Case Study: Predictive Maintenance Platform Drives Operational Excellence for Global Manufacturing Leader
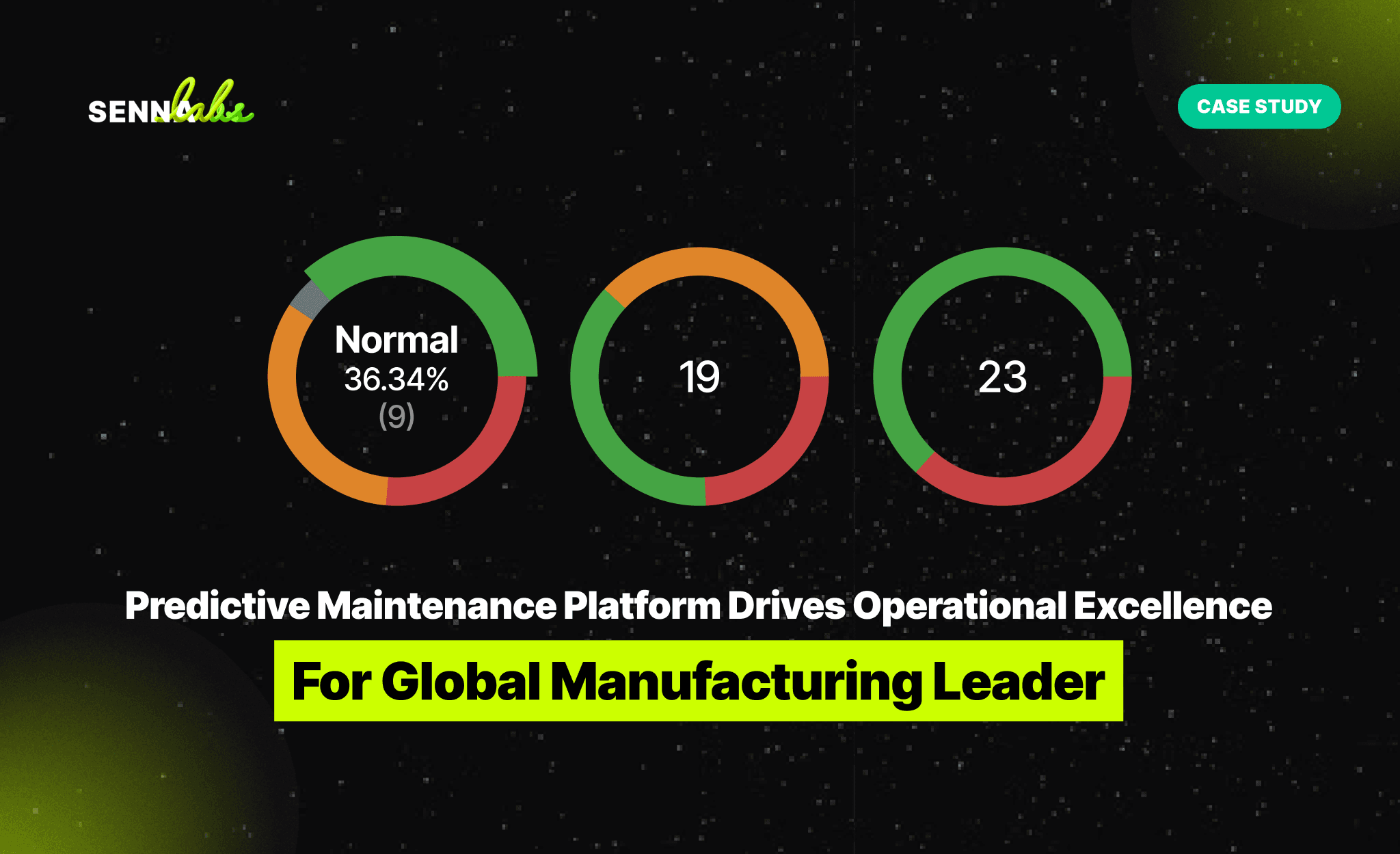
Client: Global Manufacturing Leader
Challenge
A leading multinational manufacturer, renowned for its diverse product portfolio and global reach, faced escalating maintenance costs and unplanned downtime due to equipment failures. Their existing reactive maintenance approach was inefficient, hindering productivity, increasing repair expenses, and creating potential safety risks.
Solution
Senna Labs, a trusted IT consulting firm specializing in custom software development, partnered with the manufacturer to deploy a cutting-edge Predictive Maintenance Platform. This tailored solution leveraged the latest technologies to revolutionize their maintenance operations and optimize asset performance.
Key Features of the Predictive Maintenance Platform
-
Real-Time Data Collection: The platform seamlessly integrates with the manufacturer's diverse array of sensors and equipment, capturing a comprehensive range of real-time data on machine performance, including temperature, vibration, pressure, and other critical parameters.
-
Advanced Analytics & Machine Learning: Leveraging sophisticated machine learning algorithms, the platform analyzes this vast data stream to identify subtle patterns, anomalies, and trends that could signal potential equipment failures.
-
Early Failure Detection: By recognizing these early warning signs, the platform empowers maintenance teams to proactively address issues before they escalate into costly breakdowns.
-
User-Friendly Interface: The platform's intuitive interface allows maintenance personnel at all levels to easily access and interpret data, schedule tasks, and monitor equipment health.
-
Scalability and Adaptability: The platform is designed to seamlessly scale with the manufacturer's expanding operations and can readily adapt to incorporate new equipment and technologies.
Results
The implementation of Senna Labs' Predictive Maintenance Platform delivered substantial benefits to the global manufacturing leader:
-
Reduced Downtime: Unplanned downtime was significantly reduced, leading to a substantial increase in productivity and output.
-
Lower Maintenance Costs: By shifting from a reactive to a proactive maintenance approach, the manufacturer achieved significant cost savings in annual maintenance expenditures.
-
Improved Asset Lifespan: Early detection and timely maintenance extended the lifespan of critical equipment, minimizing the need for costly replacements.
-
Enhanced Safety: Proactive maintenance helped prevent equipment failures that could pose safety risks to employees, creating a safer work environment.
-
Data-Driven Decision Making: The platform's analytics capabilities provided valuable insights into equipment performance, enabling the manufacturer to optimize their maintenance strategies and make informed, data-driven decisions.
Conclusion
This case study demonstrates the transformative power of custom software solutions in the manufacturing sector. By leveraging predictive maintenance technology, Senna Labs empowered a global manufacturing leader to achieve operational excellence, reduce costs, and enhance safety.
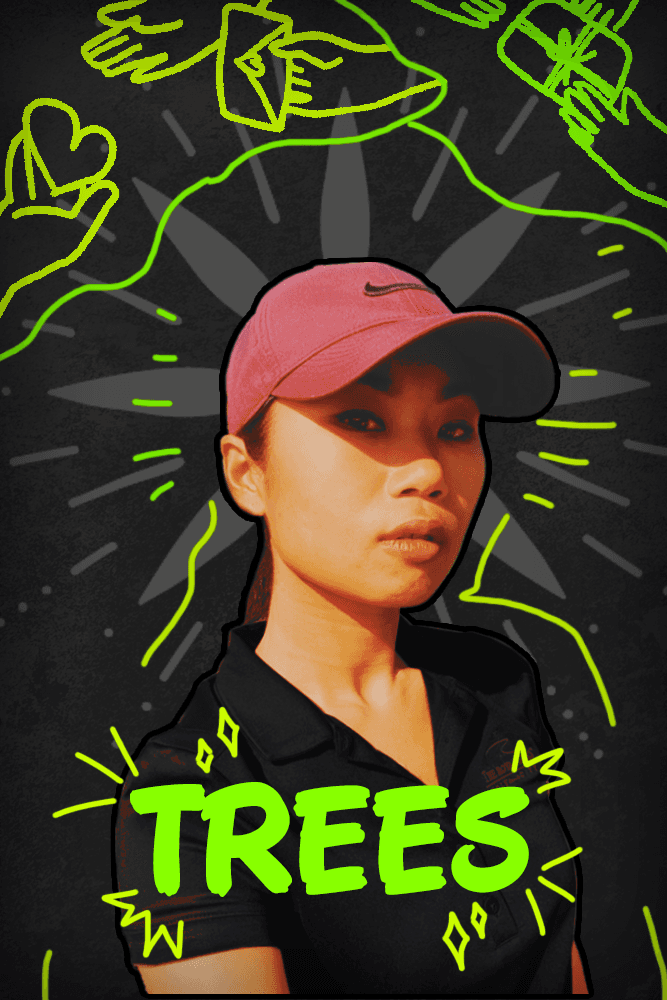
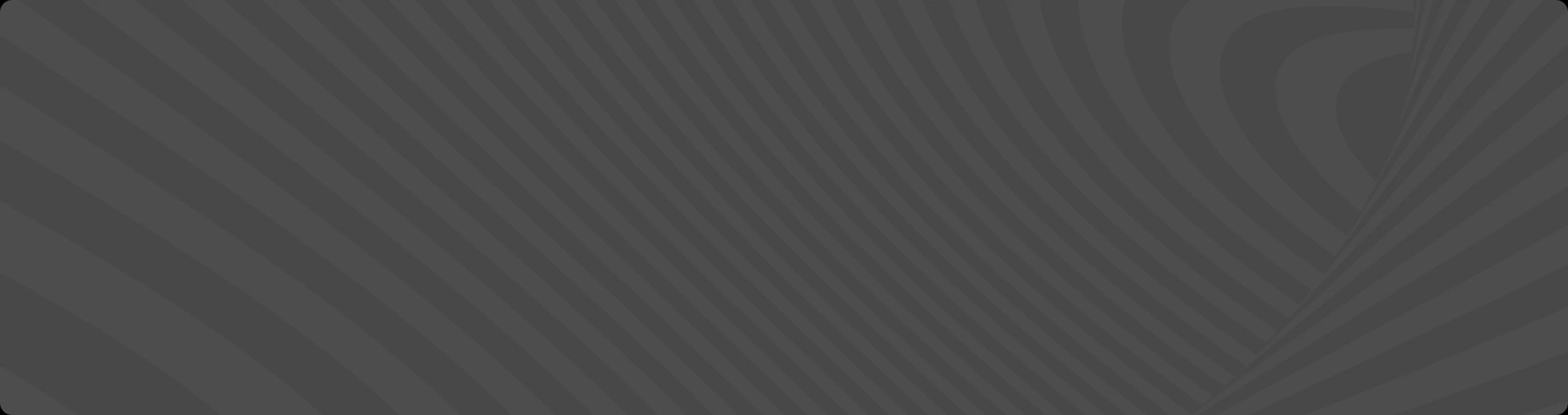
Subscribe to follow product news, latest in technology, solutions, and updates
Other articles for you
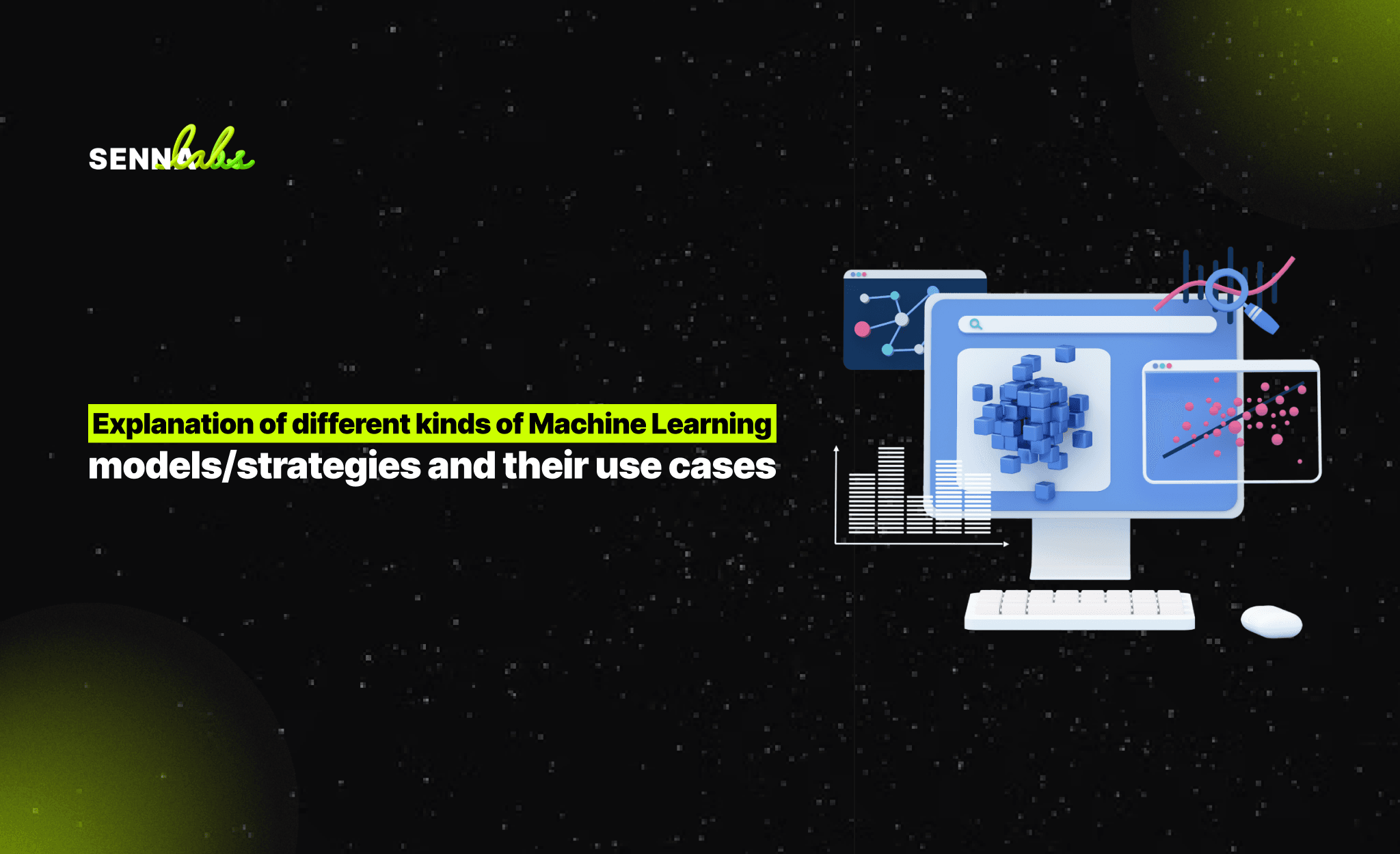
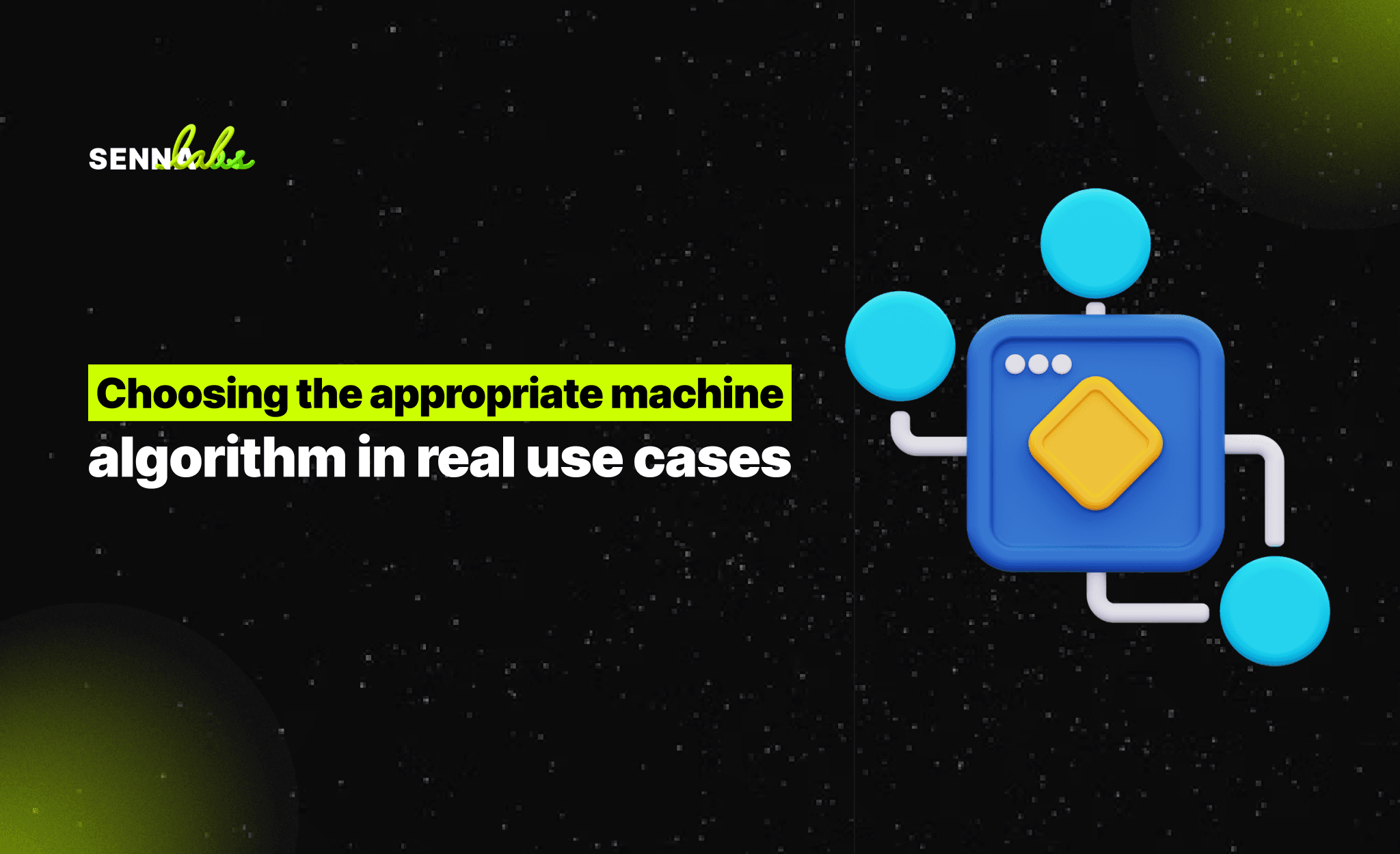
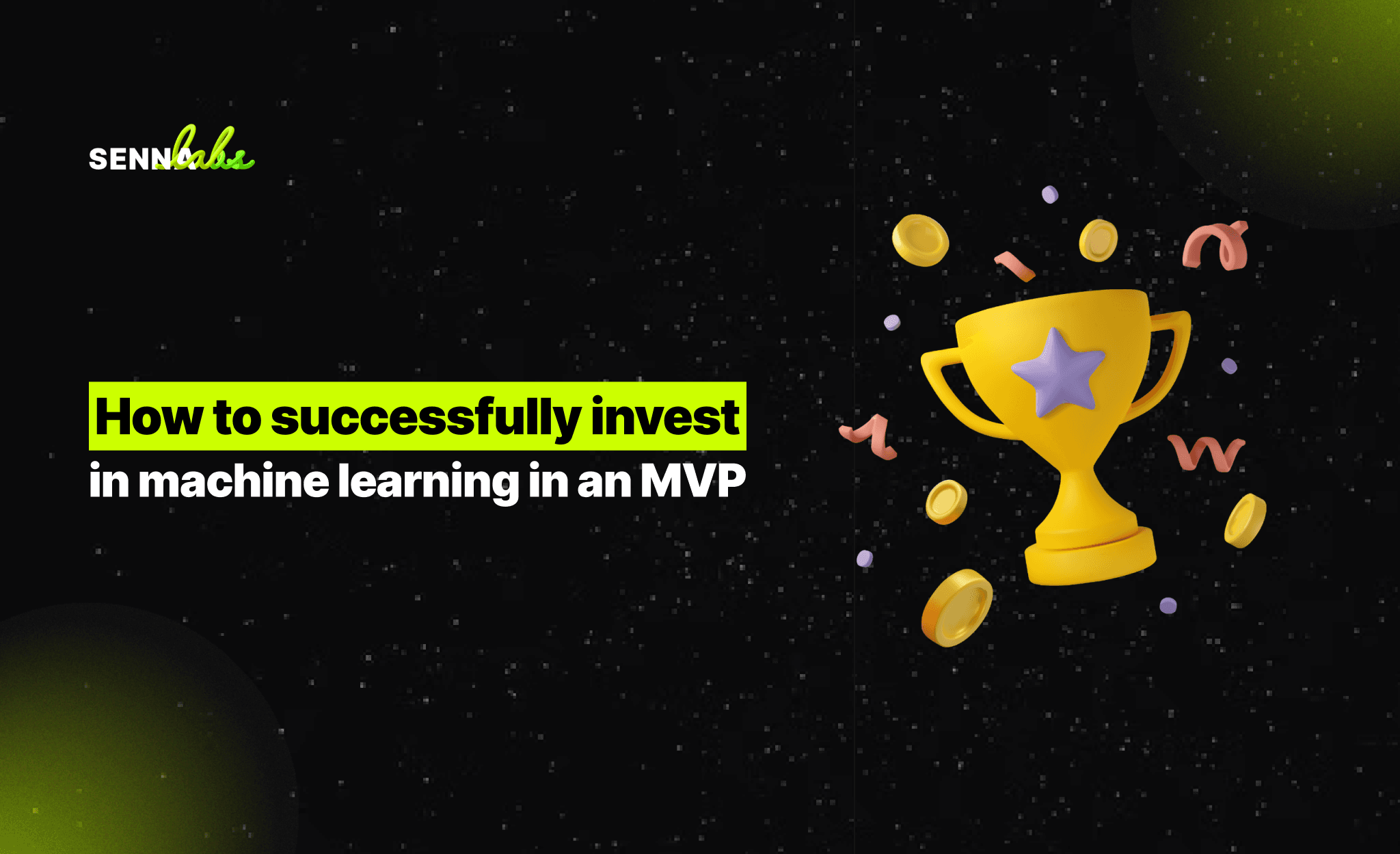
Let’s build digital products that are simply awesome !
We will get back to you within 24 hours!Go to contact us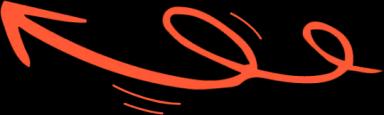
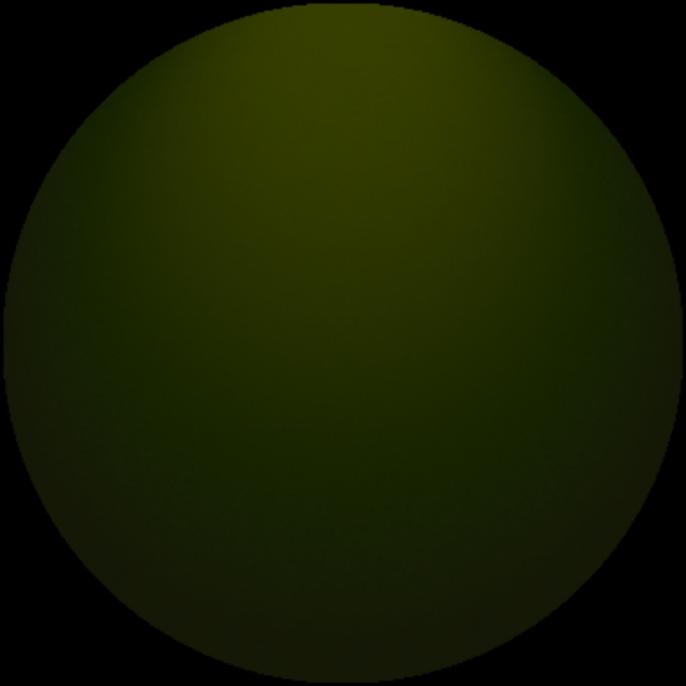
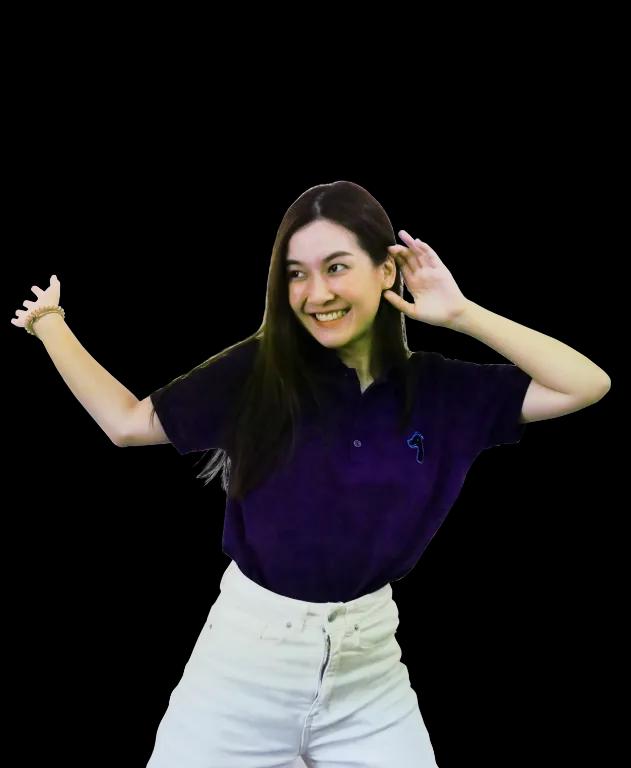
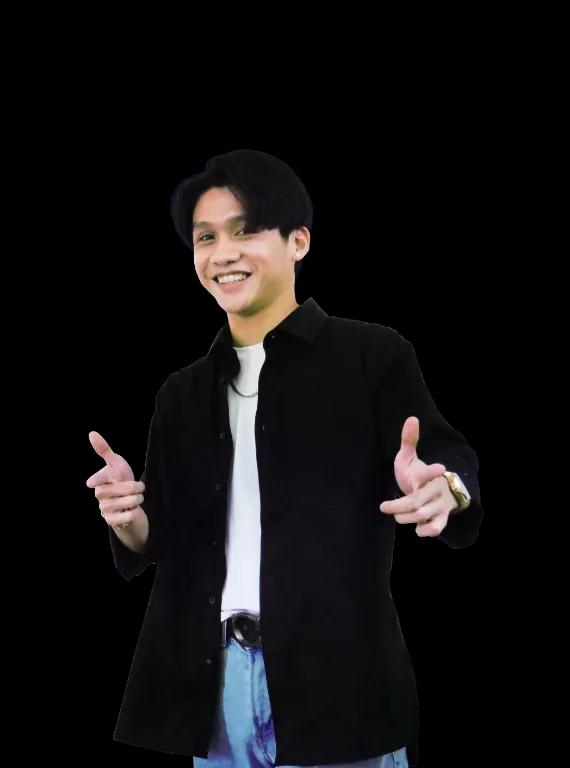
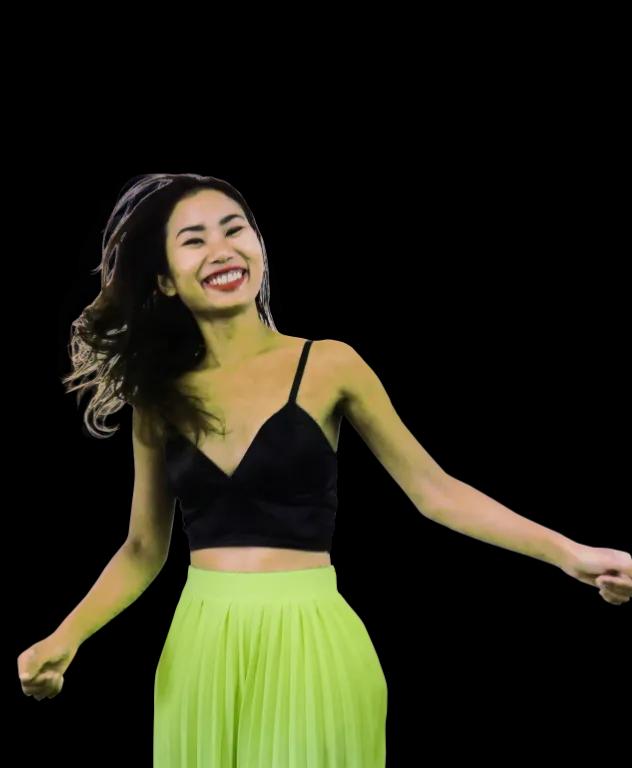
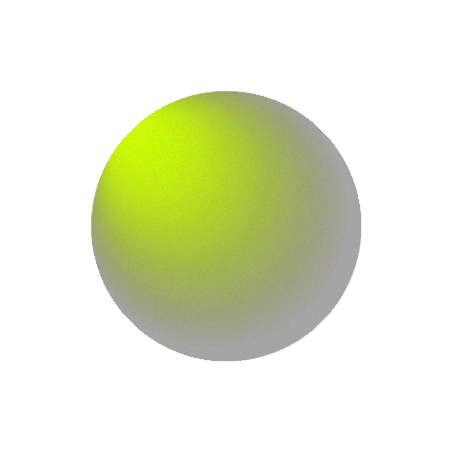
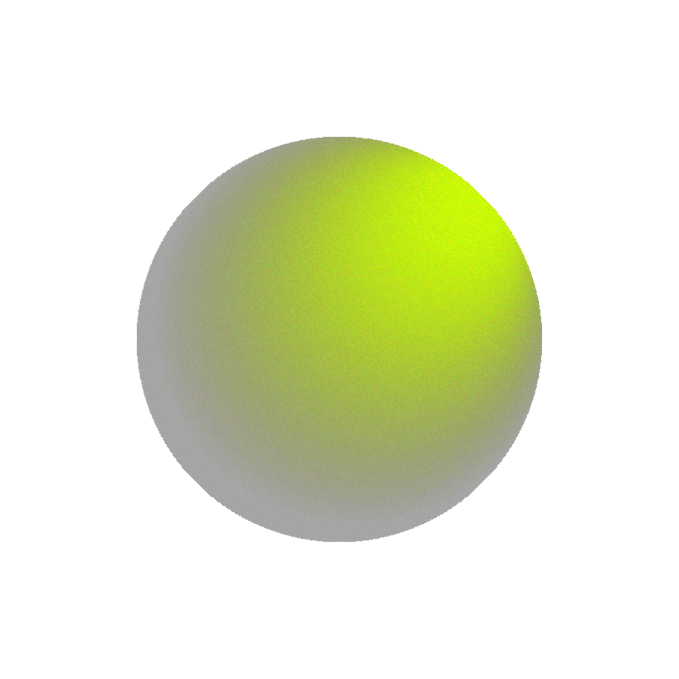
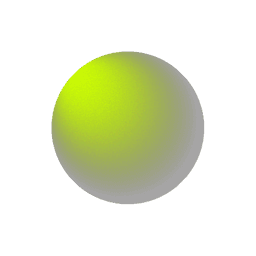
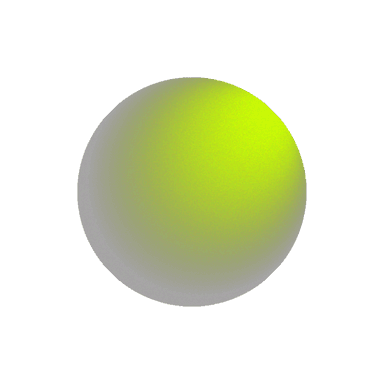
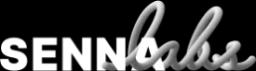