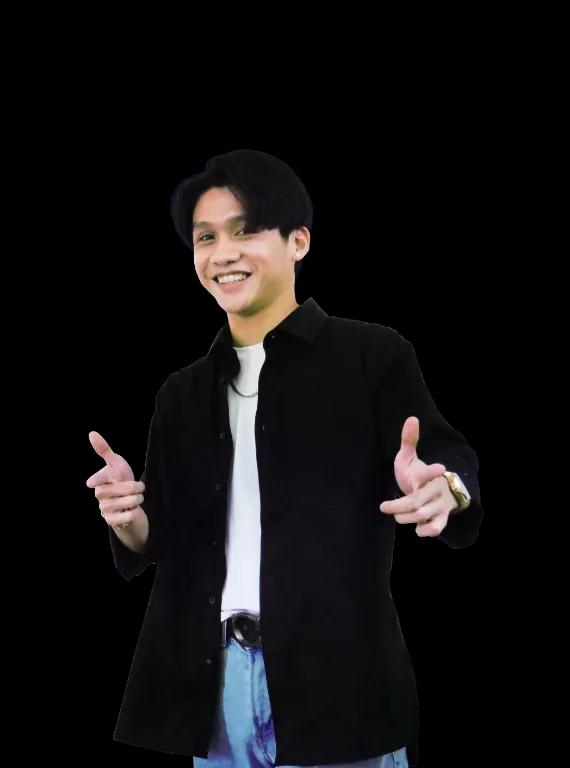
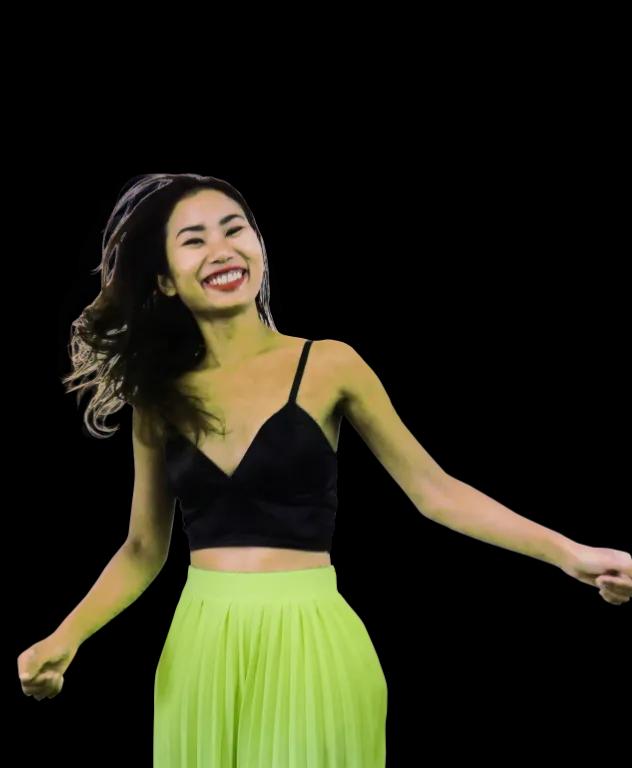
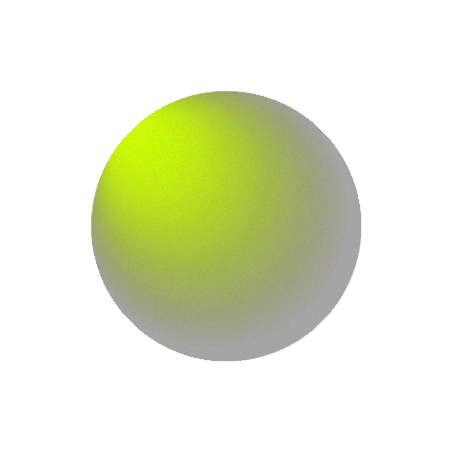
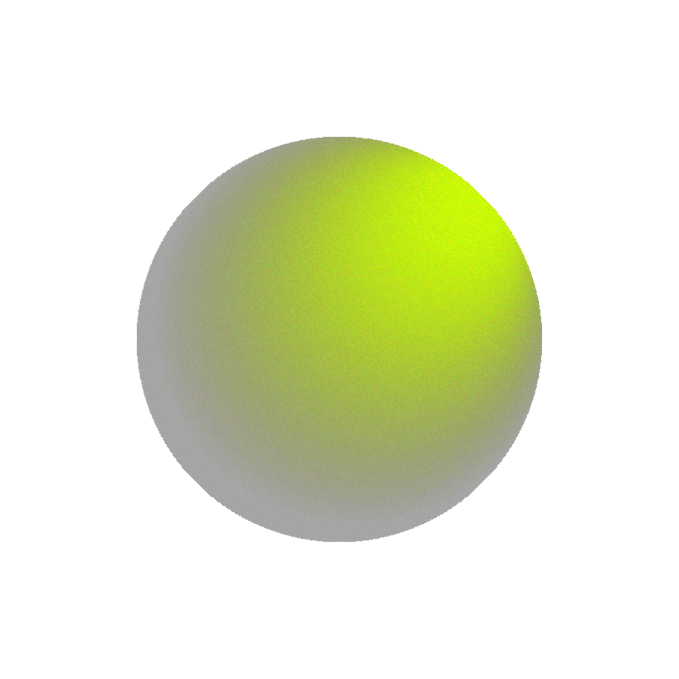
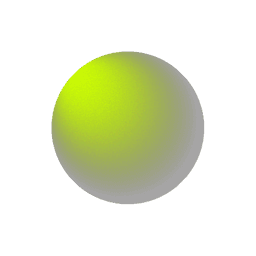
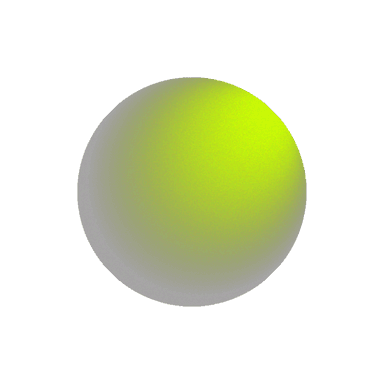
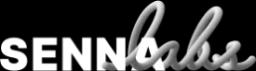