Optimizing Multi-Location Inventory with Software Solutions
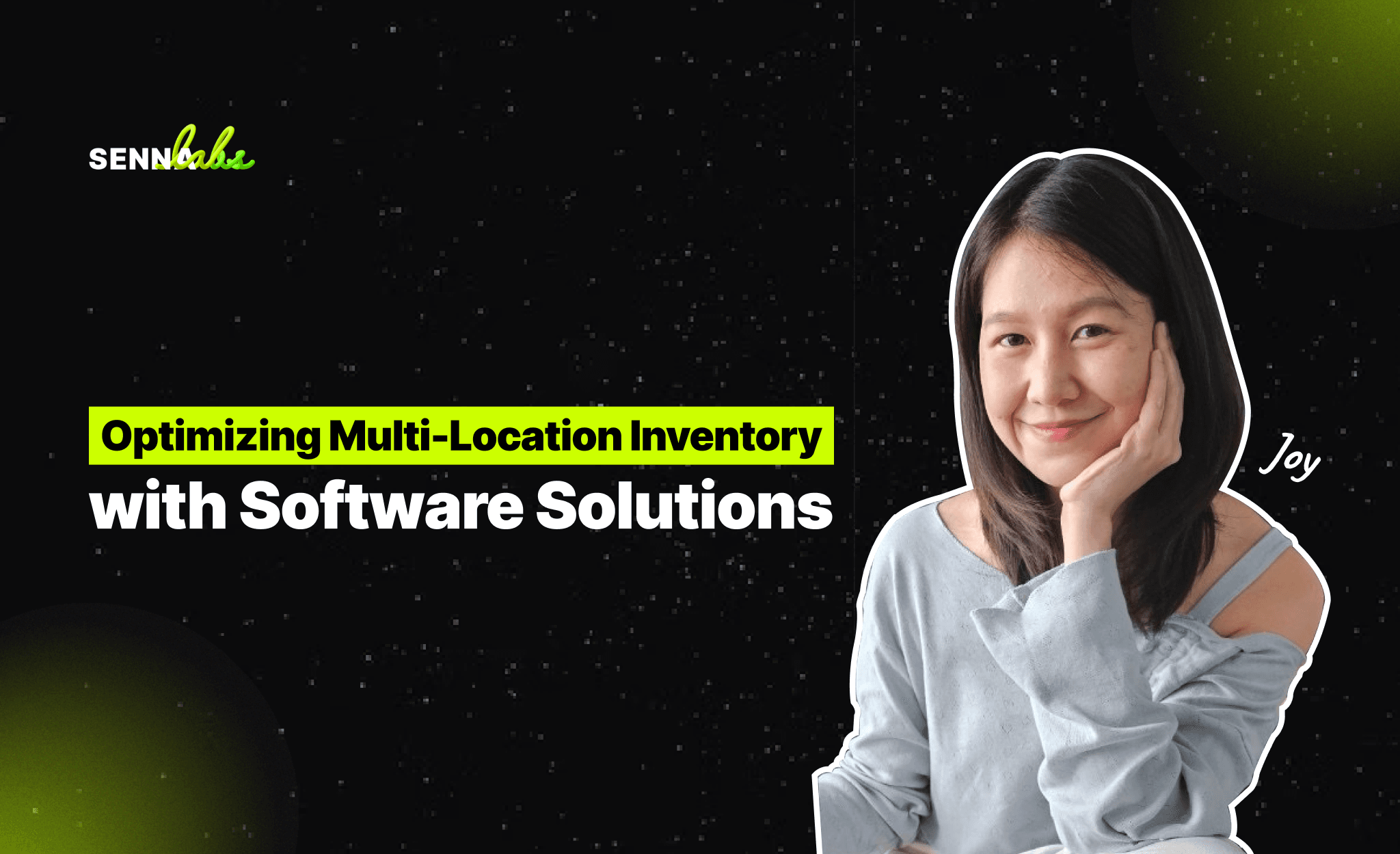
For businesses operating multiple warehouses or retail locations, managing inventory effectively can be a daunting task. Without proper systems in place, businesses face stock imbalances, delayed transfers, and difficulty meeting customer expectations. Ensuring that inventory is appropriately distributed across all locations while maintaining efficiency requires a centralized and streamlined approach.
This is where inventory management software comes into play. By providing real-time visibility and control over inventory across all locations, these tools enable businesses to optimize stock levels, reduce transfer delays, and enhance customer satisfaction. This article explores how inventory software helps manage multi-location inventory and shares how a furniture retailer successfully used these tools to improve stock distribution.
The Challenges of Multi-Location Inventory Management
Managing inventory across multiple locations comes with unique challenges, including:
-
Stock Imbalances: Some locations may overstock slow-moving items while others run out of high-demand products.
-
Lack of Centralized Visibility: Without a unified system, it’s difficult to get a clear picture of inventory levels across all sites.
-
Inefficient Transfers: Moving inventory between locations without proper planning can result in delays and increased costs.
-
Inconsistent Customer Experience: Customers may face longer wait times if items aren’t available at their nearest location.
-
Manual Errors: Relying on spreadsheets or disconnected systems often leads to discrepancies and inefficiencies.
How Inventory Management Software Optimizes Multi-Location Inventory
1. Centralized Data Management
Inventory software consolidates data from all warehouses and retail locations into a single platform, providing a unified view of stock levels, movements, and demand trends.
-
How It Works:
-
Each location’s inventory updates in real time, enabling managers to track stock accurately across the network.
-
Central dashboards allow easy monitoring of stock levels, transfers, and sales performance.
-
Benefits:
-
Prevents stockouts and overstocking.
-
Streamlines decision-making with comprehensive insights.
2. Automated Stock Reallocation
Inventory systems use advanced algorithms to identify stock imbalances and recommend or automate transfers between locations to optimize distribution.
-
How It Works:
-
The software monitors demand at each location and suggests transferring excess stock from one site to another.
-
Automated alerts trigger replenishment orders or stock transfers based on predefined thresholds.
-
Benefits:
-
Ensures all locations have the right products at the right time.
-
Reduces excess inventory and carrying costs.
3. Demand Forecasting
Modern inventory solutions analyze historical data and current trends to predict future demand, enabling proactive inventory planning across all locations.
-
How It Works:
-
Demand forecasts are tailored to each location’s unique sales patterns, ensuring stock aligns with customer needs.
-
Seasonal trends and regional preferences are factored into predictions.
-
Benefits:
-
Improves stock availability during peak periods.
-
Minimizes wasted resources from overstocking.
4. Real-Time Inventory Tracking
Inventory management software provides real-time updates on stock movements, helping businesses respond quickly to changes in demand or supply chain disruptions.
-
How It Works:
-
Integrated tools like barcode scanners and RFID track inventory as it moves between locations.
-
Real-time dashboards display stock levels and movements instantly.
-
Benefits:
-
Reduces delays in inventory transfers.
-
Enhances accuracy in order fulfillment.
5. Integration with Sales Channels
For businesses with both online and physical stores, inventory software integrates with e-commerce platforms and point-of-sale (POS) systems to synchronize stock across all channels.
-
How It Works:
-
Sales data from online and offline channels updates the central inventory system in real time.
-
Customers see accurate stock availability online and in-store.
-
Benefits:
-
Prevents overselling.
-
Ensures consistent customer experiences across all channels.
Real-World Use Case: A Furniture Retailer’s Success
A growing furniture retailer with multiple stores and warehouses struggled to manage their inventory efficiently. Some stores frequently ran out of popular items, while others overstocked products that didn’t sell well. The lack of real-time visibility across locations led to delayed transfers and frustrated customers.
The Solution: The retailer adopted an inventory management software to centralize and streamline their operations. Key features included:
-
Centralized Inventory Data: A unified dashboard provided real-time insights into stock levels across all stores and warehouses.
-
Automated Stock Transfers: The software recommended transferring products from overstocked locations to those with higher demand.
-
Demand Forecasting: Analytics tools predicted demand based on sales trends, helping the retailer optimize stock replenishment.
The Results:
-
Faster Stock Transfers: Inventory was redistributed efficiently, ensuring products were always available where needed.
-
Reduced Stock Discrepancies: Real-time tracking minimized errors and improved stock accuracy.
-
Improved Customer Satisfaction: Customers received their products faster, whether shopping online or in-store.
Key Features to Look for in Multi-Location Inventory Software
-
Centralized Dashboard: Provides an overview of inventory levels, sales performance, and stock movements across all locations.
-
Real-Time Updates: Ensures accurate tracking of inventory as it moves between sites.
-
Automated Replenishment: Simplifies restocking and reallocation processes with automated alerts and workflows.
-
Demand Forecasting: Helps plan stock levels based on historical trends and anticipated demand.
-
Scalability: Supports growing businesses by seamlessly adding new locations and sales channels.
Benefits of Optimized Multi-Location Inventory Management
-
Reduced Operational Costs: Balancing inventory across locations minimizes excess stock and reduces carrying costs.
-
Better Customer Experiences: Ensuring stock availability at all locations improves delivery times and customer satisfaction.
-
Streamlined Operations: Centralized systems eliminate manual errors and reduce administrative overhead.
-
Increased Sales Opportunities: Proper stock distribution ensures that no sales are lost due to stockouts.
-
Faster Decision-Making: Real-time insights enable quick responses to demand fluctuations and supply chain disruptions.
Conclusion: A Smarter Approach to Multi-Location Inventory
Managing inventory across multiple locations doesn’t have to be a logistical nightmare. With the right inventory management software, businesses can centralize operations, optimize stock levels, and ensure timely product availability for customers.
The success of the furniture retailer highlights the transformative impact of inventory tools in a multi-location setting. By investing in the right software, businesses can streamline their supply chains, reduce costs, and deliver consistent customer experiences across all channels.
Ready to optimize your multi-location inventory? Start exploring solutions that fit your business needs and unlock greater efficiency today.
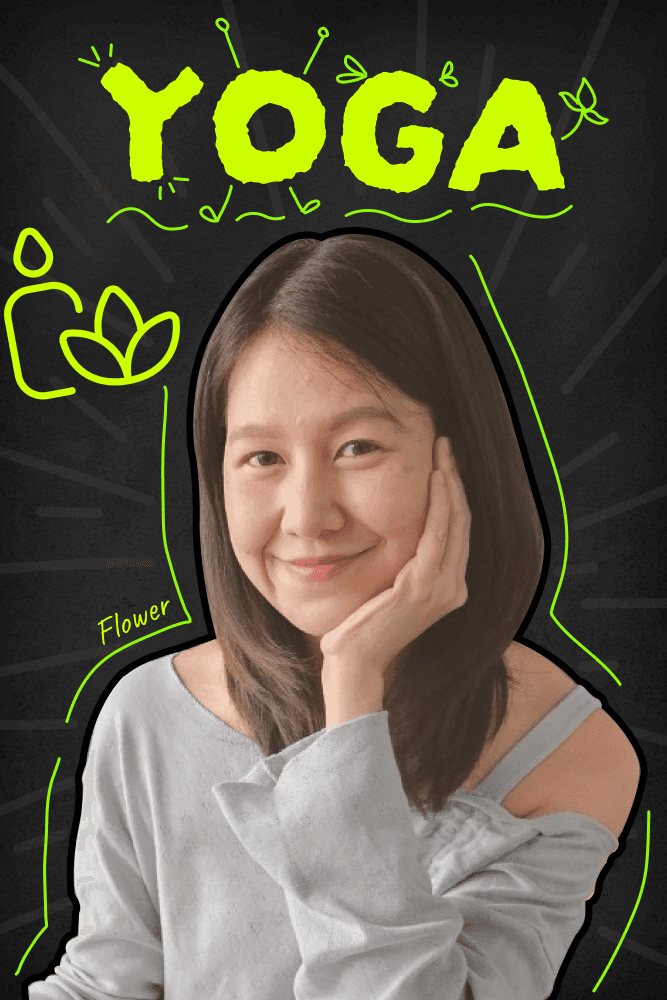
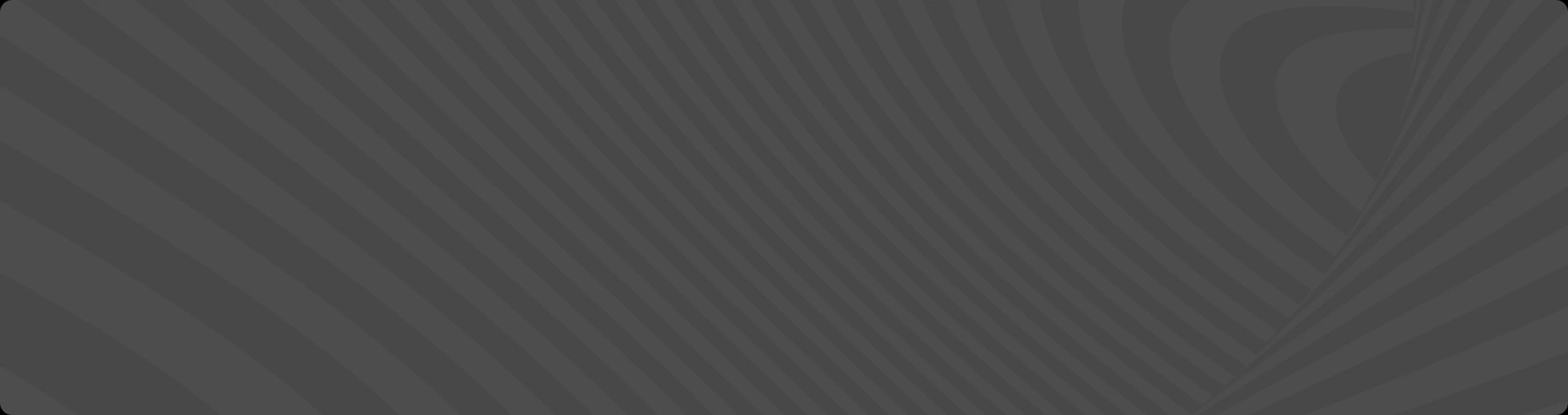
Subscribe to follow product news, latest in technology, solutions, and updates
Other articles for you
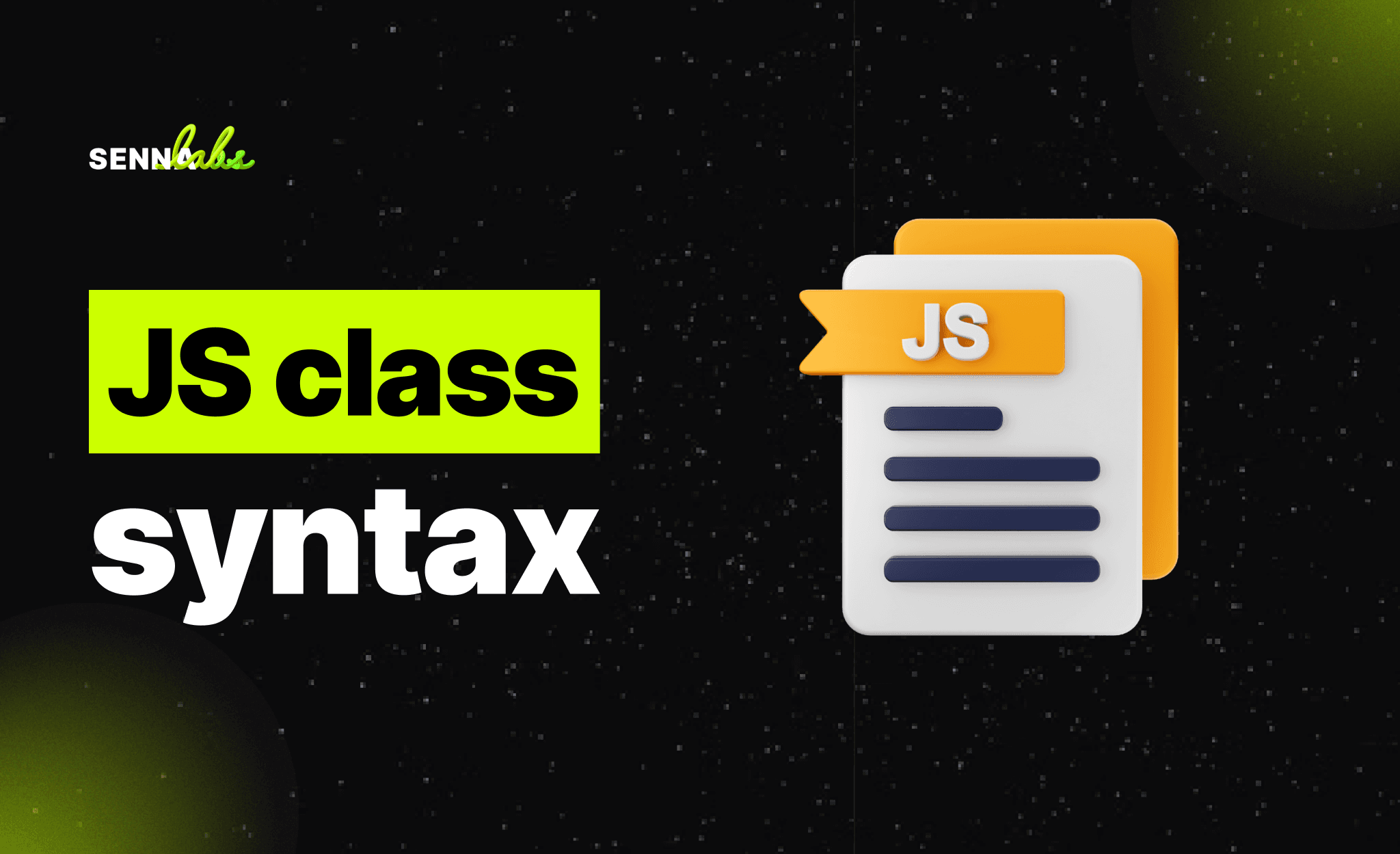
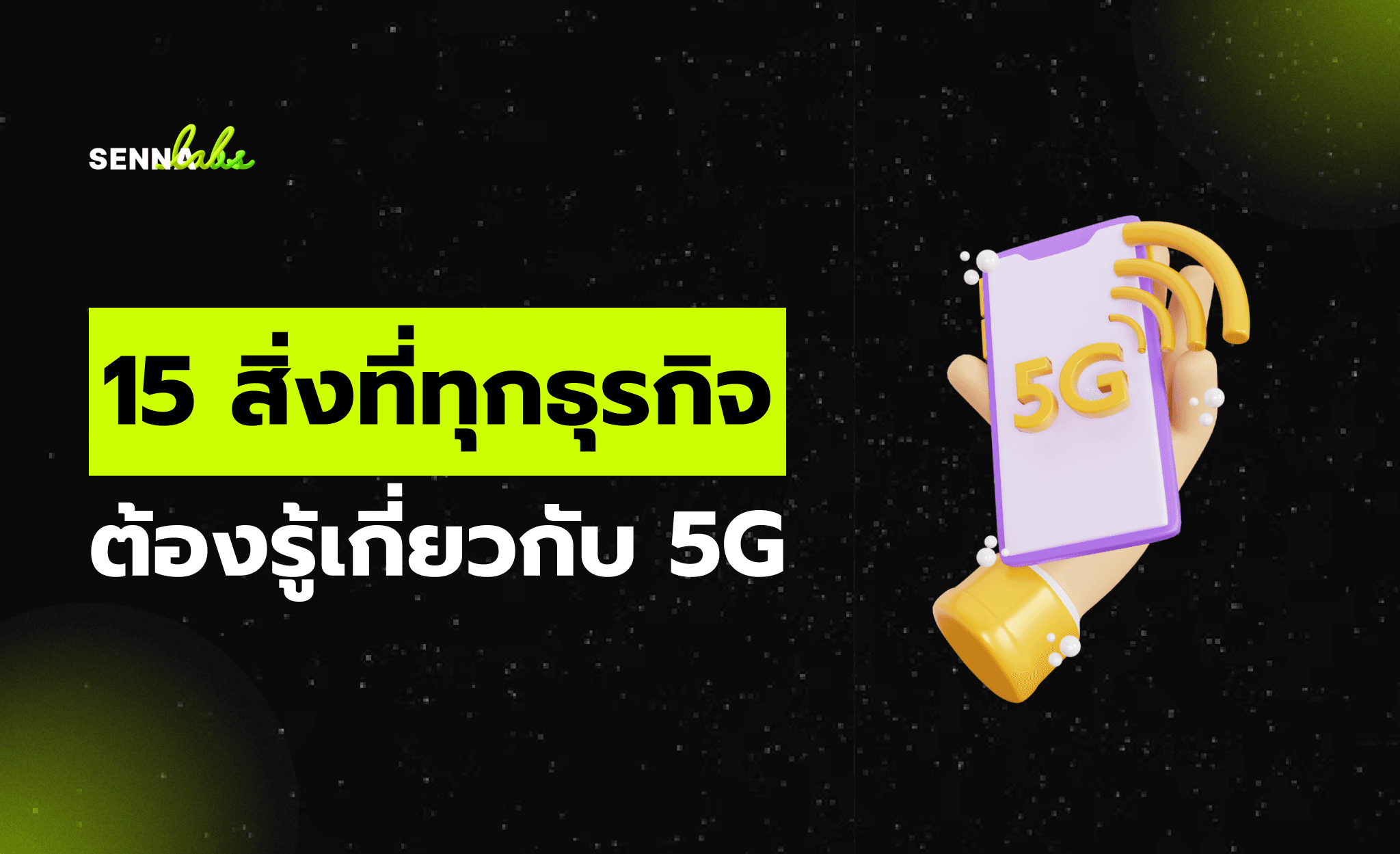
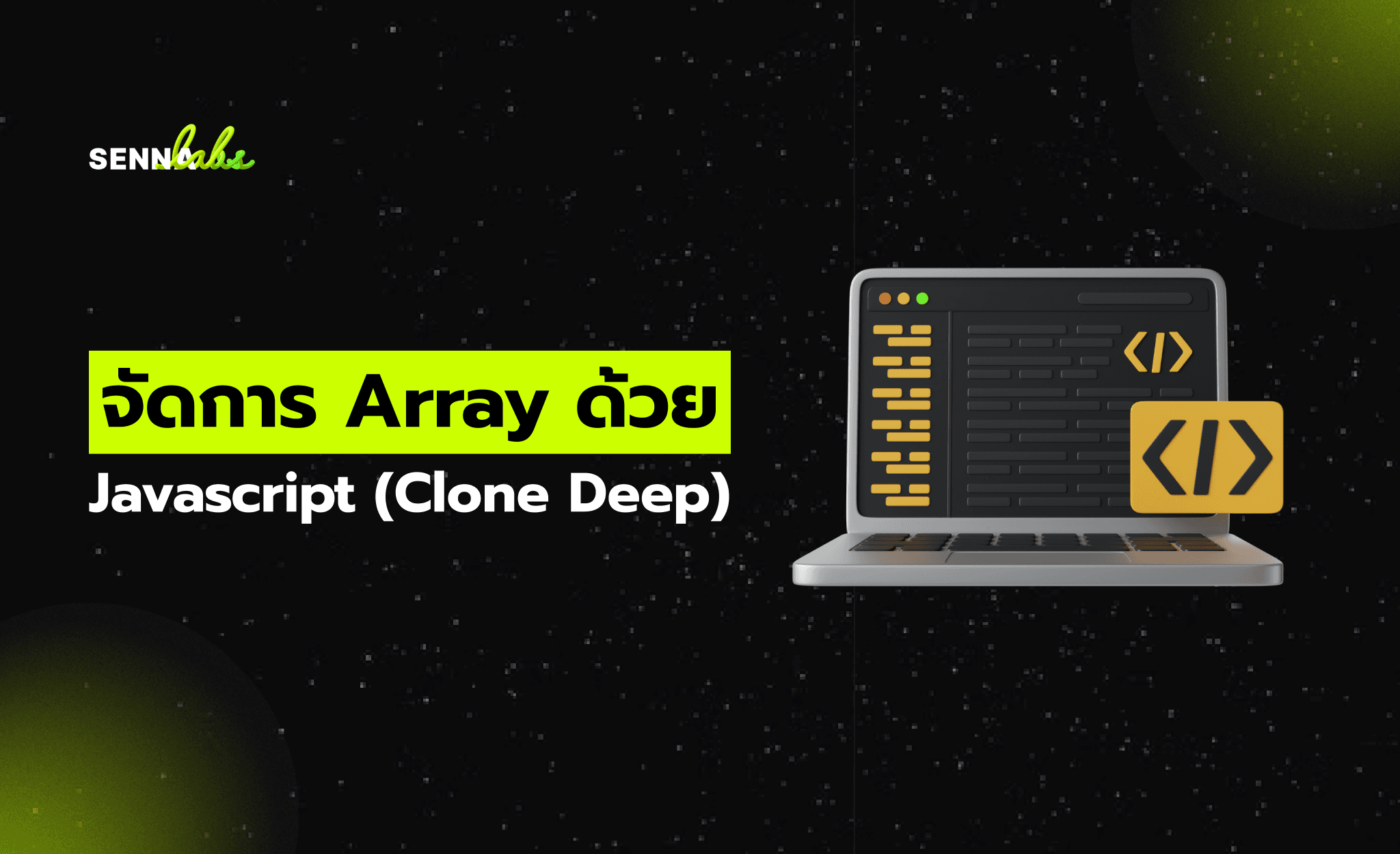
Let’s build digital products that are simply awesome !
We will get back to you within 24 hours!Go to contact us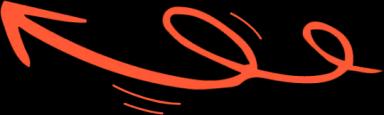
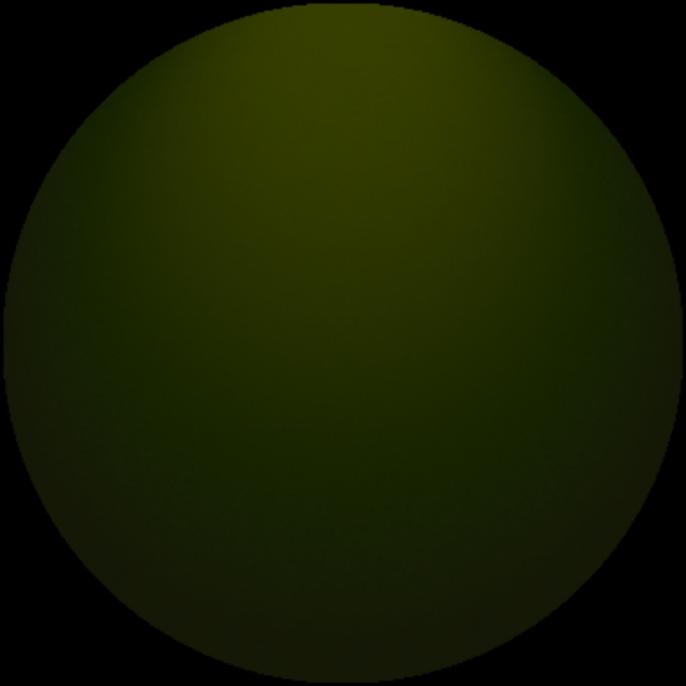
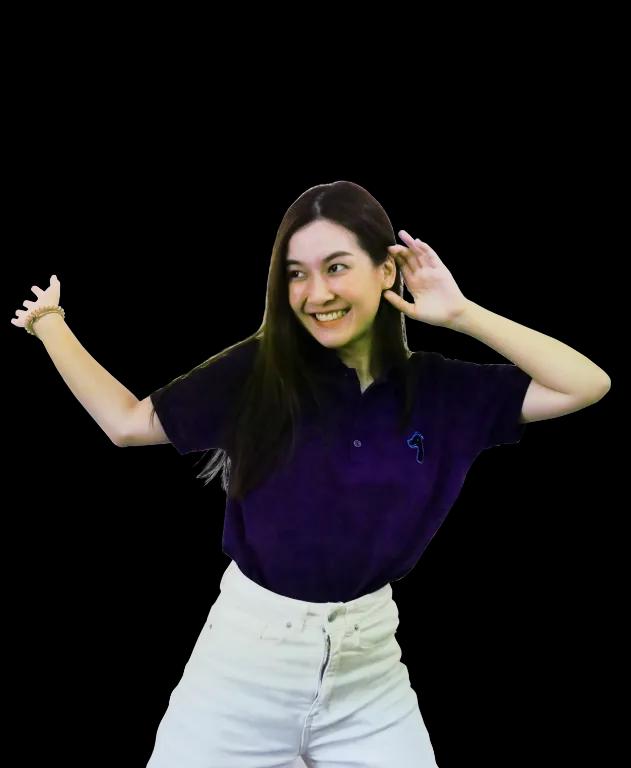
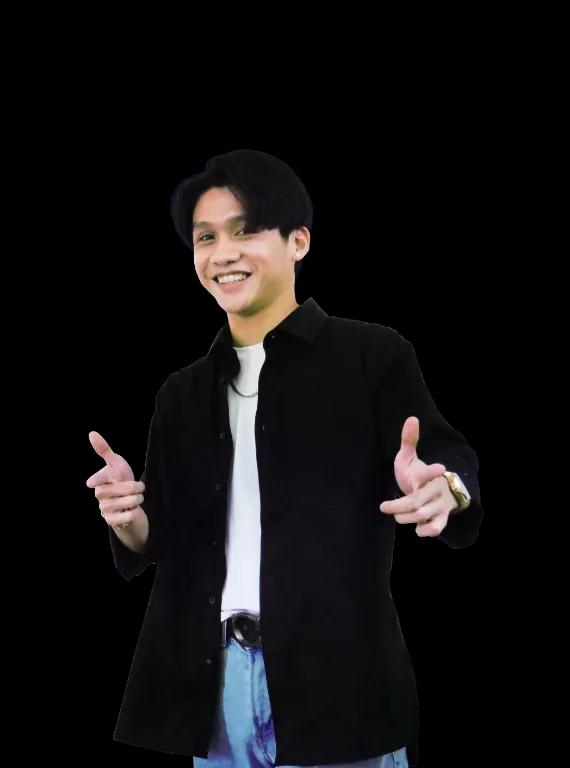
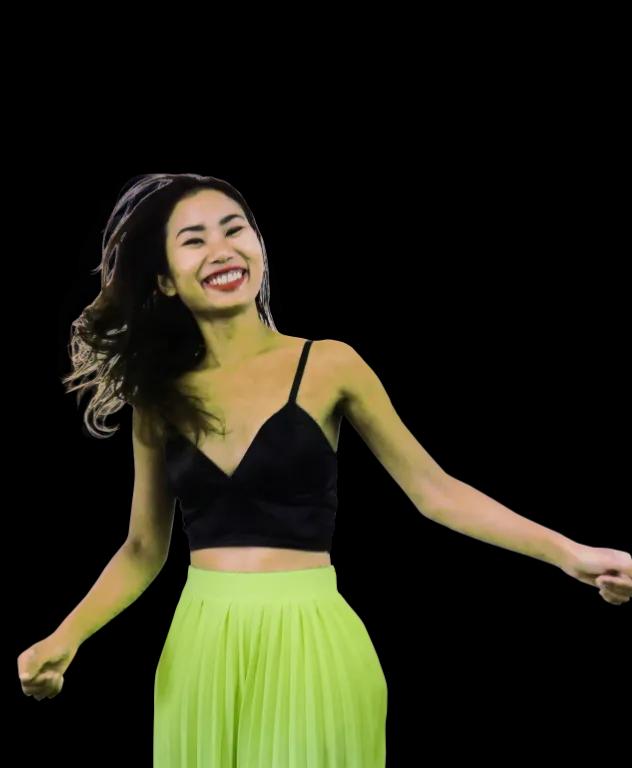
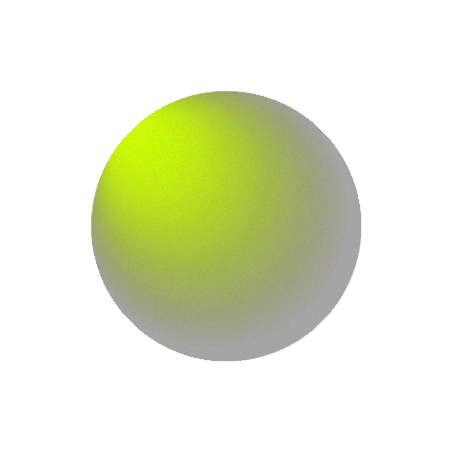
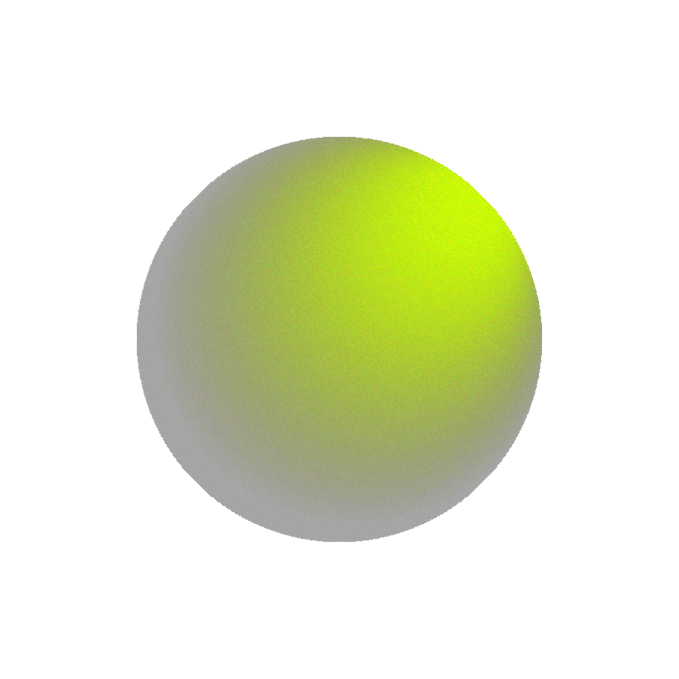
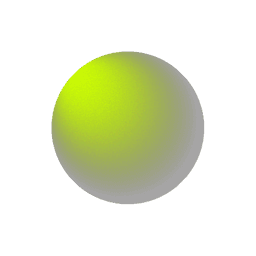
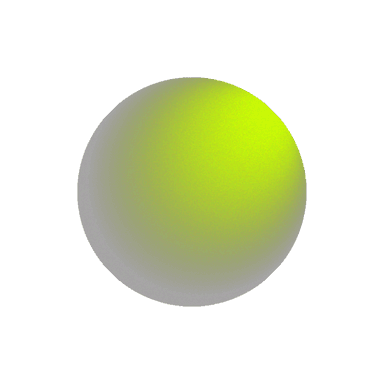
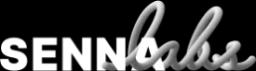