Manufacturing Software Solutions: Transforming the Future of Industry

In the rapidly evolving landscape of manufacturing, staying competitive requires leveraging advanced technologies that streamline operations, enhance productivity, and ensure quality. Manufacturing software solutions have become indispensable tools that enable businesses to achieve these goals. This article delves into the various types of manufacturing software solutions, their benefits, and how they can transform the manufacturing industry.
Types of Manufacturing Software Solutions
-
Enterprise Resource Planning (ERP) Systems: ERP systems integrate various business processes into a unified platform, including finance, human resources, supply chain, and manufacturing operations. This integration enhances data visibility, improves decision-making, and boosts overall efficiency.
-
Manufacturing Execution Systems (MES): MES software manages and monitors production processes in real-time. It collects data from the shop floor, provides insights into production performance, and helps in optimizing operations to ensure that manufacturing goals are met.
-
Computer-Aided Design (CAD) and Computer-Aided Manufacturing (CAM): CAD software allows engineers to create detailed 3D models of products, while CAM software translates these designs into instructions for manufacturing equipment. Together, they streamline the design-to-production process and improve product quality.
-
Product Lifecycle Management (PLM): PLM software manages the entire lifecycle of a product from inception, through engineering design and manufacturing, to service and disposal. It ensures that all stakeholders have access to up-to-date product information, facilitating collaboration and innovation.
-
Supply Chain Management (SCM) Systems: SCM software optimizes the flow of goods, information, and finances across the entire supply chain. It helps in managing inventory, demand forecasting, procurement, and logistics, ensuring that materials and products are available when needed.
-
Quality Management Systems (QMS): QMS software ensures that manufacturing processes comply with industry standards and regulations. It helps in tracking quality metrics, managing non-conformances, and implementing corrective actions to improve product quality.
Benefits of Manufacturing Software Solutions
-
Increased Efficiency and Productivity: By automating routine tasks and providing real-time insights into production processes, manufacturing software solutions help increase efficiency and productivity. This leads to faster production times and reduced operational costs.
-
Improved Quality and Compliance: Quality management and compliance are critical in manufacturing. Software solutions ensure that products meet industry standards and regulations, reducing the risk of defects and recalls.
-
Enhanced Collaboration and Communication: Manufacturing software facilitates better communication and collaboration among different departments and stakeholders. This ensures that everyone is on the same page and working towards common goals.
-
Data-Driven Decision Making: Access to accurate and real-time data enables manufacturers to make informed decisions. Analytics and reporting tools provide valuable insights into production performance, helping in identifying areas for improvement.
-
Scalability and Flexibility: Manufacturing software solutions can be scaled and customized to meet the specific needs of a business. As the business grows, the software can adapt to new challenges and requirements, ensuring continued efficiency and effectiveness.
Implementing Manufacturing Software Solutions
-
Assess Business Needs: Before implementing any software solution, it is essential to assess the specific needs and goals of the business. This involves identifying pain points, process inefficiencies, and areas that require improvement.
-
Choose the Right Solution: Selecting the appropriate software solution is crucial. Consider factors such as functionality, scalability, ease of integration, and cost. It is also important to choose a solution that aligns with the company’s long-term strategic goals.
-
Plan and Execute Implementation: A well-structured implementation plan is essential for the successful deployment of manufacturing software. This includes setting clear objectives, timelines, and milestones, as well as involving key stakeholders in the process.
-
Train Employees: Adequate training ensures that employees are comfortable using the new software and can leverage its full potential. Continuous support and training should be provided to keep up with software updates and new features.
-
Monitor and Optimize: Post-implementation, it is important to monitor the performance of the software and gather feedback from users. Regular reviews and optimizations ensure that the software continues to meet business needs and drives continuous improvement.
Case Studies and Success Stories
-
Automotive Manufacturing: An ERP system helped an automotive manufacturer integrate their supply chain, production, and financial processes. This led to improved inventory management, reduced production costs, and enhanced decision-making capabilities.
-
Electronics Manufacturing: A MES solution enabled an electronics manufacturer to monitor production in real-time, identify bottlenecks, and implement process improvements. As a result, they achieved higher production efficiency and reduced downtime.
-
Food and Beverage Industry: A QMS implementation in a food processing plant ensured compliance with food safety regulations. The system tracked quality metrics and non-conformances, leading to improved product quality and customer satisfaction.
-
Chemical Manufacturing: A PLM system was implemented in a chemical manufacturing company to manage the lifecycle of their products. This included managing complex formulations, regulatory compliance, and safety data. The system enhanced collaboration between R&D and production teams, leading to faster time-to-market and improved product innovation.
Conclusion
Manufacturing software solutions are transforming the industry by providing tools that enhance efficiency, quality, and collaboration. By leveraging these technologies, manufacturers can stay competitive, meet customer demands, and drive innovation. As the industry continues to evolve, investing in the right software solutions will be crucial for achieving long-term success.

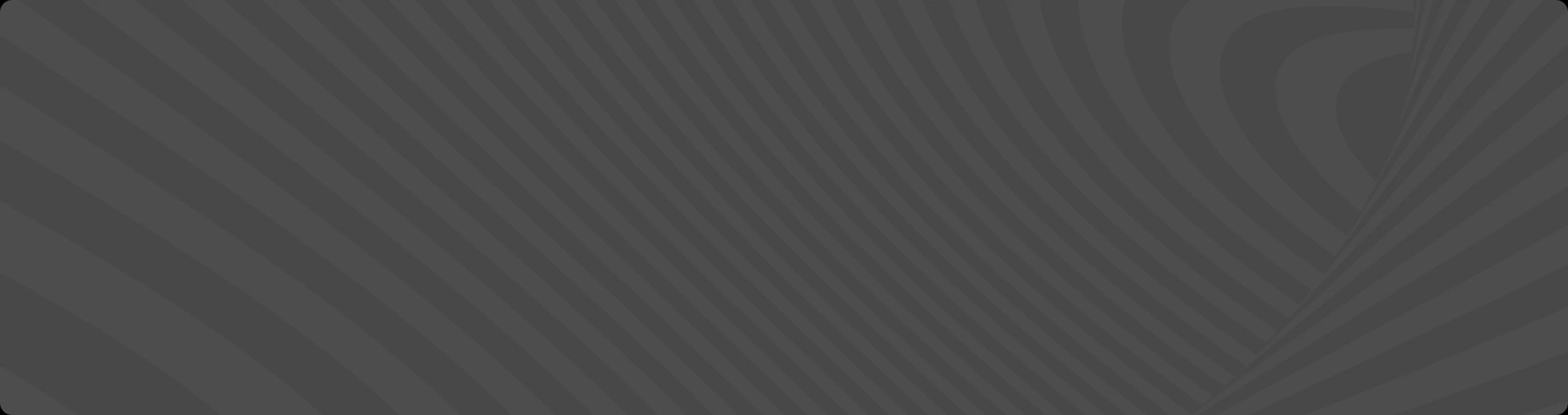
Subscribe to follow product news, latest in technology, solutions, and updates
Other articles for you
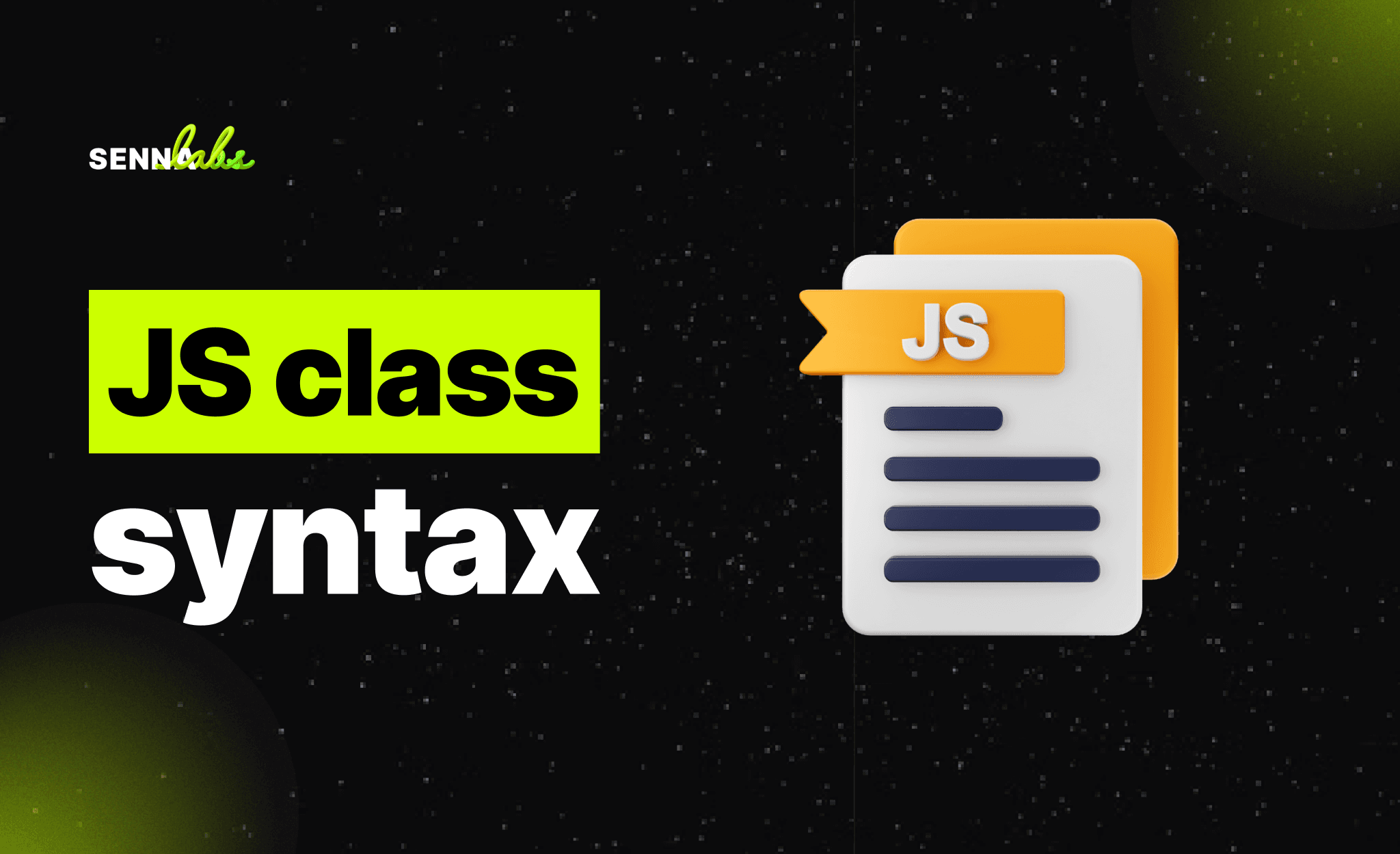
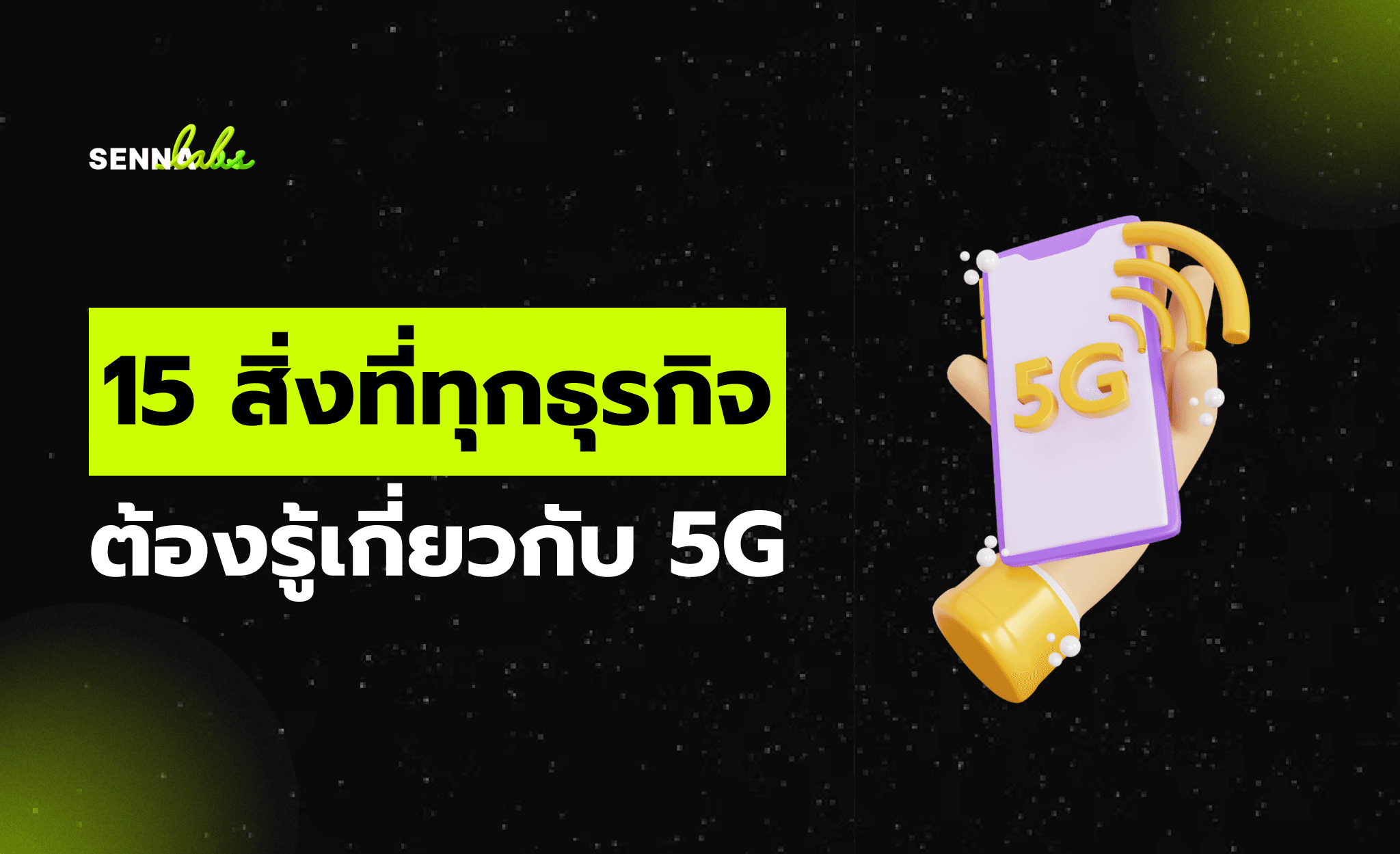
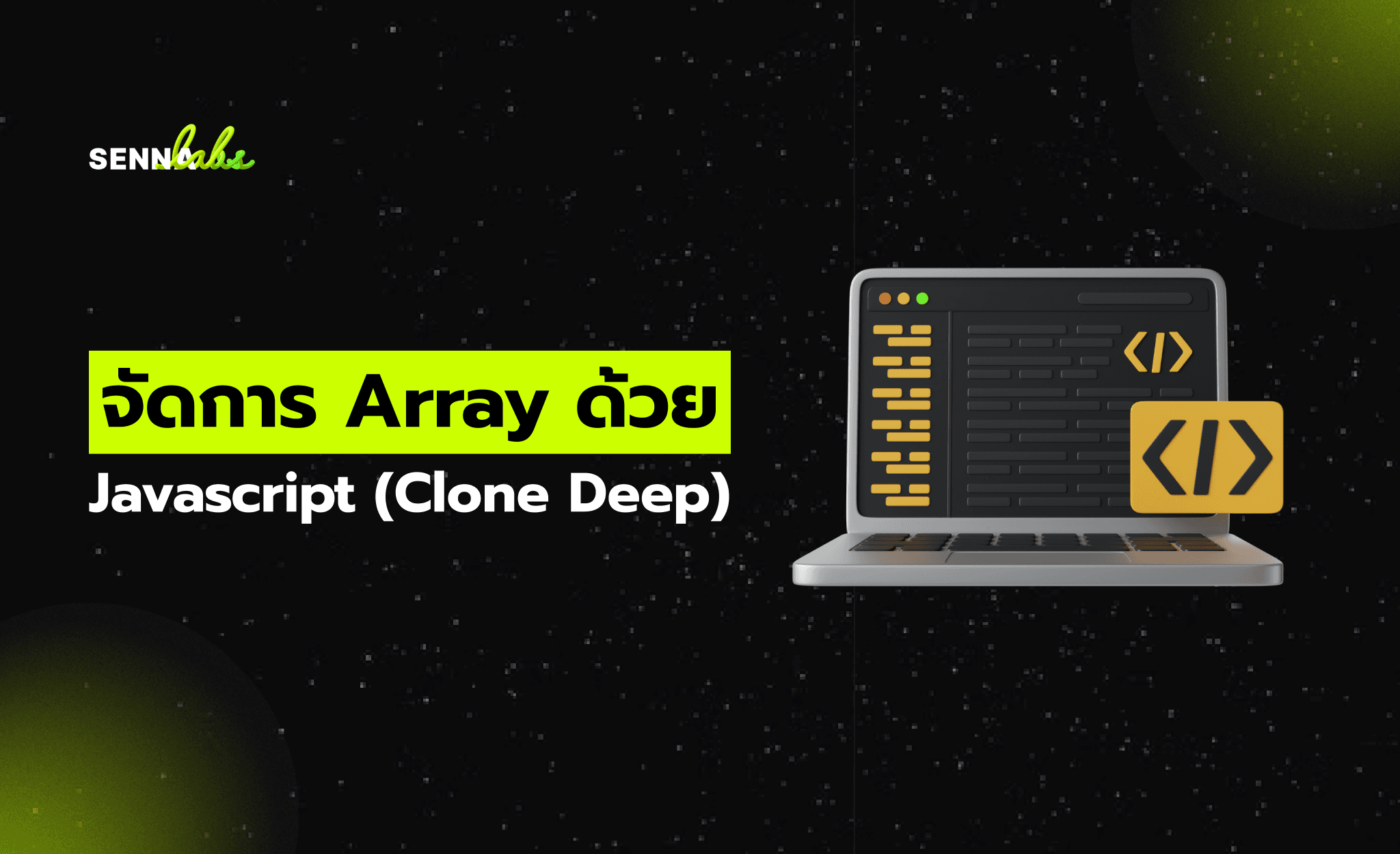
Let’s build digital products that are simply awesome !
We will get back to you within 24 hours!Go to contact us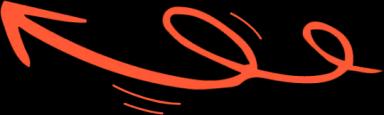
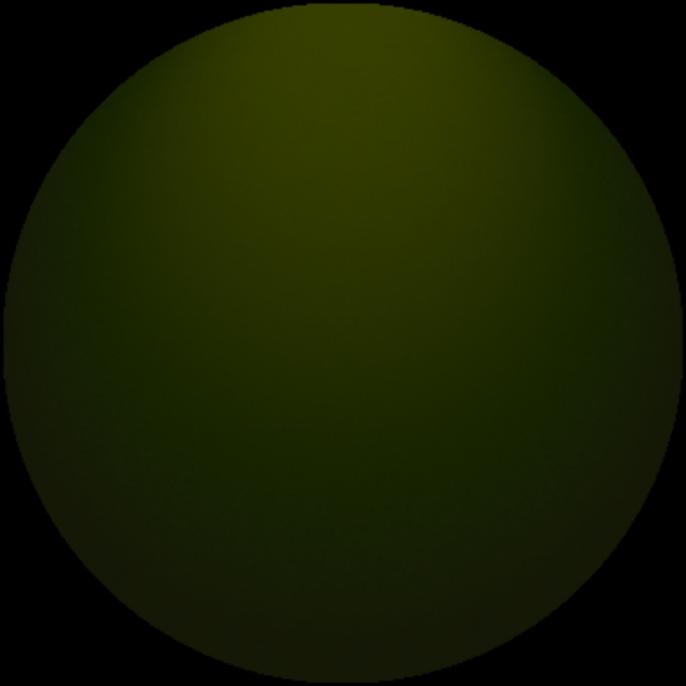
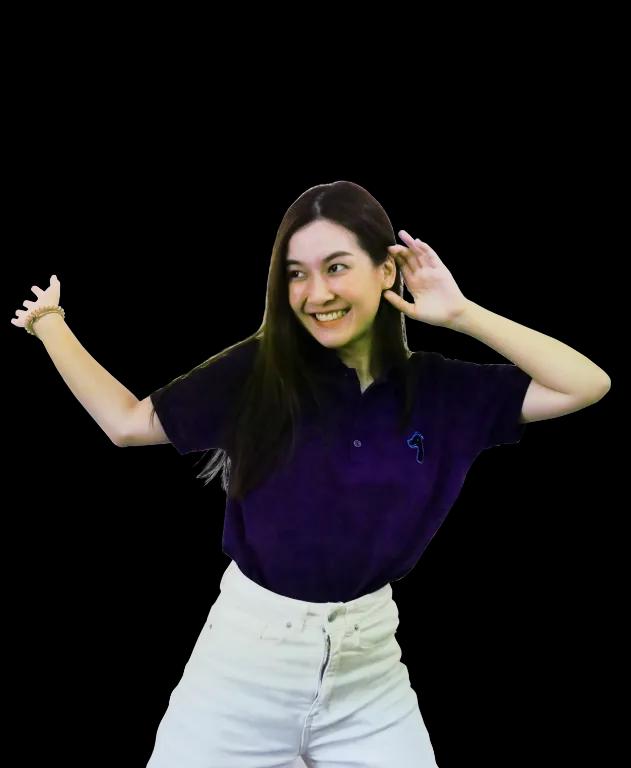
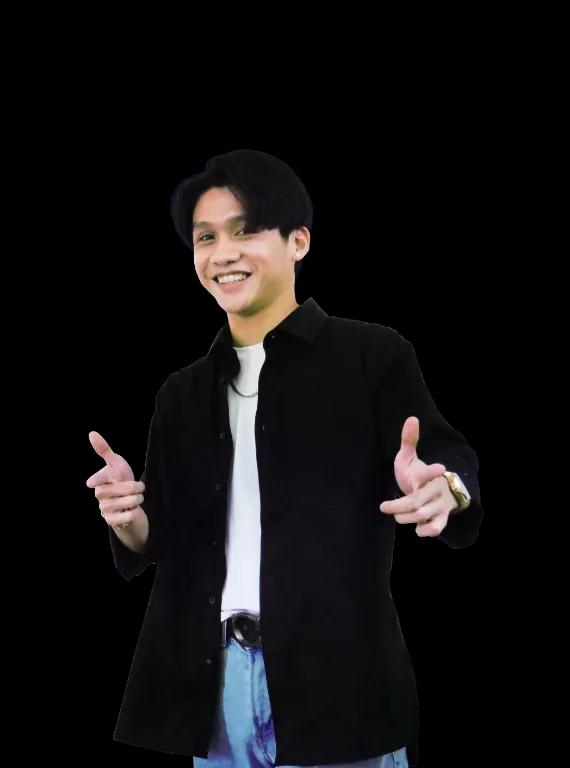
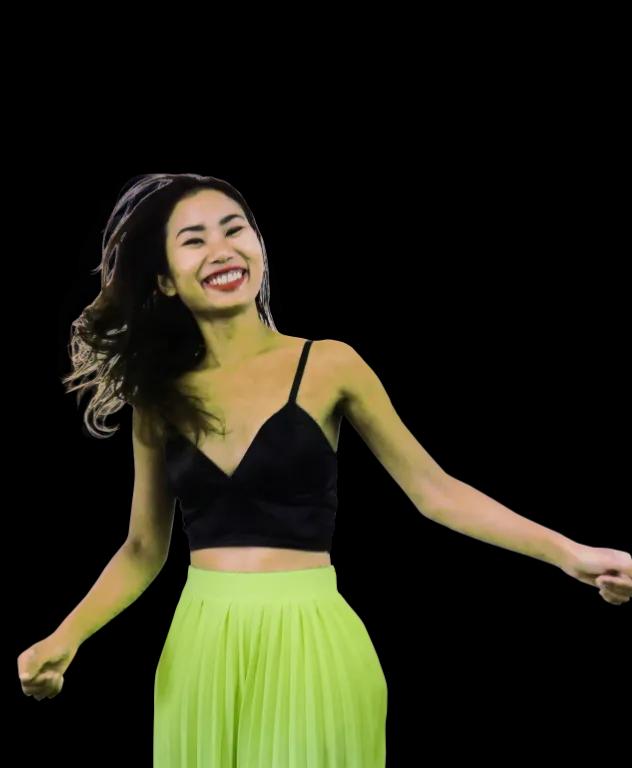
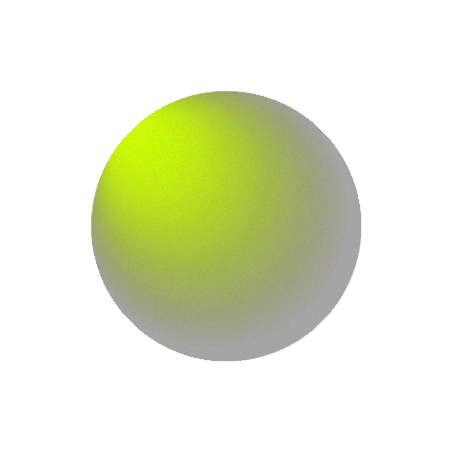
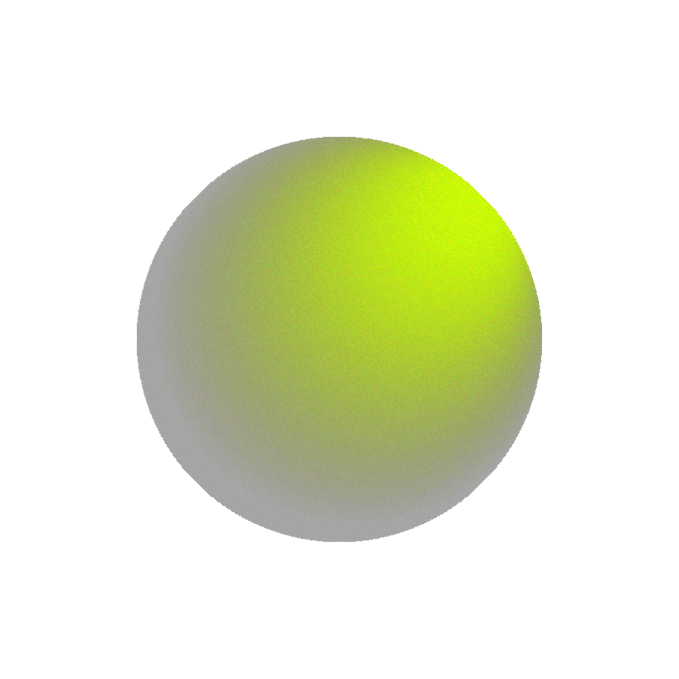
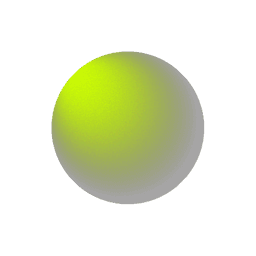
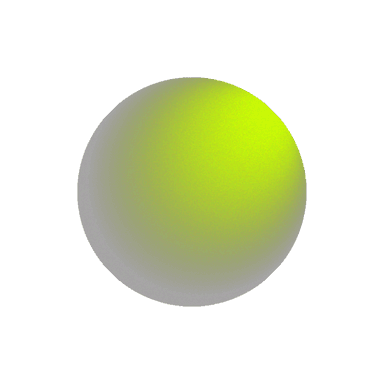
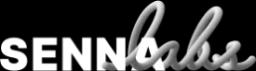